How a rebuild can make a difference
Aug 21, 2023
The Advantage™ ViscoNip® press and ReDry™ rebuilds at Sofidel’s tissue mills demonstrate benefits related to improved product quality, increased flexibility and machine runnability. In line with their multi-option strategy for reducing environmental footprint they also contribute to lower energy consumption.
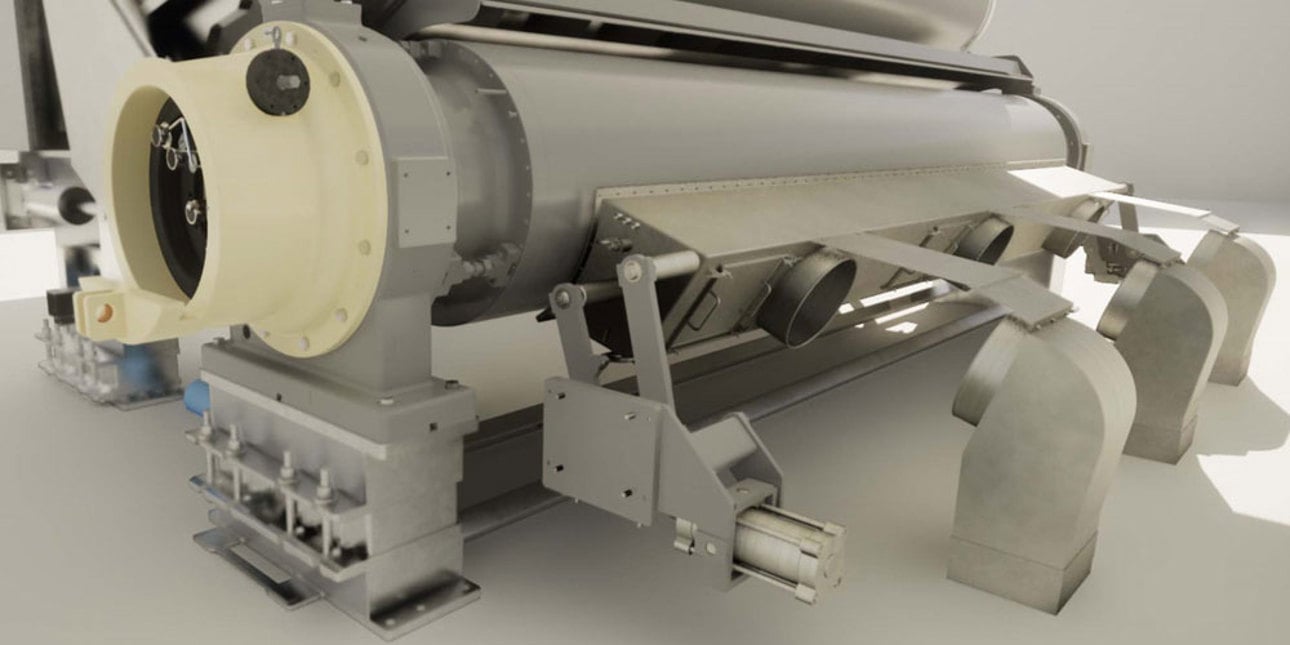
For Sofidel, sustainability has been high on the agenda for many years. In fact, in 2009, they were the first Italian manufacturing company and first tissue player in the world to join the international program WWF Climate Savers. In the two initial phases of their sustainability journey, from 2009 to 2020, Sofidel managed to reach an impressive 24% reduction in carbon intensity. Meaning direct emissions generated by the company, the source of which is owned or controlled by the company and indirect emissions generated by energy purchased and consumed by the company.
The Sofidel approach to achieve a low-carbon economy includes a multi-option strategy. One factor consists of reviewing components in the tissue machine where energy savings and production efficiency can be made. Being introduced to the opportunities of the Advantage ViscoNip press and the Advantage ReDry the decision was made to start two rebuild projects – one in Baglan, UK, and one in Kisa, Sweden.
With the ViscoNip press, the uniform cross machine direction operates over a wide range of linear loads, which opens for extensive possibilities to develop products. Low linear load provides highest possible softness while high linear load improves energy and production efficiency.
Francesco Corrotti, Operating Coordination Director at Sofidel
Francesco Corrotti, Operating Coordination Director at Sofidel reflects on the findings so far, “In Baglan we replaced the suction press roll installed on the Advantage™ DCT 200 machine with a ViscoNip press and also added the ReDry. We have seen, after 5 months of running the machine, about 20% reduction of drying energy consumption even though we are still in the so-called learning curve phase. We have also experienced less web breaks; the paper that comes off the blade is more uniform. This was also noted immediately in the converting mill where they now have more stability in the sheet”.
We have seen an improved flexibility. Linear load and load ratio is easily changed during operation without any disturbance on the quality or runnability of the machine”.
The graph demonstrates the performance before and after the rebuild. With the installation of the ViscoNip the dryness was increased by 3.5 - 4% compared to the single suction press roll, green line vs. grey line. The blue line demonstrates how additional dryness was reached immediately after the addition of the Advantage ReDry. The synergy between the two is what causes the additional dryness level. The ReDry further enhances dryness by utilizing exhaust air and humidity from the hood to heat the web and thereby increase press dryness.
During the same period as the project in Baglan another ViscoNip press rebuild was ongoing at Sofidel’s mill in Kisa, Sweden. Since the start-up results show good runnability and moisture profiles. And like Baglan, a flexibility in terms of changing ratio from maximum to minimum without any issues.
“At the Kisa mill we have also seen an improvement of felt and mostly belt lifetime. Our perception is that the ViscoNip press seems to be gentler towards the belt. As of today, 7 months after the startup the machine is running with the same start-up belt without any sign of wearing. This is of course very positive in terms of reduced maintenance cost”.
The graph indicates results from the Kisa mill measuring press dryness and hood gas consumption development. The press is responsive when it comes to sheet dryness and gas consumption as we can see a proportional correlation with the dryness and the nip pressure itself.
Perhaps more interesting is the finding in below graph. We can easily switch from one situation, in terms of bulk, to another by changing the ratio and linear load with good flexibility.
Corrotti summarizes, “With these rebuilds we can now play with bulk and tensile simply changing the ratio and linear load very easily. This is very good for our final products and, at the moment we are very satisfied with these two rebuilds”.
These rebuilds represents one part of Sofidel’s strategy to minimize the carbon footprint in tissue production. Some other examples of actions are to increase the use of purchased energy from renewable sources with long-term agreements (PPAs - Purchase Power Agreements), to adopt innovative technologies to reduce CO2 and to increase self-generation of energy from renewable sources. Examples of achievements so far includes wind farms in south of Italy and Spain from where they buy the energy from. Another new project, soon to be started up, is the production of bio-syngas for feeding the hood of both their machines at the Sofidel Kisa site in Sweden.
The target for 2030 is to reach a 40% CO2 emission reduction and 24% GHG emission per ton of paper. With these demanding goals the company has been forced modify its way to operate in many aspects. But hard work and dedication pays-off, in 2022 the carbon intensity reduction was reported to be -15.7% compared to 2018 and the journey continues.