Valmet Recovery Boiler

Valmet Recovery Boiler is the optimized recovery boiler for chemical pulp mills. Utilizing our proven solutions and the latest innovations, it represents the highest evolution of recovery boilers. With selection of modular solutions the recovery boiler can be tailored to your requirements.
Increased profitability - Valmet Recovery Boiler is the most cost-effective recovery boiler to operate.
Peace of mind - A complete solution ensures all the technical details work seamlessly together.
Safe and environmentally efficient operation - Helping you to meet regulations also in the future.
Technology with uncompromized performance
We offer guaranteed availability with maintenance interval even up to 18 months. This is enabled by robust design and superior material choices.
We can support you to reach optimized production with leading automation solutions including advanced process controls and leading IoT solutions.
Our technology enables high chemical recovery and energy efficiency, decreasing both operating costs and environmental impact. We can also optimize the boiler for high power production.
We have developed solutions to secure easy and safe operation, lowering the risk of quality errors and human errors.
Comprehensive solution from the technology leader
We can offer complete solution for chemical pulp mills including process technology, automation and services. Working with every island of the pulp and paper mills, we know the challenges of the pulp and paper production and can support in finding the optimal set-up for every island.
As a modular solution, our recovery boiler can be tailored and optimized for your needs regarding e.g. flexibility, power production, environmental performance, NCG handling, automation and process optimization.
Our patented innovations bring benefit your business.
Our team of experts at your service
We have a unique experience and understanding of the industry with over 300 recovery boilers delivered worldwide and knowhow of all pulp mill islands. Our team of experts work together to offer you the right solution.
Our global and local network of service professionals is ready to back up your operation 24/7. Leading industrial internet services complement the onsite support we offer.
Continuous development is secured with our own R&D and cooperation with leading universities and technology institutions in the field.
Main technical features
The air system is central to good recovery boiler performance. Valmet’s Multilevel Air System features staged, interlaced air distribution that efficiently reduces NOx emissions and makes it possible to meet the most stringent emission limits.
Valmet offers mill-wide systems to collect and combust odorous gases. These systems are often integrated with the Multilevel Air System.
A unique feature in the recovery boiler is a rigid cross-furnace screen at the nose arch. It protects the superheater from furnace heat radiation and thus reduces corrosion.
Operator safety and ergonomics play key roles in Valmet’s boiler design, and our boilers feature many solutions that focus on them. Some examples are our systems for automatic cleaning of air ports and smelt spouts, retractable liquor gun systems and safety shields at smelt spouts.
Related pages
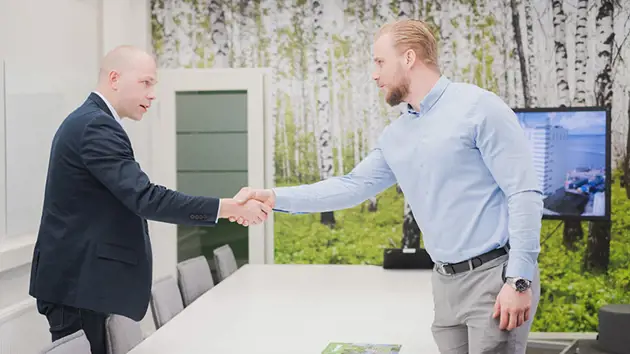
Our expertise is at your service
Our focus is to bring your performance forward and ensure that you get the most from your recovery boiler. Our technical expertise, covering both new installations and upgrades, is based on our experience from more than 200 successful recovery boiler projects. If you want to know more, contact us to get in touch with our recovery boiler specialists.
Contact us