Coater bottom waste reduced at Burgo Villorba | Valmet
Aug 20, 2018
The off-machine coater at Burgo Villorba’s paper machine PM 8 in Italy is making good use of Valmet Water Jet Turn-up Device and our knowhow. With over 99% roll change performance efficiency, they have reduced the amount of bottom waste significantly and increased the average speed of the coating machine by 100 m/min, and they are now operating more safely.
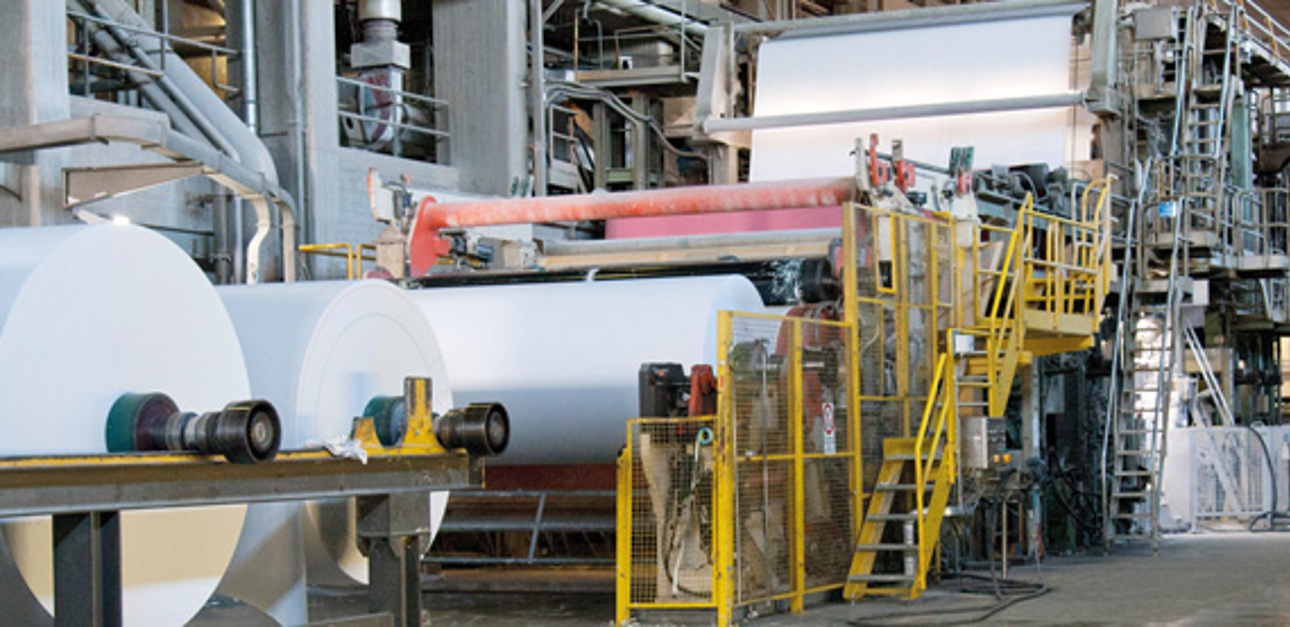
Although it was effective, our old system was causing the sheet to wind onto the spool unevenly and creating a lot of reject in the unwinder and calenders,” says Mill Manager Massimo Sponchiado, about the situation before the investment. “On top of that, we were not happy with the speed of the coating machine. To turn up and splice successfully, we always had to reduce the speed of the machine, which didn’t do our efficiency figures any favors,” he continues. Given their previous experience with Valmet’s knowhow and the success of Valmet Water Jet Turn-up Device installed at their Duino mill, they entrusted Valmet with the task of resolving these challenges.
“We liked Valmet’s holistic view, and their willingness to help and solve problems. It was not just about setting us up with new equipment – they checked the whole process and optimized the reel operations together with us,” says Sponchiado.
Earning trust
The Water Jet Turn-up Device was installed in 2015. “The tuning of the system was not immediate, but we’ve always had very good co-operation with Valmet. It is not something we take for granted,” Sponchiado points out, explaining that Valmet has proved itself worthy of their trust. As well as having an expert on-site during process studies and start-up, the Villorba mill has found having
remote services useful. “We’ve got expert services by phone and email, with very good availability. I remember very late one Friday evening we were having some challenges. Petri Mustonen, Valmet’s expert, was at a birthday party with his family, and despite this, he was on the phone and he was helping us. We heard the music in the background, but he was there, solving the problem with us,” says Sponchiado, laughing.
Massimo Sponchiado, Mill Manager of Burgo Villorba (on the left), is happy with Valmet Water Jet Turn-up Device. On the right, Mill Sales Manager Maurizio Sala of Valmet.
Change of parent roll quickly and cleanly
The targets of the project have been reached. "The amount of bottom waste has reduced from several centimeters to less than 5 mm. We've also achieved our finaltarget of a flat speed profile for the coating machine, and the average speed of the coating machine has increased by 100 meters a minute," Sponchiado says. The system is also reliable, with efficiency values of 99%. "We never have breaks during turn-up operations, some during splicing," he confirms.
Completely automatic operation increases safety
“Operator safety has improved a lot. With the previous system, the operator had to intervene manually during the splicing with an air gun to keep the paper sheet in the right position. Now, the operator waits for the turn-up in the control room,” says Sponchiado. The mill has been focusing on safety issues and creating an even better safety culture. “Safety is not a question of money, but of attitude,” he says, adding: “In 2012, we achieved a lower incident frequency alongside a daily production record. We’ve seen that working on safety increases productivity, too, as you increase the efficiency of the people.”
How does the turn-up system work?Valmet Water Jet Turn-up Device is needed in reel spool changes in the paper machine. With Water Jet Turn-up Device, two water jet nozzles traverse to the middle of the machine to initially cut a fine strip in the middle of the sheet. The strip is glued to the empty spool, after which the nozzles quickly traverse to the sides and widen the strip. As a result, the device ensures consistent, fast and clean parent roll changes. |
Published in Forward 1/2017