Press felts for board and paper machines
Excellent runnability and planned lifetime
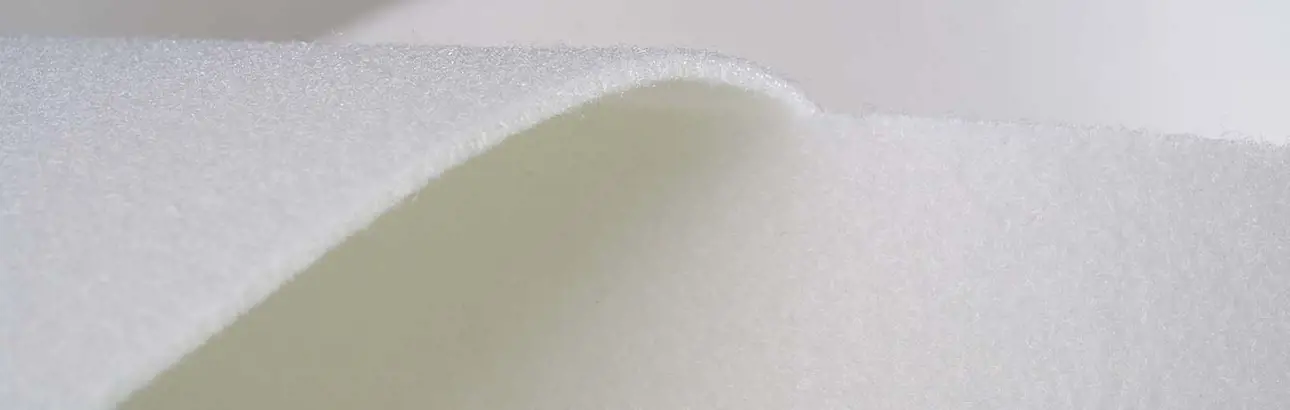
Valmet's press felts are always tailor-made to the specifications of each individual board and paper machine and position: paper grade, furnish, speed, dimensions. The proven world class press felt manufacturing technology ensures that our press felts respond to the highest customer expectations. High quality Valmet Press Felts deliver results in terms of lifetime, energy savings, sheet dryness and reliability.
Excellent runnability
Fast start-up
High sheet dry content
Marking-free
Valmet Press Felt EMX M Bioneer
This design is especially targeted for board machines. The felt features long lifetime and stable running. The felt has enough water handling capacity to avoid crushing and high CMD stability to avoid wrinkles and folding. The felt structure is optimal against marking.
- Excellent sheet quality for the targeted grade
- Balanced dewatering in the nip and the Uhle boxes
- Felt openness and void volume is optimized for needed paper grades
- Part of the raw material is replaced with a bio-based alternative
This felt style is used in both center press and linear press concepts in all positions.
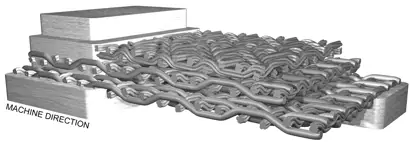
Valmet Press Felt EMX
This felt has a relatively open and compressible structure that results in less sheet breaks and more production. It has good compaction resistance and batt fiber anchorage, resulting in longer running times. A strong and flexible laminated base gives an excellent dewatering capacity in various positions for all paper grades. Smooth surface ensures good properties for the targeted grade
- Fast start-up
- Efficient nip dewatering
- Long and stable service life
- Less runnability problems
- Good sheet quality
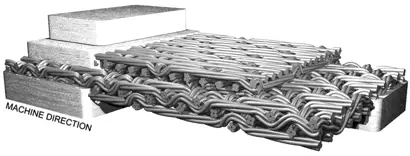
Valmet Press Felt TSM
The safe, easy and quick installation of Valmet Press Felt TSM, a seamed felt, decreases the need of manpower and crane time. It is applicable for all board and paper grades and felt positions. It has a double or triple layer structure with monofilament yarns and the void volume and openess are adjustable.
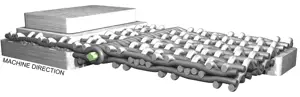
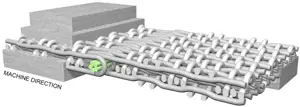
Valmet Press Felt TMO/SMO
The TMO/SMO treatment upgrades the felt's performance properties such as runnability, lifetime, smoothness and dewatering stability over the whole lifetime. This unique technology can be applied to all Valmet Press Felt designs.
- Faster start-up
- High and constant dewatering capacity
- Improved paper profiles
- Break free running
- Increased lifetime
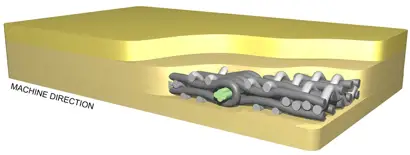
Other Valmet Press Felts
Valmet Press Felt LMR
Durable laminated modular structure for board machines to achieve reliable dewatering and long lifetime.
Valmet Press Felt SPM
Special woven structure for high nip dewatering and immediate starts up for printing and writing machines and high-speed board machines.
Valmet Press Felt TSR
Traditional single base felts that offer a large range of possibilities with highly adjustable designs to cover almost all positions specially for printing and writing grades.
Valmet Press Felt AQ
Non-woven structure for high nip dewatering and immediate starts up for printing and writing machines.
Valmet Press Felt STM
Hybrid non-woven and woven structures for high nip dewatering and targeted lifetime for printing and writing machines.
Need support with your press felts?
Our press felt professionals are here for you. Just send us your question and we'll revert soonest.
Contact usRelated articles and news
