Reliable low solids measurement in the centrate brings significant savings in Steinhäule
Jul 13, 2018
The wastewater treatment plant in Steinhäule on the Danube river treats around 40 million m3 of wastewater per year. The roughly one million m3 of sewage sludge produced is dewatered to such an extent that it can be thermally utilized in the plant’s two fluidized bed furnaces. Sludge dewatering has been considerably upgraded with the installation of a highly accurate Valmet Low Solids Measurement (Valmet LS).
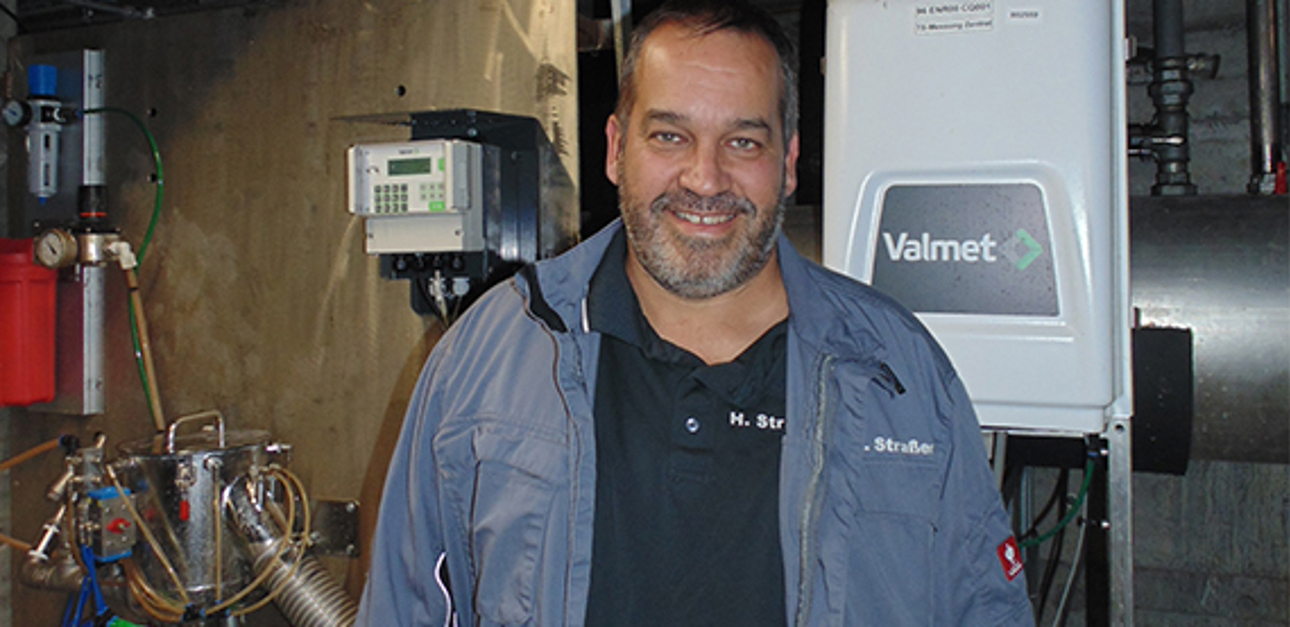
The plant located northeast of Ulm started originally as a mechanical collection treatment plant, which began its operation in 1957 with 242,000 population equivalents. The plant was expanded 25 years later when a biological treatment plant and a plant for the dewatering and incineration of sewage sludge, which contains the solid residues resulting from the mechanical and biological treatment stages, was built. The capacity increased to 330,000 population equivalents in 1980 and just a few years later, Zweckverband Klärwerk Steinhäule (Steinhäule wastewater treatment plant association) was established, which was accompanied by the decommissioning of a number of small wastewater treatment plants. Since then the Zweckverband with currently 12 members is the plant’s sponsor.
By 1993 following various investments, the biological treatment stage had reached a treatment capacity of 440,000 population equivalents and a dry-cleaning system had been installed that removes more than 90% of the phosphorus concentration. In the course of the following 25 years, the mechanical treatment stage was radically modernized. New bar screens, sand and grease trap systems were built. The wastewater treatment plant received a further secondary treatment basin and a high-water pumping station. The denitrification plant and the biological phosphorus removal were modernized. Between 2007 and 2015 the adsorptive treatment stage was built and put into operation.
At present, the plant has 55 staff employed and treats wastewater of roughly 220,000 residents plus wastewater from trade and industry of more 220,000 population equivalents within four treatment stages. Recovered phosphorus has reached the total of approximately 200 tons per year, and screenings account for approximately 462 tons annually. On average more than 80% of the trace substances contained in the wastewater are removed. The incineration of approx. 40,000 tons of in-house produced sludge and 50,000 tons of external sludge with 25% TS is generating more than six million kWh per year.
A reliable option for solid measurement in the centrate has been discussed for a long time. After all, a precise survey of solids content offers the opportunity to
Experiments were carried out using all kinds of different measuring systems - but reliable measurements were never achieved. For example, the formation of gas bubbles proved to be problematic in the optical measurement with a camera. “We were not able to always operate the centrifuges at the best operating point and, as a result, we used too much flocculants, for example”, says plant manager Erwin Schäfer, describing the situation before Valmet LS was installed.
Right image – Erwin Schäfer (left) and Volker Hermann
The measuring unit, the Valmet LS (LS stands for low solids content), offered by the Finnish engineering company at IFAT caught Schäfer’s attention. Ultimately, it provided the possibility to control the dewatering process more accurately through the continuous measurement of the solids content in the centrate.
Following some consultations and meetings, the unit was delivered in autumn 2016, adapted to the wishes of the team of the wastewater treatment plant. However, the unit was initially only rented for a period of six months in order to gain some practical experience. The Valmet LS was mounted on a wall in close proximity to the centrifuge. "The operators had already adjusted their response times. After all, this was a suitable place for automated sampling with enough centrate water available to operate the device continuously”, says Schäfer. The installation was quick and easy and the system is measuring the total amount of free floating solids ever since.
Schäfer also highlights the close cooperation with the supplier: "It was a matter of trust and cooperative collaboration from the very start. It made sense and it was important to involve and coordinate with the employees, especially in view of the fact that various solid matter measurement systems had been tested before, but unfortunately had not delivered any satisfactory results.
Volker Hermann, his colleague, who is in charge of construction, planning and mechanical maintenance of thermal sludge utilization within the plant, also point out the "very positive course of the project". "We have very high requirements for the reproducibility of the samples," he says and explains: “From the very start the equipment worked just like we had envisioned it would work."
(from left to right) Erwin Schäfer, Hans-Juergen Koinegg, and Volker Hermann
Once the unit was running, the centrifuge was operated in all possible areas of work. The results delivered by the Valmet LS were compared with the values from the laboratory measurements and a corresponding calibration was carried out. "Our operators watched very closely and were wondering whether they could trust the values delivered by the new device." But soon their feedback was very positive. “Actually within a few days," according to Herrmann. “In fact, our colleagues here are very skeptical - in a positive sense - and they do question things."
The first impression was good and solidified within the first year after the installation of the Valmet LS. “We think, we saved almost 10,000 Euros in the first year by using less flocculants. We never thought that this acquisition would be so beneficial so soon,” says Schäfer. "In addition, it is important for us to keep pollution as low as possible. 4,000 kilos of flocculants less, or less polymer use, is of course a very positive result in terms of sustainability." Schäfer, who has been working with the company for 24 years, also highlights the spirit of the wastewater treatment plant. "We do not want to be the driven, but pro-actively walk new and innovative ways!"
Volker Herrmann adds to the list of arguments in favor of the equipment by pointing out that this is an online measurement that allows a direct response. The plant is maintained by two employees per shift, which in return reduces the workload of the colleagues. "The ideal state is achieved if with the system’s support the sludge dewatering is reliable and economically mapped in all operating conditions says Schäfer.
Harald Straßer, Master Mechanic in Thermal Sludge Recycling, who works directly with the Valmet LS, is satisfied too. "We were skeptical at first, but after some time in operation things turned very positively!"
Harald Straßer (left) and Stefan Mayr
His colleague Stefan Mayr, Master Electric and Thermal Sludge Recycling, can’t imagine doing it without the equipment. “Only the pipeline would now have to be laid permanently - this here is just a makeshift solution we implemented to start with”, he says.
Also, the purchase of the Valmet DS (Dry Solids) is envisioned. This is a device for measuring sludge with TS contents between 15 and 35%. The Valmet DS is designed to detect the TS content after a centrifuge in order to optimize drying of the dewatered sludge in the subsequent thin-layer dryer.
The Valmet DS is already in use in Finland. Currently tests are carried out in two wastewater treatment plants in Germany and Austria. The Steinhäule plant will be curiously watching how everything will work out in the field. However, Volker Herrmann is already certain: "It would be great, if the Valmet DS repeats the story of the LS!"
Related articles