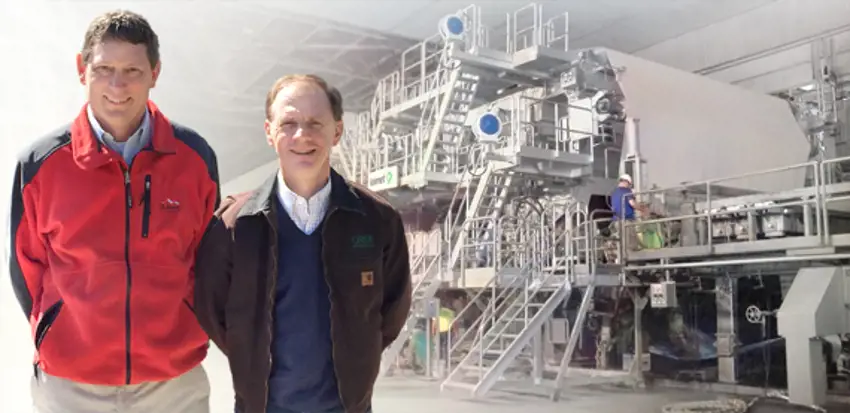
Sep 13, 2017
The Greif Packaging mill in Riverville, Virginia, USA decided to modernize key parts of BM 1, thereby boosting productivity, gaining ground in quality and trimming production costs. As the focal point of a BM 1 corrugating medium machine rebuild, they replaced a 1975-vintage bi-nip press section with a Valmet shoe press section. The on-time and under-budget project, which concluded in June 2015 after a 26 day shutdown, was accomplished with no accidents in over 100,000 man hours.
Summary
Location | The Greif Packaging mill in Riverville, Virginia, USA |
Customer challenge | Need to produce a product competitive in the market place. Press section was a bottleneck, BM1 was drying/speed limited. |
Solution |
1975-vintage bi-nip press section was replaced with a Valmet OptiPress Center shoe press section. BM clothing co-operation with matching Valmet press felts designed to give maximum nip dewatering. |
Results |
Productivity improvement
Energy efficiency
Quality improvement
|
Keywords |
Board and paper, North America, Rebuilds |
Greif Riverville BM1
Grade | Corrugating medium based on hardwood semi-chemical pulp and OCC furnish |
Basis weight range | 23 to 40 lbs (112 to 195 g/m2) |
Wire width | 282 inches (7 160 mm) |
Design speed | 3 000 fpm (914 m/min) |