Guangdong Shanying: dedicated to intelligent, low-carbon manufacturing
Dec 13, 2023
With their new PM 52 and PM 53 lines, Guangdong Shanying aims to meet their low-carbon goals while setting industry benchmarks for intelligent manufacturing. Close cooperation with Valmet has enabled rapid start-up and exceptional efficiency.
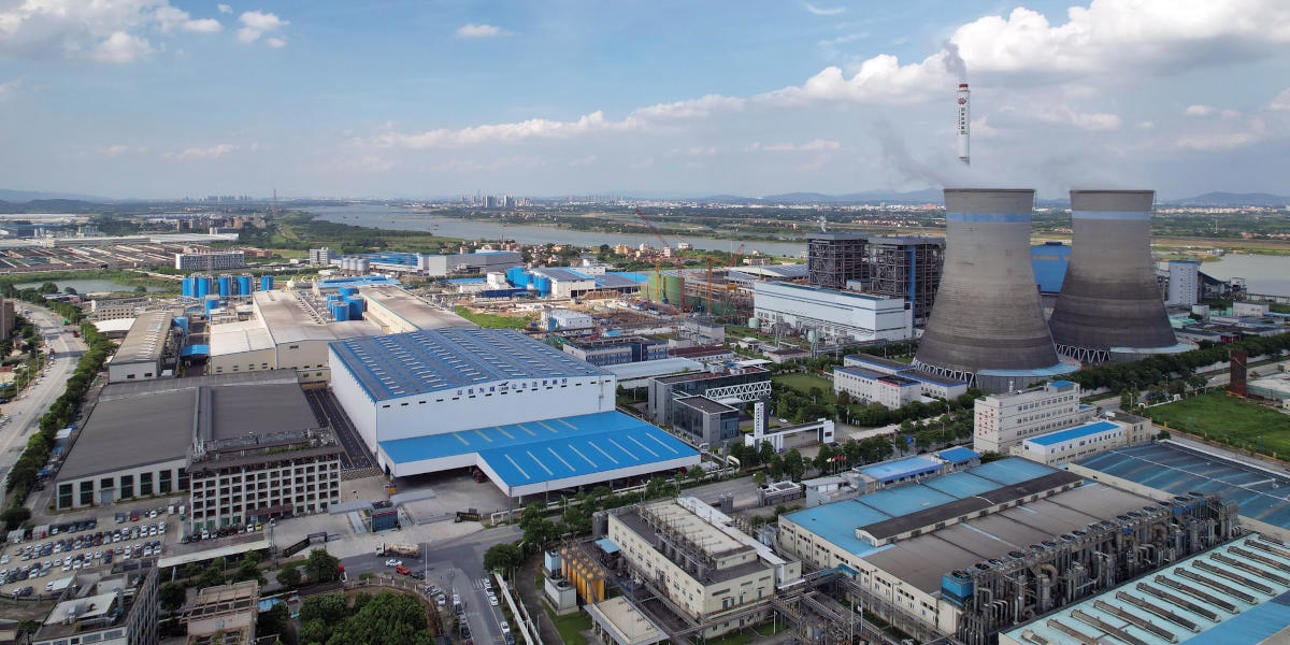
In 2022, Shanying Paper Industry (Guangdong) Co., Ltd., also known as Guangdong Shanying, commenced operations of their PM 52 and PM 53 production lines at their Zhaoqing mill in China. Both lines manufacture products that prioritize light weight, low-carbon and efficiency improvement, and both are capable of production speeds of up to 1,200 meters per minute. The ultimate goal is for Guangdong Shanying to become an eco-intelligent paper mill with an annual production capacity of one million tonnes. This aligns with Shanying Group’s mission of “making life better through paper” and its vision of becoming a global leading provider of integrated green solutions that create long-term value for customers.
Dedicated to high-quality packaging
In the past, the company focused on the production of high-permeability, high-strength paper bag base paper, for bag packaging in the chemical and mortar industries. Today, the main focus is on container board packaging. “The long-term demand for packaging paper is expected to rise steadily, however domestic packaging paper companies face immense pressure. We are actively strengthening lean production and energy efficiency management practices, striving to deliver top-notch packaging paper that meets the needs of our customers,” says Wang Lihai, General Manager, Guangdong Shanying.
Wang Lihai, General Manager, Guangdong Shanying.
Yin Kai, Assistant General Manager of Guangdong Shanying.
Working together to reduce emissions
Shanying International prioritized green development and intelligent manufacturing during the investment stage and, after extensive discussions with Valmet about carbon reduction technology, they implemented numerous energy efficient solutions, for instance in the press section design, forming section operation, and in sizing and calendering. “As a supplier that combines process technology, automation and service, Valmet played a crucial role during the project implementation process,” says Wang Lihai. “The performance and overall outcome during the commissioning process and after start-up have been exceptional.”
Guangdong Shanying PM 53.
High dryness after pressing
Yin Kai, Assistant General Manager of Guangdong Shanying, highlights the excellent performance of the OptiPress Linear in PM 52, which achieves high dryness after pressing. “This reduces the likelihood of paper breaks and minimizes steam consumption, resulting in energy savings and increased efficiency. The specially designed transfer suction roll also helps prevent edge drifting and web tearing during operation, greatly improving running performance.” He also highlights the advantages of the installed base winder. “The compact design of the base winder with subfloor installation solution takes up less space and has a good vibration damping effect and overall operating stability. A single winder can meet the needs of a single production line. Additionally, the final paper roll has neat ends and less bottom and paper tail losses.”
The production lines PM 52 and PM 53 mark the 10th and 11th installations for Shanying International.
Rapid achievement of many targets
Lei Pengkang, PM 52 Manager, says, “PM 52 began paper production on the same day it was started up. After approximately two hours of process optimization and adjustment, the products met the sales standards. The machine achieved continuous production shortly after that. Since the start-up, it has been running smoothly, and the products have received unanimous praise from customers. The consumption of water, electricity and steam has been lower than expected, reaching the industry’s best consumption levels.”
We are actively strengthening lean production and energy efficiency management practices.
Pan Lingjun, PM 53 Manager, adds, “PM 53’s production level is outstanding compared to similar paper machines and is very stable. This is due to the highly integrated and modular design of Valmet’s paper machine, which allows us to easily identify and handle various production situations. It is easy to maintain and highly automated, so that workers can quickly adapt to its operation after a short training period.”
Outstanding support and collaboration
Ma Hanbing, Assistant General Manager of PM 52 and PM 53, says: “Throughout the construction period, and the installation and commissioning process, Shanying and Valmet collaborated closely. Given the significant profit pressure in the packaging paper market, it was crucial for us to expedite production as soon as possible. Valmet provided exceptional expert support, particularly for PM 53, which achieved production within just three days after commissioning and reached the target speed within 11 days, setting a new world record for similar Valmet paper machines.”
Wang Lihai adds: “Remote support has been immensely valuable to us during the pandemic. For example, during the commissioning of the winder, when Valmet’s European experts were unable to be physically present, Valmet’s online experts provided extensive training and guidance.”
“Valmet and Shanying have been collaborating throughout the project. With the combined wisdom and experience of both parties, we have successfully established Guangdong Shanying’s world-leading lightweight, high-quality packaging paper production line. I sincerely express my gratitude to both teams,” says Liu Hailiang, Director of Project Management for major project operations in China.
Guangdong Shanying PM 52.
Text: Jingyu Xue
Photos: Lu Jun
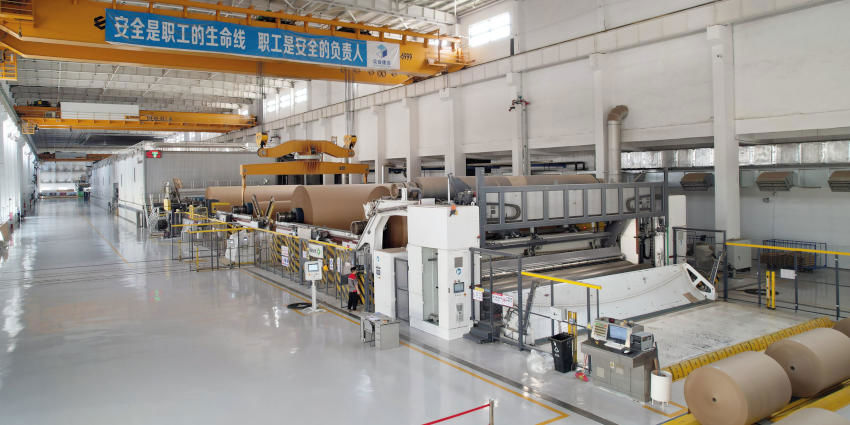
Valmet's fabrics and extensive automation offering enhance production efficiency
Both machines run with Valmet’s forming fabrics, press felts, shoe press belts and dryer fabrics. Ma Hanbing, Assistant General Manager of PM 52 and PM 53, says: “The new lines are fully equipped with Valmet's fabrics, which perform very well and helped us achieve the guaranteed production rate quickly after start-up. We value Valmet’s continuous research and development, technology and quick response to our needs, and continue to use Valmet’s fabrics and services also in the future.”
The extensive automation offering includes Valmet DNA Distributed Control System (DCS) with built-in condition and runnability monitoring, Valmet IQ Quality Control System (QCS), Web Monitoring System (WMS), Moisturizer, Dilution and Steam profilers. Wei Xiangui, Automation Manager of PM 52 and PM 53, says: “Valmet DNA’s unified data management platform can greatly reduce the workload intensity of operators. It provides efficient and fast analysis for root cause based on historical data, which is a great help to operation and maintenance people. At the same time, it solves our problem of a lack of professional and experienced operators as it requires less engineers to use the system.” Xue Jiujiang, Deputy Manager of Guangdong Shanying Instruments adds: “Since the start-up, two incidents have been detected through Valmet DNA condition monitoring system and accurate diagnosis has been made. It avoided unplanned downtime and the loss of the production line. The operational efficiency has improved.”