A superheater upgrade improves waste firing reliability
Feb 21, 2023
A new secondary superheater and wall panels together with Inconel® 625 overlay welding ensure operational reliability, reduce maintenance costs and extend process lifetime at Oulun Energia’s Laanila waste-fired Ekopower plant.
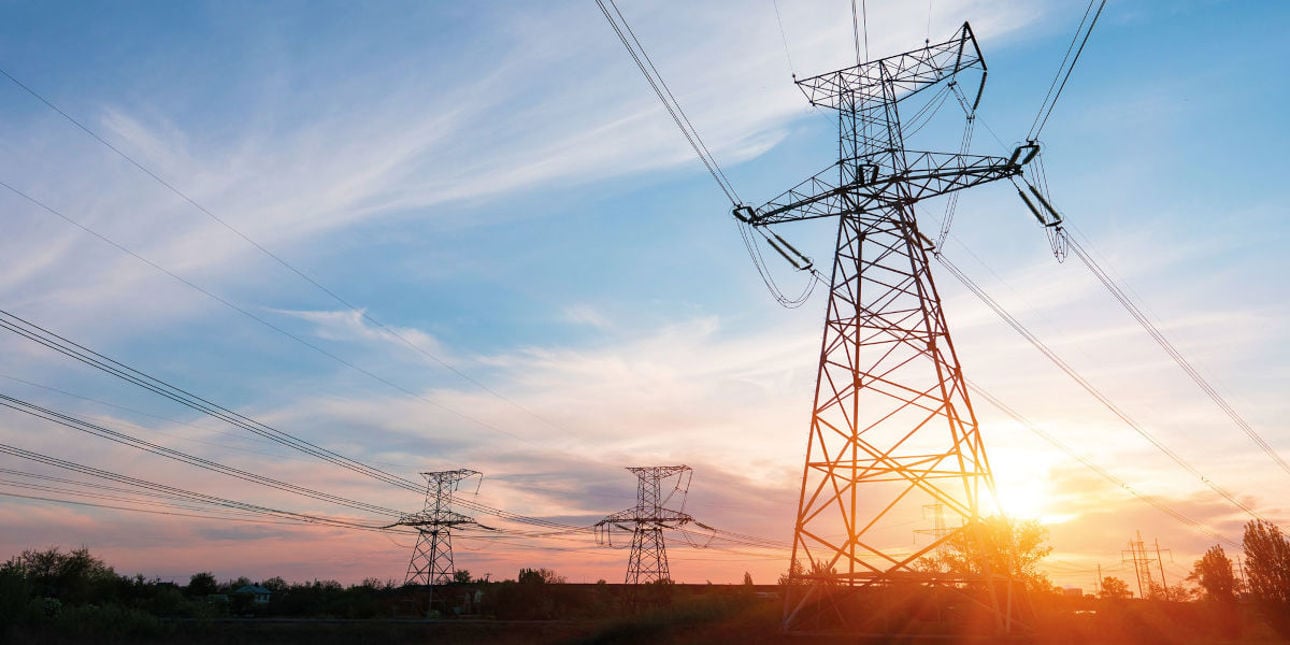
As an active promoter of sustainability, Oulun Energia aims to reach carbon neutrality in its energy production by 2030 at the latest. The company produces power with more than 130 years of experience in the city of Oulu, Finland.
Oulun Energia’s Laanila Ekopower plant processes about 150,000 tons of non-recyclable waste annually into steam and heat. By doing this, it reduces the load on landfills and greenhouse gas emissions into the air. With a fuel capacity of 53 megawatts, the plant is the main supplier of steam to neighboring industrial plants.
“We noticed some thinning in the tube materials of the secondary superheater during our annual maintenance shutdown in the summer of 2021. Dating back to the plant startup in 2012, the device was reaching the end of its lifetime and needed to be replaced before anything drastic happened,” explains Markku Heikkinen, Maintenance Manager, Energy Production, Oulun Energia.
Since any disturbance in steam production would have a vast negative effect on the industrial processes dependent on steam deliveries, it was important to act proactively and ensure high plant availability.
According to Heikkinen, maintenance inspections had also revealed a need to renew some wall panels, as they were thinning, too.
Cooperation goes back a long way
Of the many suppliers, Oulun Energia placed an order with Valmet for the upgrade in February 2022. “In a project of this size, price, of course, is one decisive factor. We go back a long way with Valmet. Due to its strong capabilities in technology and engineering, the company has proven to be a very reliable partner,” Heikkinen points out.
A few years earlier, in 2020, Valmet had delivered a biopower plant to the same industrial park where the Ekopower plant is located. At the core of the former plant is a Valmet CFB Boiler that features circulating fluidized bed technology. With a steam-generating capacity of 194 MWth at 120 bar, 540 °C, it runs on biomass and solid recovered fuel (SRF).
The previous delivery also included a Valmet flue gas cleaning system, a flue gas condenser as well as a plant-wide automation system and Valmet Industrial Internet applications, making it possible to optimize the use of the entire system in real time.
The long cooperation between Oulun Energia and Valmet includes numerous smaller process improvements and service work, too, over the years.
A superheater replacement calls for expertise
The escalated global political situation caused some additional concern, especially regarding material procurement during the Ekopower plant upgrade project in 2022. Luckily, no unpleasant surprises came along.
During the spring maintenance shutdown, Valmet’s local service organization experts checked the existing secondary superheater and its dimensions. No original drawings were available for this third-party component. “There was no plug-and-play solution for us. Valmet provided new drawings with exact dimensions to ensure a smooth installation with minimal modifications,” recalls Heikkinen.
Resistance to corrosion is a must
Oulun Energia is well aware of the corrosion risks that waste firing presents – and wanted to avoid them this time by choosing corrosion-resistant material. Valmet replaced the existing boiler wall panels in the second pass with ones that were overlay welded with an Inconel® 625 corrosion-resistant alloy.
“It is a material that withstands corrosion well. Our target is to lower our maintenance costs in the long run. The Inconel-coated tubes endure harsh conditions twice as long as cast iron tubes do. Depending on the fuel quality, Inconel-coated tubes can last from 10 to 15 years,” says Heikkinen.
|
Oulun Energia’s Laanila Ekopower plant aimed to avoid possible production disturbances caused by a secondary superheater that was reaching the end of its lifetime. Valmet supplied a new superheater and wall panels together with Inconel® 625 overlay welding. Oulun Energia archive / Photographer; Kati Leinonen |
Expectations fulfilled, more benefits to come later
Heikkinen is happy with the installation carried out during the Laanila Ekopower plant shutdown in November 2022. “Although the schedule was tight and every hour counted, the Valmet team was able to get the work done in ten days, as agreed. Like with earlier projects, our cooperation was smooth. We had good and open dialog with each other – from the very beginning of the project up to the first firing. Valmet responded to our needs promptly.”
Most of the work was carried out by Valmet’s local service team, who knew the plant and its staff, a fact that was a big plus, according to Heikkinen. Although this upgrade project is now successfully finished, cooperation with Oulun Energia and its Laanila plant will continue based on a plant-wide service agreement.
At the time when this article was written, only a few months had passed since the upgrade. Heikkinen says that the new installation is running fine, and the project fulfilled the plant’s expectations. “However, the real benefits brought by the investment will only be seen in the long run,” he points out.
As the person responsible for the company’s maintenance, Heikkinen can enjoy a good night’s sleep. He longer needs to worry about the tube wearing out in the secondary superheater or the boiler ceiling or walls. And the neighboring industrial processes will get their steam delivered reliably.
Such a successful outcome is not new to Valmet.
“Today our customers are combusting quite challenging fuels that cause rapid corrosion. Valmet has several references in which existing components have been replaced with overlay-welded and more corrosion-resistant ones,” says Minna Saarelainen, Director, Energy, Recovery, Environmental Services, Finland and Baltics, Valmet. “Even though Oulun Energia’s boiler was not built by Valmet, we were able to provide the right replacement components. Since we have a long history of cooperation with the company, we knew the site and the customer’s expectations – and how to carry out a successful shutdown.”