The cornerstones of safe, successful shutdowns
Apr 24, 2024
Successful shutdowns are an essential part of every mill’s maintenance calendar. They help mills maintain their competitiveness, ensure performance and productivity, prevent failures, and reduce operational costs. However, a lot of work goes into making a shutdown go smoothly and safely. We talked to some of Valmet’s shutdown experts to find out more.
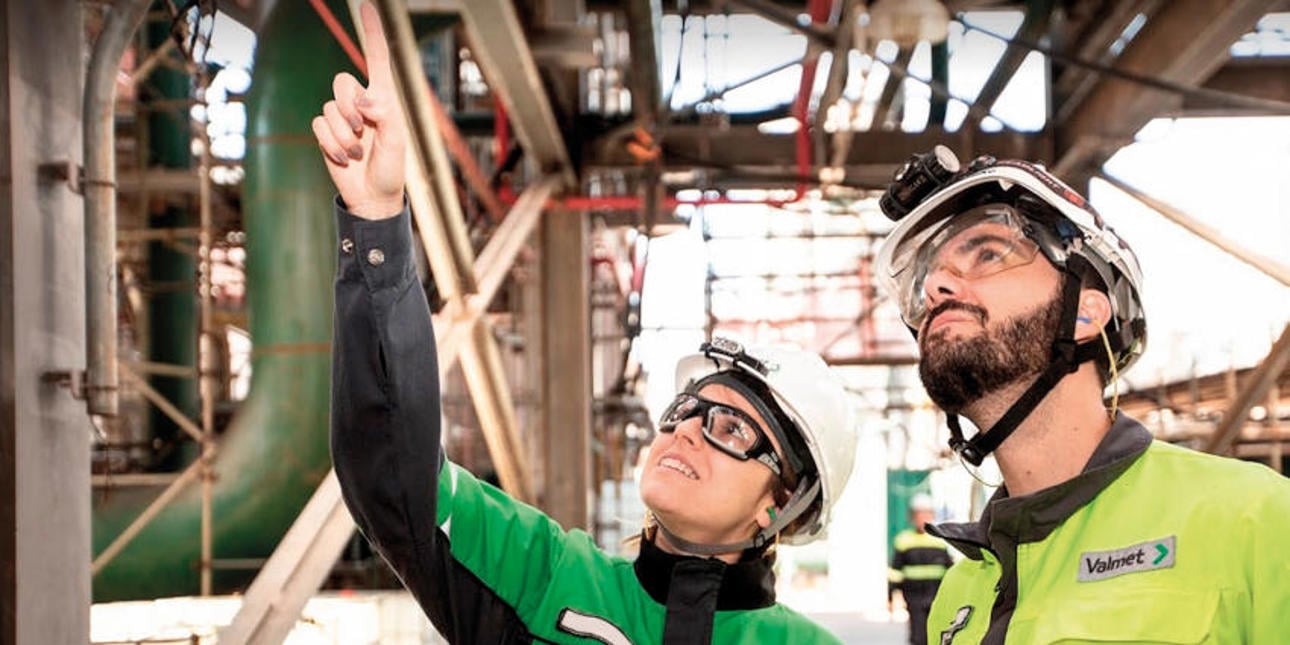
Valmet has comprehensive experience in shutdowns, with over 300 completed shutdowns in pulp and paper mills globally, and we offer a range of shutdown management services for pulp, paper and board producers. With years of experience behind them, our experts always follow the cornerstones of a successful shutdown – planning, expertise, critical analysis, deadlines and safety.
An extensive network of field services professionals
“Our field services professionals are a global team with a high level of technical expertise and experience, and they play a crucial role in Valmet’s shutdown services. We have more than 1,000 field services professionals working at customer mills, and they’re supported by a global network of Valmet experts. We are close to our customers, locally and remotely, every day, working to achieve their targets,” says Fausto Pires, Valmet’s Services Sales Manager in South America.
Thorough planning
Valmet’s main target is to perform each shutdown according to the deadline, with no production losses for the customer or compromises in quality or safety. Managing maintenance shutdowns is a complex challenge due to the many simultaneous activities and people involved. We therefore work closely with the customer, aligning the technical scope, defining the schedule, validating historical mill data, hiring any additional people/resources, performing the maintenance services and providing support until the start-up of the mill. “This approach results in better reliability and a better equipment life cycle,” Pires explains.
Systematic work results in production continuity and a process with excellent operational results.
Customer case: LD Celulose – Full services scope
“Among the hundreds of shutdowns coordinated by Valmet, one of our most recent in South America was for LD Celulose at one of the biggest dissolving pulp mills in the world, in Minas Gerais state, Brazil. Valmet delivered the whole services scope, including maintenance, supervision, inspection and improvements. The project involved a team of more than 500 professionals, and we ensured that the shutdown was a success together,” says Felipe Floriani, Valmet’s Services Director in South America.
The shutdown was the joint effort of Valmet's Automation Systems, Flow Control and Services business lines. “It was a successful operation, and all the activities went according to plan. Our focus on quality, the deadline and safety played a key role in making it a success. The team involved was very important for achieving this result, especially in the planning and other activities before the shutdown. People from Engineering, Supply chain, Logisticis and Assembly were also involved. The coordination and interaction between our business lines also played a major role in delivering easiness, quality and reliability for the customer,” comments the Mill Sales Manager, Felipe Vidal.
Customer case: CMPC – a strong focus on safety
Valmet was also responsible for the maintenance services and supervision of the latest shutdown at the CMPC Guaíba pulp mill in Rio Grande do Sul, in the south of Brazil. This is the biggest mill in the state, and the shutdown involved more than 290 professionals.
The work required the planning, execution, management and development of activities in alignment with the customer’s expectations and needs. Another consideration was that the shutdown coincided with the upgrade and modernization work in the BioCMPC project.
One of Valmet's most recent shutdowns in South America was for LD Celulose at one of the biggest dissolving pulp mills in the world. The scope of delivery included maintenance, supervision, inspection and improvements.
It is noteworthy that Valmet’s General Shutdown package, including maintenance, supervision, smelt extraction and cleaning, upgrades on the DCS, and automation predictive maintenance, again contributed to the successful execution of the shutdown activities. To achieve this, Valmet’s work methodology strictly follows the cornerstones of planning, knowledge, critical analysis (including analysis after the shutdown), deadlines and safety. During this shutdown, five Safety Walks were conducted to check lifting equipment, inspect tools, adapt scaffolding, verify documentation and eliminate unsafe conditions. Furthermore, more than 30 Daily Safety Dialogues were carried out with the participation of the Valmet team.
“With such shutdowns, we can guarantee the integrity of all the equipment in operation, preventing emergency stops, possible problems or damage to structures. This systematic work results in production continuity and a process with excellent operational results,” concludes Floriani.
Text Luiza Callado