Flow control for air separation
Improving reliability and productivity of your process
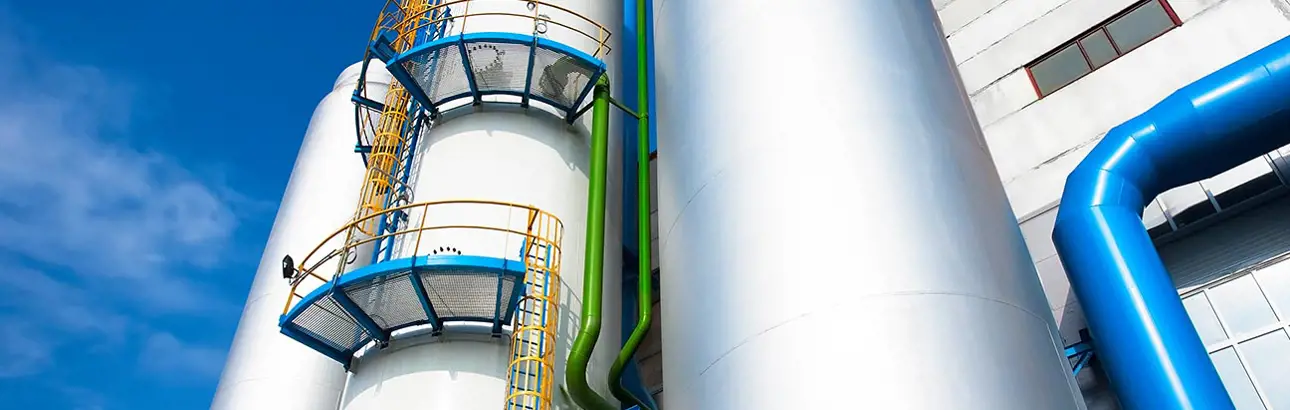
Valmet's products and experience cover the entire Air Separation Unit (ASU) process from the compressor and purification through the cold box to tank loading and distribution. Our industry-leading metal and soft seating technology are ideally fitted for specific cold box requirements – the core of the air separation process. Using our vast experience the correct materials needed for hazardous oxygen applications can be selected. The proven high reliability and long lifecycle make Valmet the world leader in cryogenic valves. Continuous plant availability can be ensured with intelligent online diagnostic capability.
Reliability
Long lifecycle
Plant availability
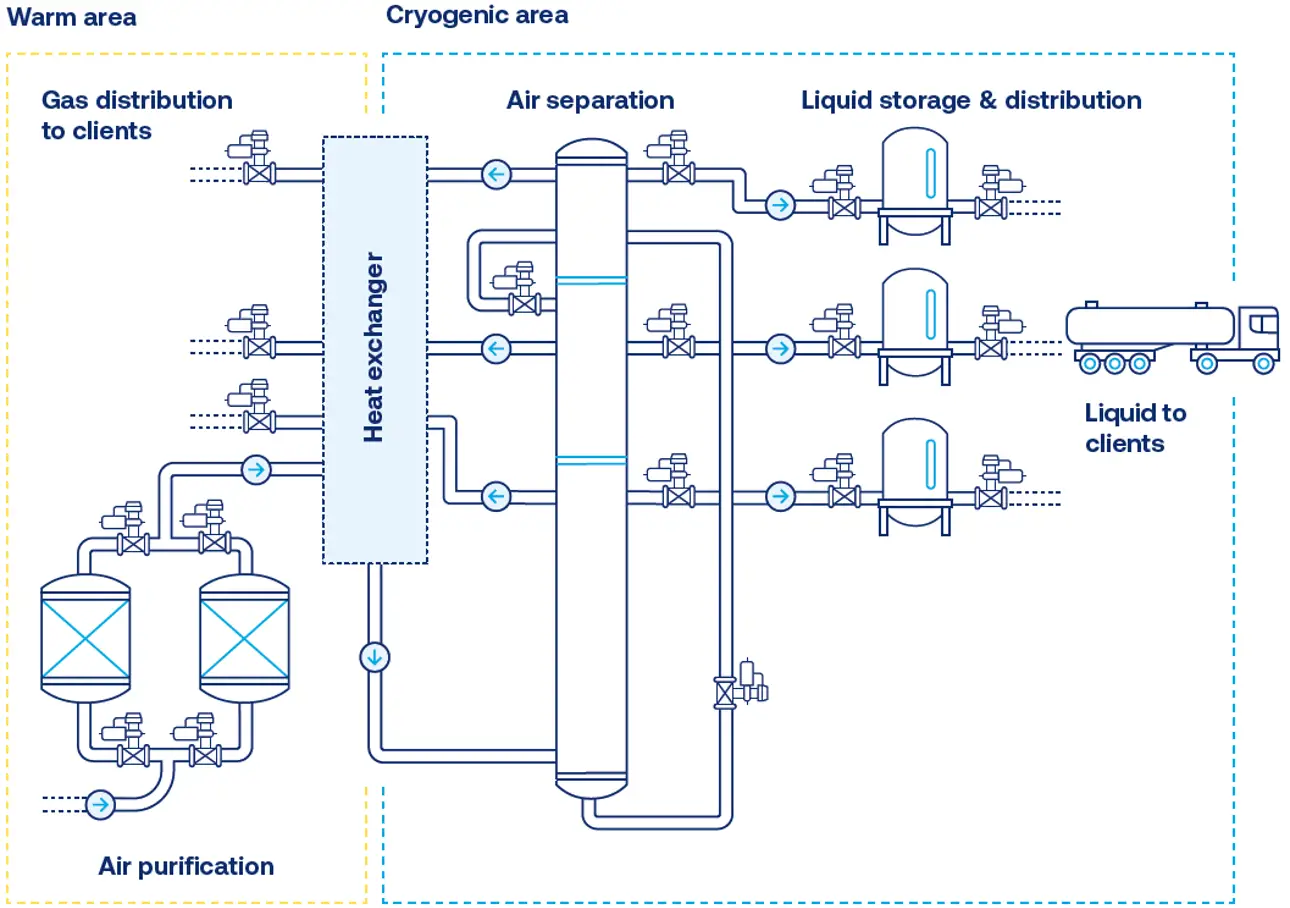
Air separation unit process flow
Air purification:
- Challenges include cycling valves, humidity, molecular sieve protection, temperature swings (ambient to 300˚C)
- Specifically designed 3-lever valves that only allow opening at low delta pressure (dP) to ensure the protection of the molecular sieve adsorbers
Air separation and liquid storage & distribution:
- Cryogenic valves with extended shaft design and possibility for horizontal shaft mounting installation
- Valves allowing maintenance of internals on welded valves of the cold box
- Valve design providing long-lasting safe tight shutoff and excellent controllability in operation avoiding hazards and production interruptions
- Our portfolio is suited for use in cryogenic environments and complies with oxygen requirements
Reliable flow control and services for air separation
There are a number of critical valves throughout air separation plants. Those applied in cryogenic service carry a unique set of challenges. Extreme temperature swings and oxygen-rich environments put considerable stress on valves. Great attention must be paid to every detail from metallurgy to the lubricants used to prevent hazardous sparking and ignition situations.
Keep cool under pressure
Rotary valves installed within the cold box will need neck extensions, which often need to be custom built and welded. These extensions must withstand considerable torque at temperatures below -185°C/-300°F and be able to do so reliably for many years.
Valves destined for cold box usage must be fitted with high-strength neck extensions, while actuators must provide sustained high torque capabilities over long periods of time.
Leakage in this service must be prevented from the seat and seal into the pipes and through the neck into the packing. This requires special polymers to be used in the seat while shaft leakage must be contained by installing the neck at the exact right angle from the point at which cryogenic materials enter.
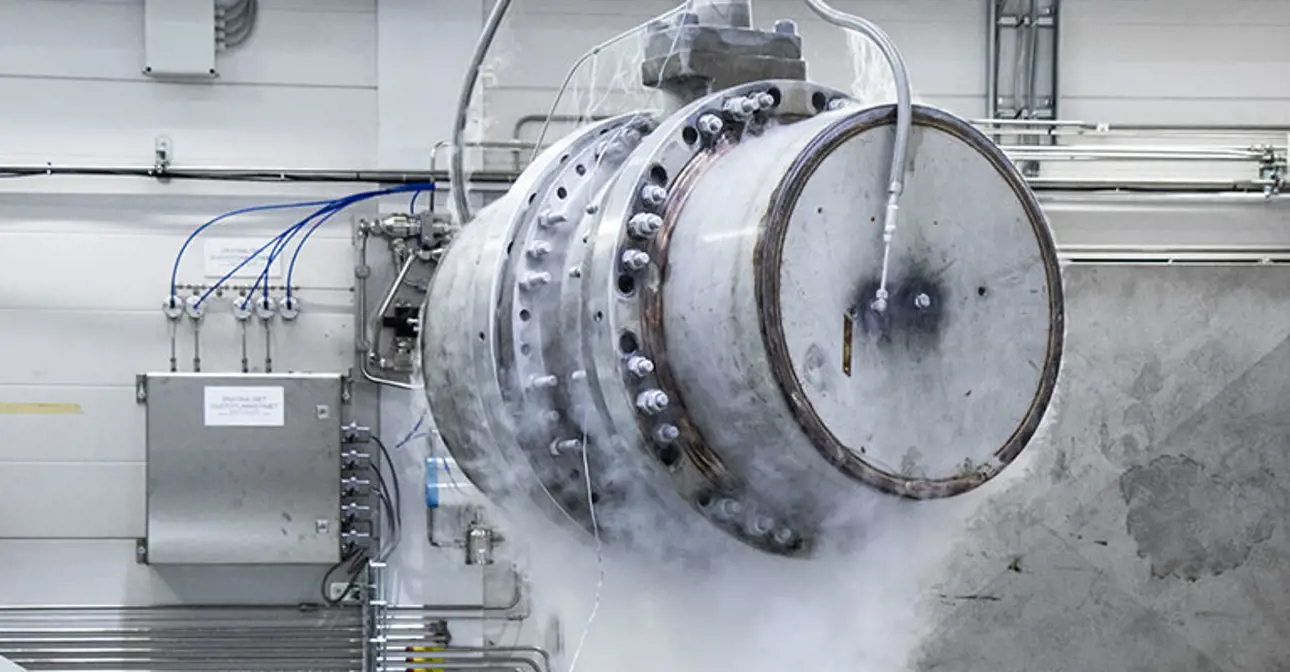
Ideal solution for industrial gas reliability
At Valmet, we understand that industrial gas manufacturers are under intense pressure to deliver. As such, we organize our service offering and comprehensive product line to provide a total solution that can help you to achieve higher levels of productivity and reliability from day-one through the entire lifecycle of your plant.
Our staff, with extensive application knowledge and industry experience, will start by helping you to size the valves and actuators needed to keep your process running for long periods. Then, especially for critical applications, we will recreate conditions of your process in our lab to verify performance and use our proprietary software to confirm that the ideal valve and actuator sizes are being used to prevent premature wear, over torquing and boost your operational uptime.
Our cryogenic valves are the result of extensive R&D efforts and testing within our state-of-the-art cryogenic lab. We use advanced materials of construction, including Monel, that are proven to overcome process conditions of oxygen service and extend the time between scheduled maintenance. We have also developed seat, seal and boot designs that prevent leakage of cryogenic material into the pipe. We validate this by helium testing valves immersed in nitrogen and confirming there are no leaks.
Outperform with a total solution
Valmet is committed to helping our industrial gas customers outperform. Our experience in the field overcoming your application challenges is evident throughout your relationship with us, from the sales and sizing phase to supporting a long-term maintenance strategy.
- Unrivaled process uptime and plant availability
- Reduce total cost of valve ownership over product lifecycle
- Optimize efficiency and reduce waste
- Mitigate safety concerns and minimize environmental impact
- Comprehensive sales and service support
- 24/7 OEM maintenance and support
Flow control solutions and services for air separation
Read more about our solutions for industrial gas processing