Press section
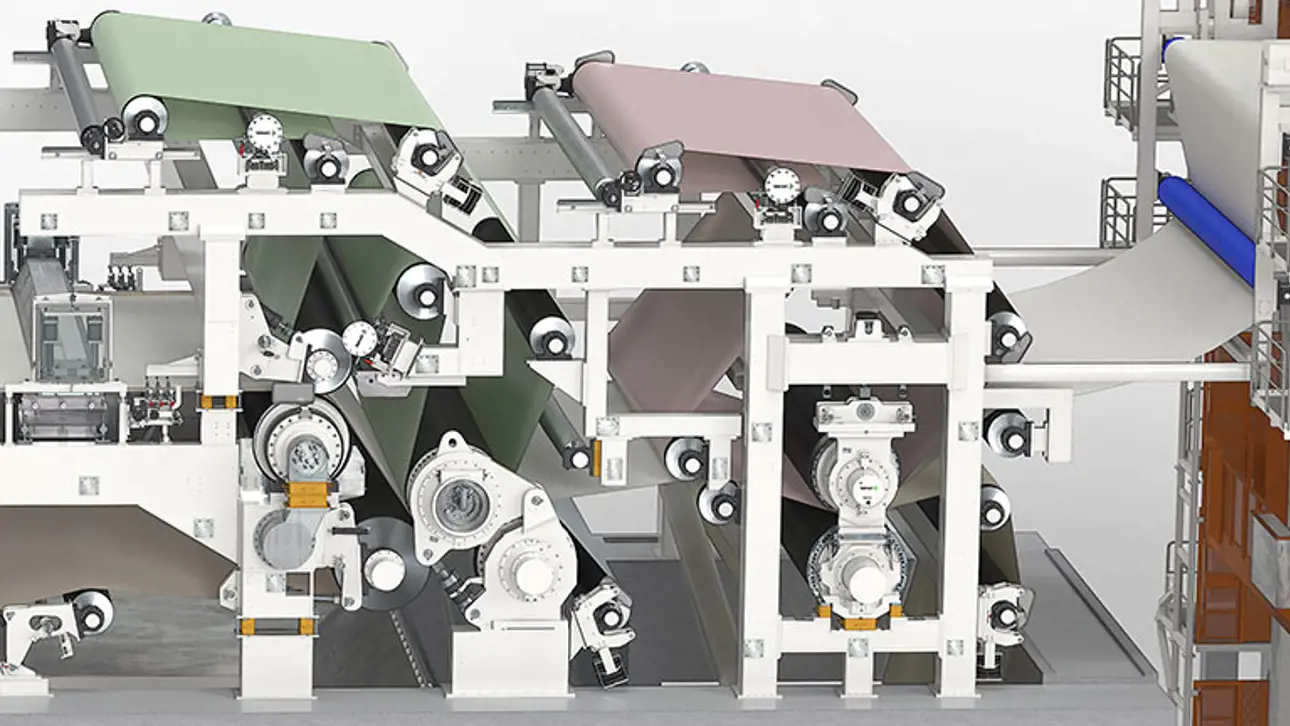
The press section consists of Valmet Combi Press with two nips and Valmet Shoe Press. The first open draw of the web is after Valmet Combi Press, when dryness is more than 40% and web is already very strong. Valmet Shoe Press gives higher dryness of web before it enters into Valmet Airborne Dryer.
Provides high dryness
Some 60% of the removed water flows to the counter roll, while the rest is removed by the top felt. Because of the long nip, web dryness exceeds 40% when leaving the press section.
Savings in steam costs
With two shoe presses, the Wet end is able to provide higher dryness values and savings in steam costs for any kind of pulp.
Good runnability
High dryness in first open draw ensuring good runnability and less web breaks.
Automatic tail threading
An automatic tail-threading device takes the tail to the dryer and secures fast and safe tail threading at high speeds.
The first nip of Valmet Combi Press consists of pick-up suction roll on top and wire turning roll on bottom. Web is between felt (pick-up felt) and wire. Line pressure in the nip is max 60 kN/m. Second press is double felted, it consists of same pick-up suction roll and pick-up felt as in first press and second press bottom roll and a felt. Design line pressure is 170 kN/m.
The second press is a Valmet Shoe Press, i.e. double felted press with extended nip and which operates with high nip load, typical design nip load is 1250 kN/m. Extended nip gives more dwell time and together with high nip load gives higher final dryness of web than traditional felt press.
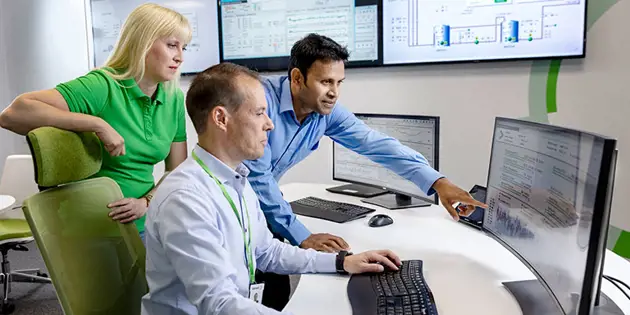
Our expertise is at your service
We at Valmet are committed to moving our customers performance forward and ensure smooth, disruption-free operation, supporting you all the way.
Contact us