Creating a valuable product from hazardous side streams
Producing sulfuric acid from a pulp mill’s non-condensable gases (NCG) is a true win-win-win solution. An innovation developed by Valmet improves the chemical balance of mills, generates cost savings, and reduces environmental impact.
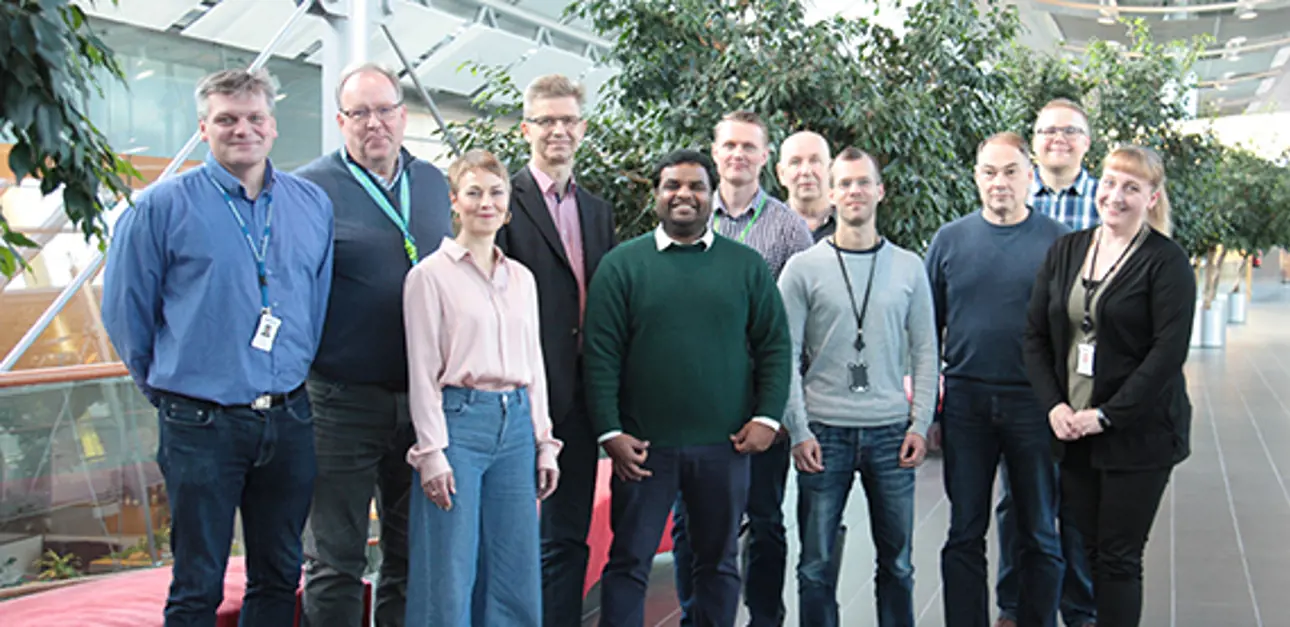
Creating something new is always interesting and exciting, especially when it is done with a clear goal and tight time schedule. This was the kind of challenge that Metsä Group gave Valmet’s team as part of the Äänekoski bioproduct mill project. The emission limits based on best available techniques set very low limits on emissions into the air and water from the mill. Therefore it was essential to find a new solution for reducing the chemical losses and consequently emissions from the production process. In line with the bioproduct mill thinking, the goal was to produce valuable sulfuric acid internally from mill’s own side streams.
Concentrated non-condensable gases are collected and led to a collection tank, from which they are taken to a separate incinerator. In the incinerator, the total reduced sulfur compounds in the CNCG are oxidized into SO2. The flue gas from the boiler is led to a catalytic reaction vessel. The catalyst oxidizes SO2 by using excess oxygen supplied through combustion air into SO3. Flue gases from the catalytic converter are passed into a condensing tower. The temperature of the flue gases is reduced with the cooling liquid, and the SO3 in the flue gases reacts with H2O to produce sulfuric acid.
Finding the right solution
Sodium and sulfur are essential chemicals in kraft pulping, and they play a vital role in the quality of the pulp production. Balancing these chemicals directly contributes to the efficiency of the pulp mill. The side stream processes – like production of tall oil or lignin – increase the demand of sulfur intake into the production process.
“If there is a surplus of sulfur in the process and the process losses are very small, you need to find a way to balance the incoming and outgoing sulfur. Conventionally, this balance is achieved by removing sulfur from the process with recovery boiler ash. However, removed ash also contains sodium and this loss needs to be replaced by external supply of valuable caustic soda,” explains Tero Juutilainen, the Product Manager for Valmet’s Sulfuric Acid Plant.
Production of sulfuric acid itself is a well-known process. But developing an integrated solution to produce sulfuric acid at a mill site from the mill’s own process streams was not that clear cut. The work started by identifying the source of the sulfur, which was selected to be concentrated, non-condensable gases (CNCG). The sulfuric acid plant consists of a CNCG incinerator, catalytic converter, condensing tower, and bisulfite scrubber, including product storage tanks.
“The biggest challenge in this kind of sulfuric acid production is the end concentration of the acid – 50 to 70 percent – which is the most aggressive concentration. To manage the corrosion, we needed to carefully design the temperatures and materials in the process,” explains Antti Väljä, Project Manager from Valmet.
Antti Väljä, Asta Humalajoki and Tero Juutilainen from Valmet's NCG Solutions team.
Win-win-win results
The project was a success. The plant was ready on time and has been able to produce sulfuric acid of excellent quality, surpassing all the criteria for externally sourced sulfuric acid.
“To succeed, we needed to have the right team in place, combining both technical knowledge and a strong drive to deliver results – not to mention a small hint of daredevil. This development project was an excellent example of cooperation between Valmet and customer teams,” explains Asta Humalajoki, Product Sales Chief Engineer from Valmet’s Mill-Wide NCG Solutions team.
“This kind of integrated sulfuric acid plant is a true win-win-win solution for managing the chemical balance. This is an environmental investment with a tangible financial payback in chemical savings,” Juutilainen continues.
Having its own sulfuric acid plant brings the mill significant environmental advantages. One of them is that the amount of sulfate going to the mill’s effluent treatment plant is reduced and the sulfate load in the nearby waterways decreases drastically.
The produced acid can be used in bleaching, the chlorine dioxide production plant, tall oil production, pH control, and the wastewater treatment plant. The economic savings come first and foremost in the form of smaller need for make-up sodium, while savings in sulfuric acid purchases have only a secondary impact. The average overall saving is about EUR 5 per tonne of pulp produced. In addition, reduced dumping of ash leads to further economic and environmental benefits.
Related articles