OptiFlo Layering Fourdrinier headbox
Two- or Three-Layer headbox for lightweight containerboards
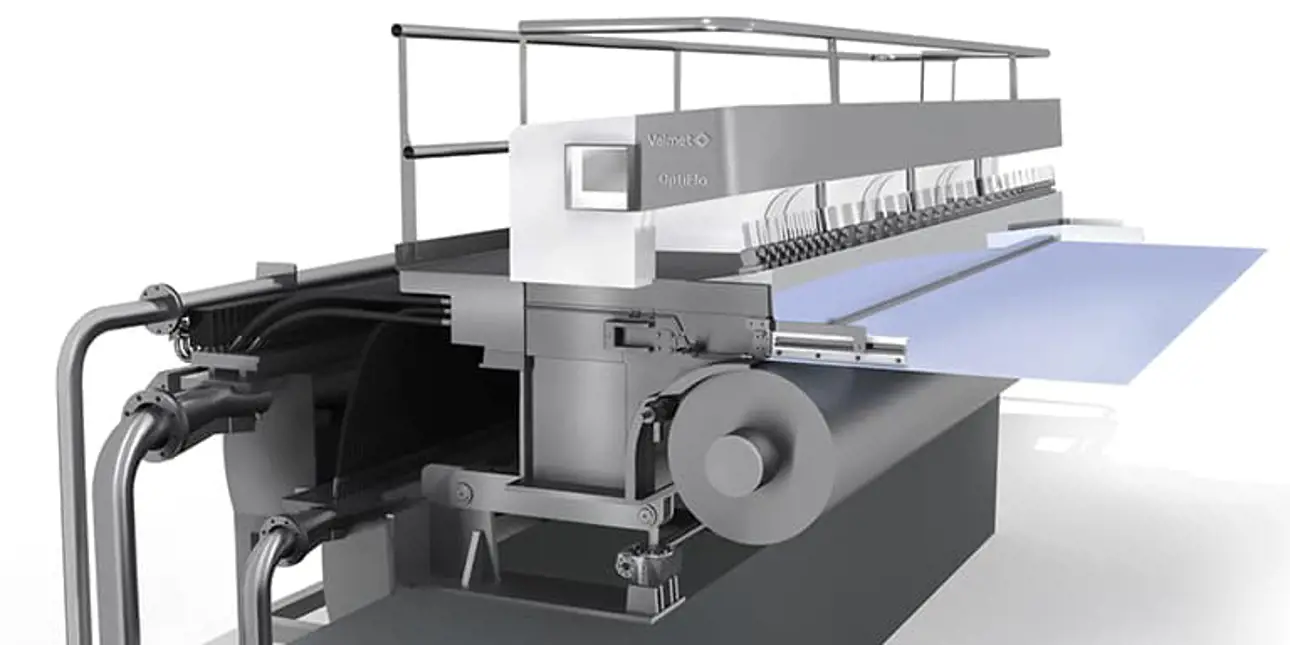
The new OptiFlo headbox family brings together our unrivaled expertise and new technology, opening the door to improved quality and increased productivity in all forming applications. Valmet's cost-effective two- or three-layer headbox makes it possible to produce lightweight containerboard with only one hybrid forming unit or with Fourdrinier type former.
Cost efficient layering concept
Excellent layer coverage
Aqua layering technology
Cost efficient layering headbox concept
OptiFlo Layering Fourdrinier tackles the board makers’ challenges in combining lower basis weights, faster speeds and higher ash contents resulting from the increased use of recycled fiber. OptiFlo Layering headbox enables feeding different stock into each layer, which in turn means that the structure of board can be further optimized.
Having two or three separate headboxes is a much bigger investment compared to a layering headbox. But the cost savings do not come only from the initial headbox investment. There are possibilities for great operational cost savings as well. With two or three headboxes you have wires running with all of them consuming water and chemicals. These require cleaning and changing wires, which take a lot of time. All of these create a higher operational cost compared to a layering headbox. So, it is not only about the initial headbox investment, but consider also the cost savings in energy, chemicals and consumables.
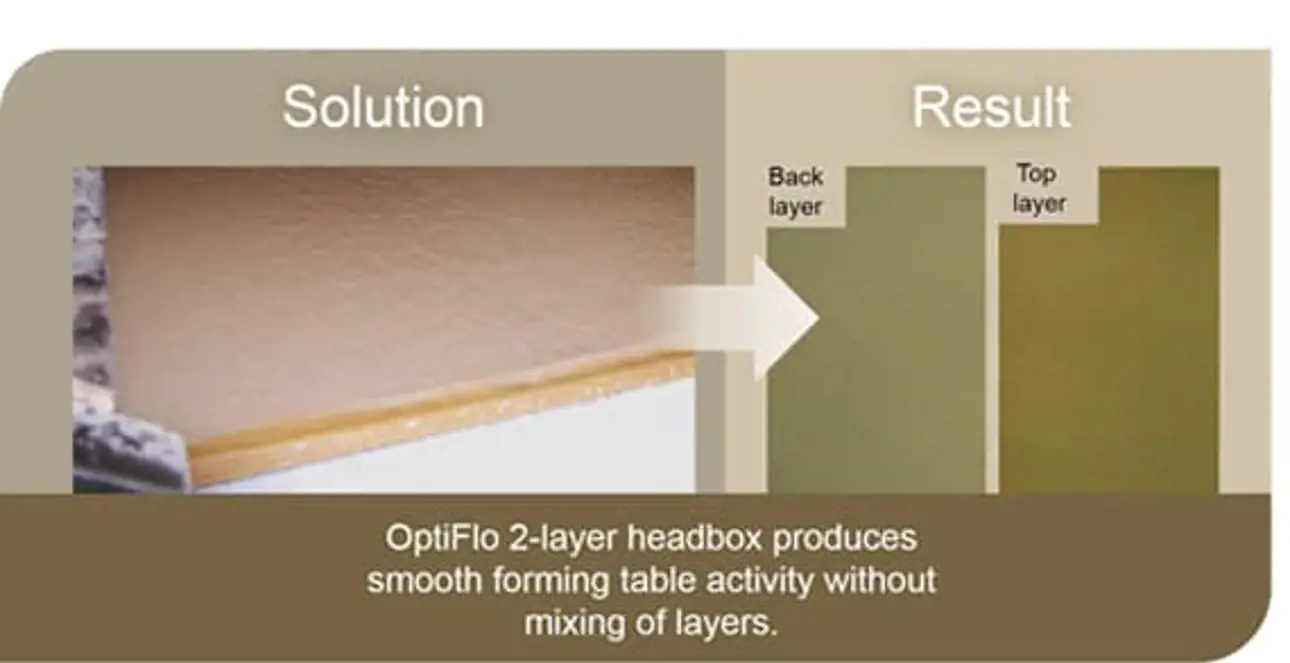
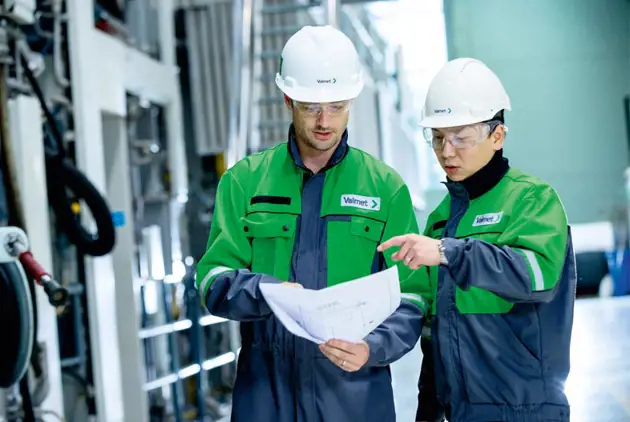
Want to talk to our headbox experts?
If you wish to get further information like technical specifications, need a quotation, or wish to discuss different solutions, fill in the contact form and our experts will contact you shortly.
Contact our expertsExcellent layer coverage
In two-layer and three-layer headbox applications, it is very important to guarantee layer coverage. All hydraulic components of the OptiFlo Layering Fourdinier headbox have been designed to minimize slice jet and board sheet disturbances. This novel solution provides excellent layer coverage, considerably lower residual variation in basis weight as well as an excellent formation with no streaks or tiger stripes. The OptiFlo Layering headbox hydraulics’ design produces smooth forming board activity, without any mixing of individual layers.
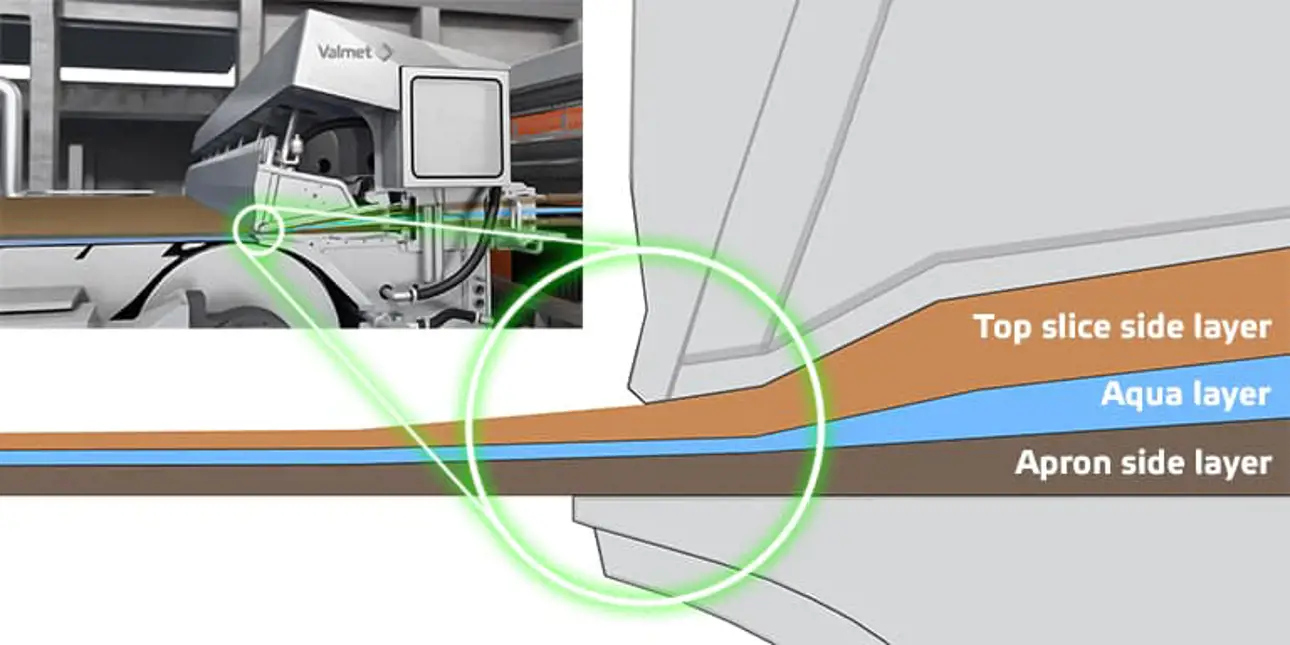
Aqua layering technology
Valmet's latest innovation, aqua layering technology uses a thin water layer as a headbox wedge to stabilize layers and to form an even film while layers of stratified paper are being joined together.
It prevents the mixing of stock layers and also enables the feeding of functional additives between the stock layers. Read more about the benefits of aqua layering here.
Valmet’s unique three-layer headbox was at the heart of Sappi Maastricht’s rebuild where the aim was to improve board properties and quality. The old headbox was replaced with completely new type of headbox, supplying three simultaneous layers of stock, leaving forming and the press section unchanged. “Having three separate headboxes would have been a much bigger investment – ten times what we needed for this machine,” says de Koning. There are other benefits, too. Not all the grades produced in Maastricht (graphical, SBS, FBB) are traditionally layered, but the mill has found it valuable to layer all their grades. They optimize the quality and cost of each layer for each grade.
Watch the video and learn how Sappi Maastricht managed to get into the specialty boards business with a unique three-layer headbox, producing extremely high-quality SBS and FBB with superior smoothness and printability.
How to plan a successful rebuild?
Rebuilding a paper or board machine can improve the competitiveness of your business and your processes. But where do you start? Download our e-book to learn how to develop a winning rebuild concept, how to minimize rebuild related risks, and how to ensure smooth ramp up to full production.
Download e-bookLooking for headbox related services?
We provide a wide range of professional headbox maintenance and testing services to get the best out of your headbox. These services make it possible to eliminate web streakiness and jet inaccuracy, to lower the need for slice opening adjustments, and to improve dry weight profiles.
Go to headbox servicesPlanning a grade conversion?
The world is changing fast; the consumption of newsprint and printing paper is decreasing and the consumption of containerboards or cartonboards are increasing. An old paper machine can be updated with a grade conversion rebuild to produce more profitable products. Turn a new page for your paper machine with the help from Valmet.
Discover moreExplore our latest board and paper press releases
- Jul 8, 2024Valmet to supply operator training simulator to Graphic Packaging International in Waco, Texas, United States
- Jul 8, 2024Discover Valmet MTC Wizard at Tissue Innovation Days 2024: the latest technology enhances Client benefits in Tissue Folding
- Jul 2, 2024Valmet to supply a high-capacity winder to Wuzhou Special Paper in China
- Jun 26, 2024Valmet to supply both a papermaking line and a paper machine rebuild to a customer in Asia-Pacific
- Jun 25, 2024Valmet to deliver a tissue machine to Andhra Paper in India
- Jun 19, 2024Valmet receives the second order of converting lines to Metsä Tissue in Mariestad, Sweden
- Jun 13, 2024Valmet and Flootech enter partnership to advance water treatment for the board, paper and tissue industry
- May 30, 2024Valmet enters joint venture with Körber to advance the digital offering to the tissue industry
- Jan 11, 2024Valmet to supply key technology for Shandong Jin Tian He Paper’s board machine in China
- Oct 25, 2023Valmet has received a major order of multiple technologies from Liansheng Pulp & Paper in China