Automated Boiler Cleaning Technology
Valmet Shock Pulse Generator
The Shock Pulse Generator (SPG), is online boiler cleaning equipment that automatically generates Shock Pulses (SP) through the use of pressurized gas combustion. This innovative alternative to Steam Sootblowers has proven its outstanding performance worldwide with more than 1,200 different installations in 20+ countries.
Solve tough challenges
The Valmet Shock Pulse Generator (SPG) is a uniquely tailored solution for tough boiler cleaning applications. Through the use of combustion-generated pulses, the unit efficiently removes ash and slag build-up across a broad range of boiler applications.
Safe operation
Safe cleaning operation with no collateral damage to boiler tubes.
Space savings
When compared to sootblowers, the SPG has a much smaller footprint. This is particularly helpful in areas that plug up frequently, but adding an additional sootblower isn’t an option because of a lack of space.
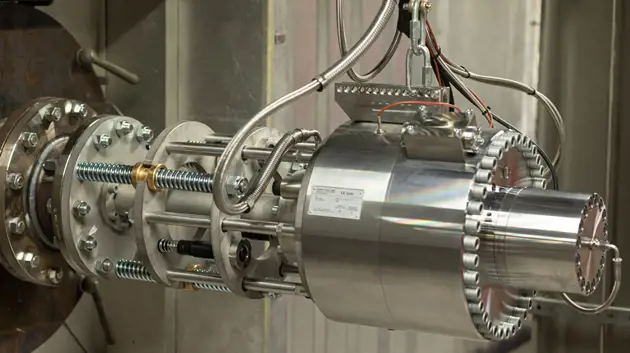
What is a Shock Pulse Generator?
Developed in 2009, the Shock Pulse Generator (SPG) is an on-line boiler-cleaning device that generates automatic, directed shock pulses/waves. The shock waves are created through the controlled combustion of a mixture of burnable gas (Natural Gas or Methane) and air. Contrary to manual processes, the combustion is carried out automatically and outside of the boiler, in a pressure-resistant device. The resulting supersonic shock wave is introduced into the boiler by means of a valve and a discharge nozzle. The combustion gas, the boiler tubes, and walls are put into a short oscillation, so that deposits, i.e. slag and fly ash, are cleaned off.
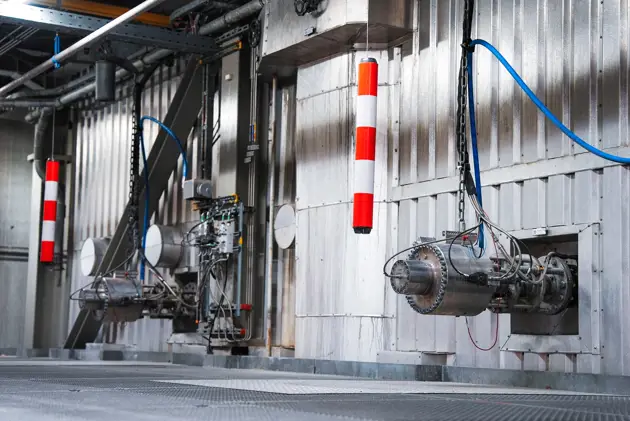
SPG Quick Facts Guide
The SPG is a compact yet robust online boiler cleaning system that utilizes automated shock pulses to clean slag, ash, and buildup. Want a quick overview of the equipment and how it works?
Show me the guide!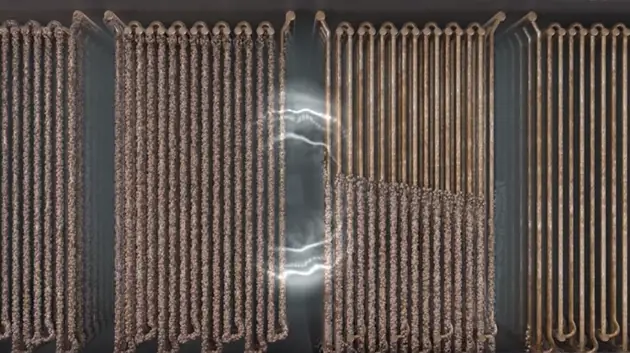
Automated combustion of gas and air generates Shock Pulses for cleaning deposits
Function and cleaning effect
The SPG is mounted to the outside of the boiler wall with a discharge nozzle being introduced into the boiler by means of a boiler nozzle or manhole. SPG's are manufactured from special high-pressure, high-temperature stainless steel and are available in two different models, SPGr10 and SPGr16.
The following steps are performed during one cycle:
- Filling of the combustion chamber with methane / natural gas and air
- Mixing of gases in the combustion chamber
- Ignition by glow plug
- Opening the piston, releasing the discharge valve
- Injection of shock pulse into the boiler
- Short shock pulse cleans heating surfaces, removing slag and fly ash
- Cleaning without damage to boiler tubes
Benefits
- Permanent and automated boiler cleaning
- Lower exhaust temperature and higher boiler efficiency
- Improved CO2 plant performance
- No thermal abrasion or damage to the boiler tubes
- Reduced cleaning needs during maintenance stops
- High degree of operational safety – boiler remains closed during operation
- Reduced space requirements
- High industrial standard (CE-certification based on Pressure Equipment Directive, clearly defined ATEX zones, PLC system monitoring, PROFIBUS/MODBUS compatible)
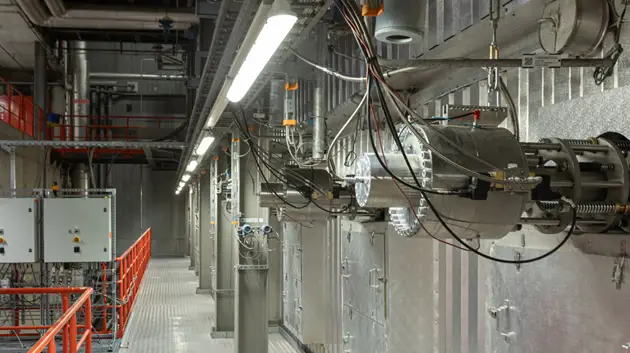
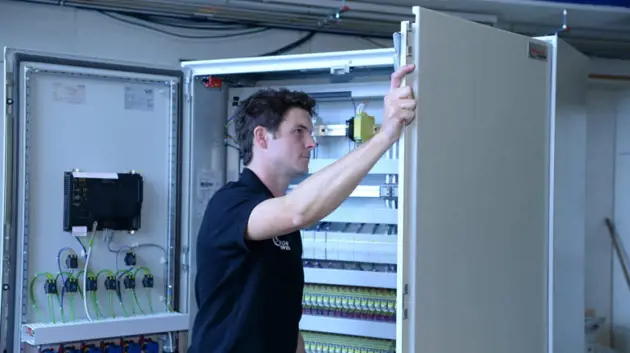
Industries
The online boiler cleaning equipment removes slag and ash and can be used to replace or enhance sootblowers, shot ball systems, water canons, rapping systems, sonic horns, and shower cleaning systems (SCS).
Applications include:
- Waste to energy plants
- Industrial boilers (biomass / various fuels)
- Sludge incineration plants
- Hazardous waste incineration plants
- Replace or enhance soot blowers
- Coal-fired power plants
- Black liquor recovery boilers
- Filters and spray absorbers
- Cements kilns, Zinc factories
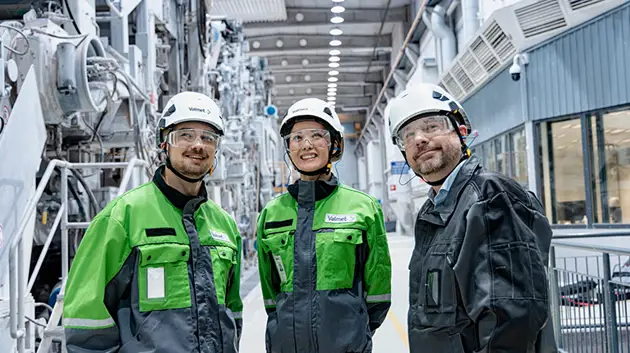
Innovative boiler cleaning technology
Looking to learn more about a space-saving boiler cleaning solution with no thermal abrasion to the boiler tubes?
Contact us