Drum pulping
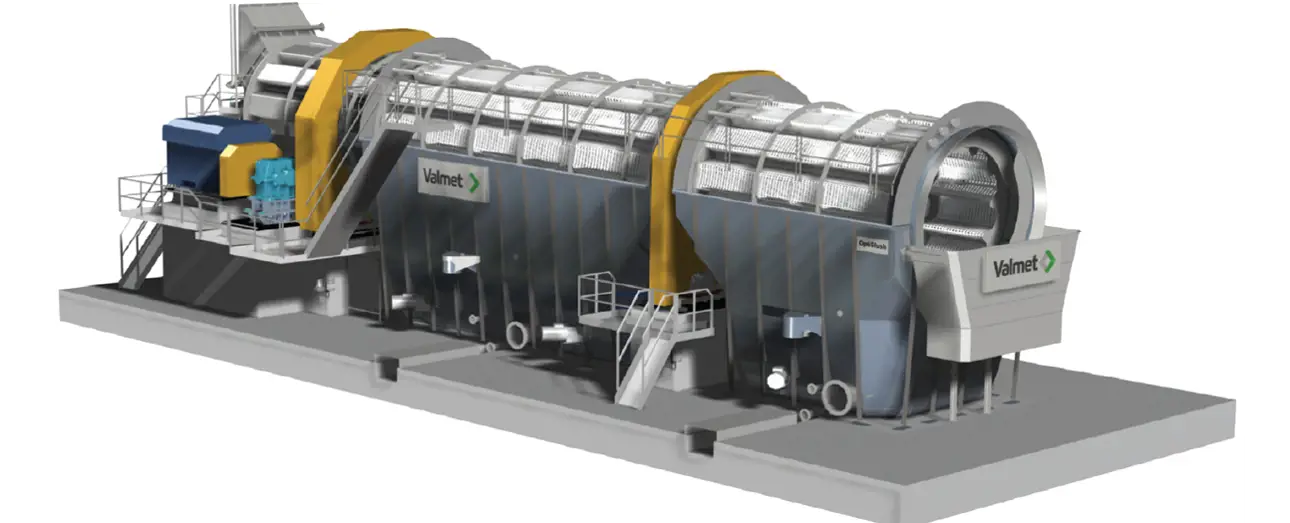
Smart and compact design
Raw material flexibility
Low operating costs
Designed as an energy-efficient solution to help board and papermakers produce high quality end products from recycled fiber, Valmet Drum Pulper is revolutionizing the pulping process. Valmet Drum Pulper technology features a three-stage process for faster raw material processing with maximum efficiency.
Key benefits of Valmet Drum Pulper include:
- A shorter, lighter design that requires less space and up to 20% less weight than conventional drum pulpers
- Reduced energy consumption
- Integrated shredding, screening, and slushing helps reduce the need for additional energy-consuming parts
- Increased pre-slushing efficiency from the use of innovative knife lifters
Click here to view the Valmet Drum Pulper Data Sheet.
Did you know...
that the Valmet Drum Pulper requires 15-30% less specific pulping energy than a vat pulper or conventional drum pulper?
Learn moreSmarter design
Valmet Drum Pulper produces two fractions to enable screening while slushing. Separation of fractions into a fine fraction (with small-sized holes) and a course fraction (with large-sized holes) provides more slushing time for harder-to-slush materials such as lower-grade OCC, while removing easier-to-slush fibers as soon as possible.
Valmet Drum pulper’s high consistency treatment enables efficient fiberizing and ink detachment even from very contaminated furnish. The gentle slushing action of a drum pulper does not break up impurities, making them easier to remove in the subsequent process stages. Continuous operation stabilizes and improves the efficiency of the entire process, ensuring consistent pulp quality.
The key slushing factors, time and impact energy, are tuned by adjusting the roll angle and speed to create the optimal vertical and horizontal flows inside the pulper. This makes it possible to optimize the treatment of different raw materials for various end-use requirements. The screen section is equipped with multiple dilution spray piping that also broadens the pulper’s operating range.