Energy efficiency and high quality for fourdrinier machines
OptiFlo Fourdrinier headbox

The OptiFlo headbox family introduces a new level of performance with a modular construction developed to meet the growing productivity and quality requirements of high-quality board and paper machines. The OptiFlo Fourdrinier headbox is a mix of proven technology and new ideas.
Excellent end-product quality
Higher productivity
Lower life cycle costs
A secure investment
Better quality with dilution system and edge feed control in fourdrinier headbox
The secret behind the 30% better CD profiling accuracy is OptiFlo’s ejector type dilution system and patented CD dilution profiling with edge feed control. Unlike traditional designs, profiling water is delivered to every primary tube. Effective and zone-controlled mixing of dilution water and pulp flow provides narrow and accurate dilution response. The redesigned hydraulics using accelerating secondary tubes provide better turbulence and flock breaking power and deliver a more uniform and stable headbox jet to the wire.
The raw material quality potential is maximized and good formation without streaks or stripes enhances end product properties for perfect visual appearance. Designed to produce perfect visual appearance with good profiles across the entire machine, the OptiFlo headbox delivers improved paper quality.
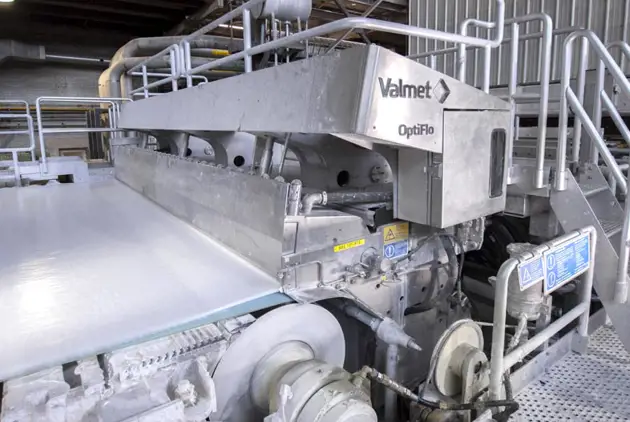
Want to talk to our headbox experts?
If you wish to get further information like technical specifications, need a quotation, or wish to discuss different solutions, fill in the contact form and our experts will contact you shortly.
Contact our expertsHigher productivity with increased machine speed and better runnability
Making more with less is the byword for today’s competitive production environment and OptiFlo introduces a new level of performance for high-quality board and paper machines. Increased machine speeds and better runnability are made possible by the excellent web uniformity achieved by the OptiFlo headbox.
Quicker tuning at grade change, more uniform web edges providing a wider trim, further maximize production capacity potential. Unplanned downtime is minimized with the easy operation and good cleanliness of the headbox, allowing extended operation times while excellent component accessibility makes maintenance easier and shutdowns shorter.
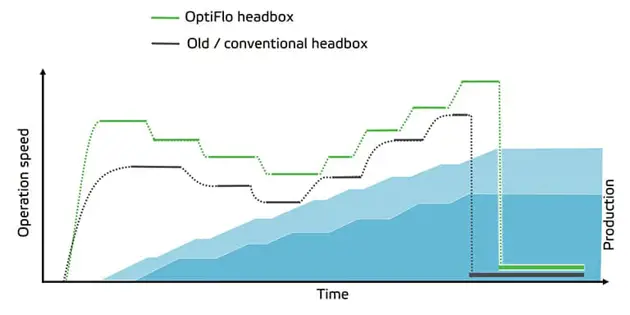
Headbox production boost with OptiFlo headbox - operate faster, operate longer and operate wider
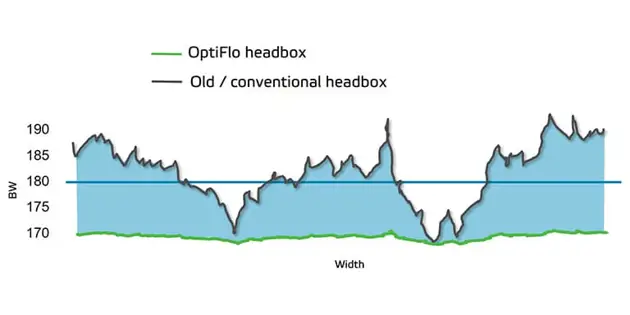
OptiFlo Fourdrinier headbox – example for containerboard: Better raw material economy of flat profiles
Lower fourdinier headbox life cycle costs
Considerable energy savings are gained with OptiFlo’s ejector dilution systems, more efficient tube design and reduced internal pressure losses. Recirculation is minimized (5 %) and overflow pumping eliminated.
The result is a 50 % reduction in energy consumed by internal headbox losses. Lower operating costs are also achieved with OptiFlo’s simplified maintenance requirements and exceptional component accessibility to make service easier and shutdowns shorter.
A secure investment with upgrade possibilities
The advanced design of OptiFlo makes later upgrades possible to handle changing production needs or new control technology with the minimum disruption in production.
The headbox ensures optimum utilization even though production or quality targets may change later. With OptiFlo, you can reach targeted improvements in productivity and quality right after start-up.
Are you looking for headbox sheets and wedges?
Headbox sheets used in the headbox are vital for producing a uniform jet flow from the headbox slice to the forming section.
Learn more about headbox sheetsHave a closer look at the main features of OptiFlo Fourdrinier Headbox
The innovative design of Valmet’s OptiFlo headbox provides the greatest floc breaking ability and flattest profiles available on the market. That ensures that the paper and board products you make is of optimal quality. All the features of the headbox have been carefully designed to increase machine productivity, while keeping daily operating costs in control.
Have a closer look at a few of these main features, like the attenuator, optimized headbox header shape and design, edge feed, ring feed dilution system, and redesigned hydraulics with accelerating secondary on the video: Valmet OptiFlo Fourdrinier Headbox - Transforming machine performance.
Headbox rebuild for Ahlström Munksjö Dettingen PM34
"Just plug and play, start the systems, and get extraordinary good quality out of the PM34." , said Thomas Gehring, Mill manager at Ahlstrom-Munksjö Dettingen Mill after successfull wet end rebuild of their PM34.
The customers of Ahlström Munksjö’s Dettingen mill in Germany set high expectations of the quality and printability of decor paper used in furniture. The mill’s recent wet end rebuild has further improved paper strength, as well as decreased the grammage deviation, enabling them to deliver the quality their customers expect.
See the video for full reference details.
How to plan a successful headbox rebuild?
Rebuilding a paper or board machine can improve the competitiveness of your business and your processes. But where do you start? Download our e-book to learn how to develop a winning rebuild concept, how to minimize rebuild related risks, and how to ensure smooth ramp up to full production.
Download e-bookLooking for headbox related services?
We provide a wide range of professional headbox maintenance and testing services to get the best out of your headbox. These services make it possible to eliminate web streakiness and jet inaccuracy, to lower the need for slice opening adjustments, and to improve dry weight profiles.
Go to headbox servicesPlanning a grade conversion?
The world is changing fast; the consumption of newsprint and printing paper is decreasing and the consumption of containerboards or cartonboards are increasing. An old paper machine can be updated with a grade conversion rebuild to produce more profitable products. Turn a new page for your paper machine with the help from Valmet.
Discover moreExplore our latest board and paper press releases
- Jun 13, 2025Dr. Jin-Doo Kim awarded with a Medal for Extraordinary Achievement for decades-long work for promoting board and paper technologies
- May 26, 2025Valmet to supply a fifth Advantage tissue production line to Lila Group in Turkey
- May 21, 2025Valmet to supply a major paper machine rebuild to Sylvamo in North America
- Mar 27, 2025Successful start-up of Zhejiang Forest United Paper’s PM 6 production line
- Mar 27, 2025Valmet to supply two winders to Wuzhou Special Paper in China
- Mar 6, 2025Valmet to supply a high-capacity winder to Jingxing Holdings in Malaysia
- Jan 21, 2025Valmet to supply an off-machine coater to a customer in Asia-Pacific
- Nov 12, 2024Valmet to supply a complete papermaking line to one of its major customers in Asia-Pacific
- Oct 21, 2024Valmet’s change negotiations completed in Finland in its Paper business line’s Board and Paper Mills business unit
- Oct 3, 2024Valmet to supply an OptiConcept M board making line to Anhui Linping Circular Development in China