Sulfuric acid plant

Integrated Sulfuric Acid Plant provides savings and improved environmental performance. With this solution, sulfur in pulp mill’s odorous gases can be converted into sulfuric acid. Internally produced acid closes the mill’s Na-S chemical balance. Sodium and Sulfur are essential chemical elements at a kraft pulp mill, and they play a vital role in the quality pulp production. Balancing these chemicals directly attributes to the efficiency of the pulp mill. Reduced sulfur in pulp mill odorous gases can be converted to sulfuric acid and this internally produced acid closes the chemical circulation and brings economic and environmental gains.
Improved environmental performance - with minimized sodium sulfate ash dumping
Enhanced Na-S balance
Savings in NaOH consumption
Sulfuric acid plant - production process
Concentrated non-condensable gases (CNCG) are collected and lead to a collection tank, from which they are taken to a separate incinerator. In the separate incinerator, total reduced sulfur compounds in the CNCG are oxidized into SO2. The flue gas from the boiler is led to a catalytic reaction vessel. The catalyst oxidizes SO2 by using excess oxygen supplied through combustion air into SO3. Flue gases from the catalytic converter are passed into a condensing tower. The temperature of the flue gases is reduced with the cooling liquid and the SO3 in the flue gases reacts with H2O to produce sulfuric acid.
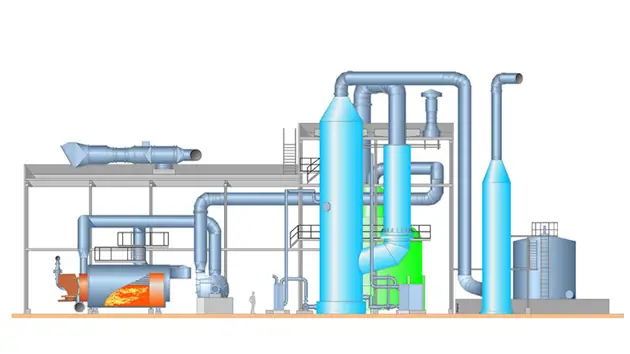
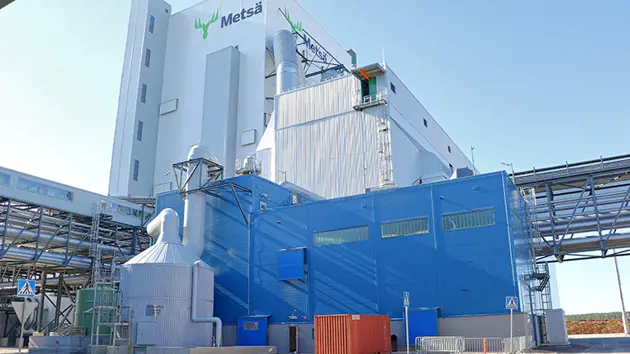
First installation in successful operation
The first sulfuric acid plant of this type was started up in 2017 and has been continuously operating at Äänekoski Metsä Bioproduct mill, Finland. The plant was ready on-time and has been able to produce sulfuric acid of excellent quality surpassing all the criteria set for externally sourced sulfuric acid. This integrated sulfuric acid plant is a true win-win-win solution. This is an environmental investment with a tangible financial payback in chemical savings.
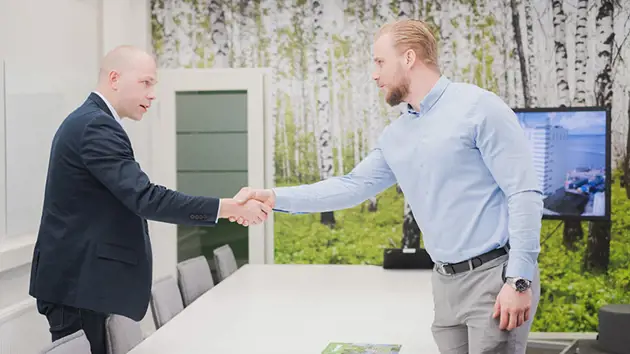
Our expertise is at your service
Our focus is to bring your performance forward and ensure sustainable pulp production. We have a dedicated technology team working on NCG and Sulfuric Acid Plant solutions. If you want to know more, contact us to get in touch with our experts.
Contact us