Forming Section
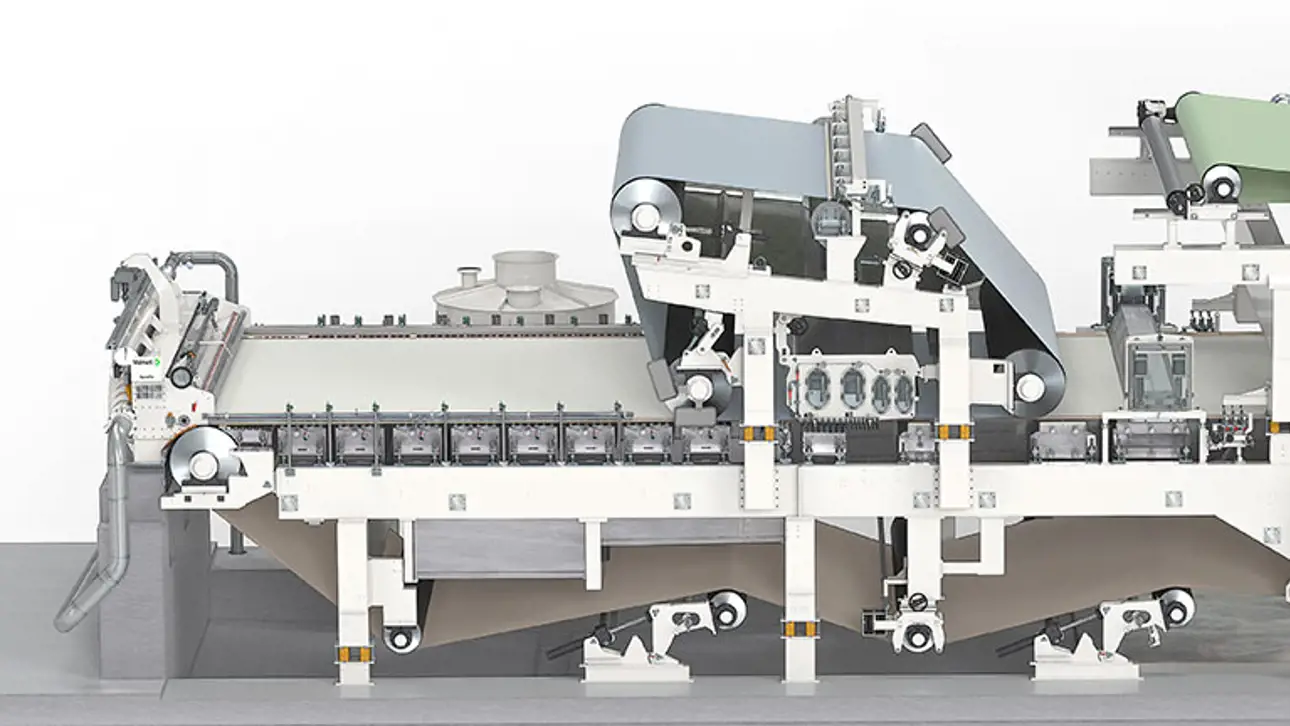
Valmet wet end concept offers the widest scope on the market. What ever the need, we have a suitable solution for the application.
Valmet Fourdrinier Former
Application: Softwood, Fluff pulp, Flexible for different pulp grades and properties.
Valmet Gap Former
Application: Pulp with low dewatering properties and very high capacity machines
Valmet Top Former
Application: Hardwood, High capacity, Market pulp, Dissolving pulp.
Valmet Fourdrinier Former
The Fourdrinier type wet end provides extreme flexibility for varying production rates, basis weights and pulp qualities, thanks to several adjustable parameters including headbox slice. In addition, the Fourdrinier type features long wire lifetime and disturbance-free operation. For maximized dewatering the Fourdrinier can be furnished with a top former. Alternatively, the top former can be installed at a later stage when an increase in production becomes necessary.
Valmet Gap Former is the result of continuous development
The Valmet Gap Former represents the latest evolution of double-wire formers featuring effective, controlled two-sided dewatering. Web formation takes place in a fully controlled, adjustable former section.
The Gap former utilizes mechanical dewatering methods in all consistency areas and thus avoids practically all such losses. In low consistency area from the headbox to the sealing unit, water is removed in an airless, controlled former section.
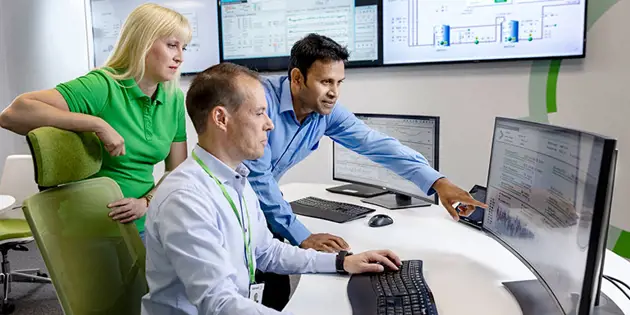
Our expertise is at your service
We at Valmet are committed to moving our customers performance forward and ensure smooth, disruption-free operation, supporting you all the way.
Contact us