Q&A with Neles expert: Jing Cao
Oct 20, 2020
How has COVID-19 affected customer inspections? We talked briefly with project engineer Jing Cao, to find out more about Factory Acceptance Tests, and what is going on in the factory. In addition, we asked a few things about her career at Neles (now part of Valmet).
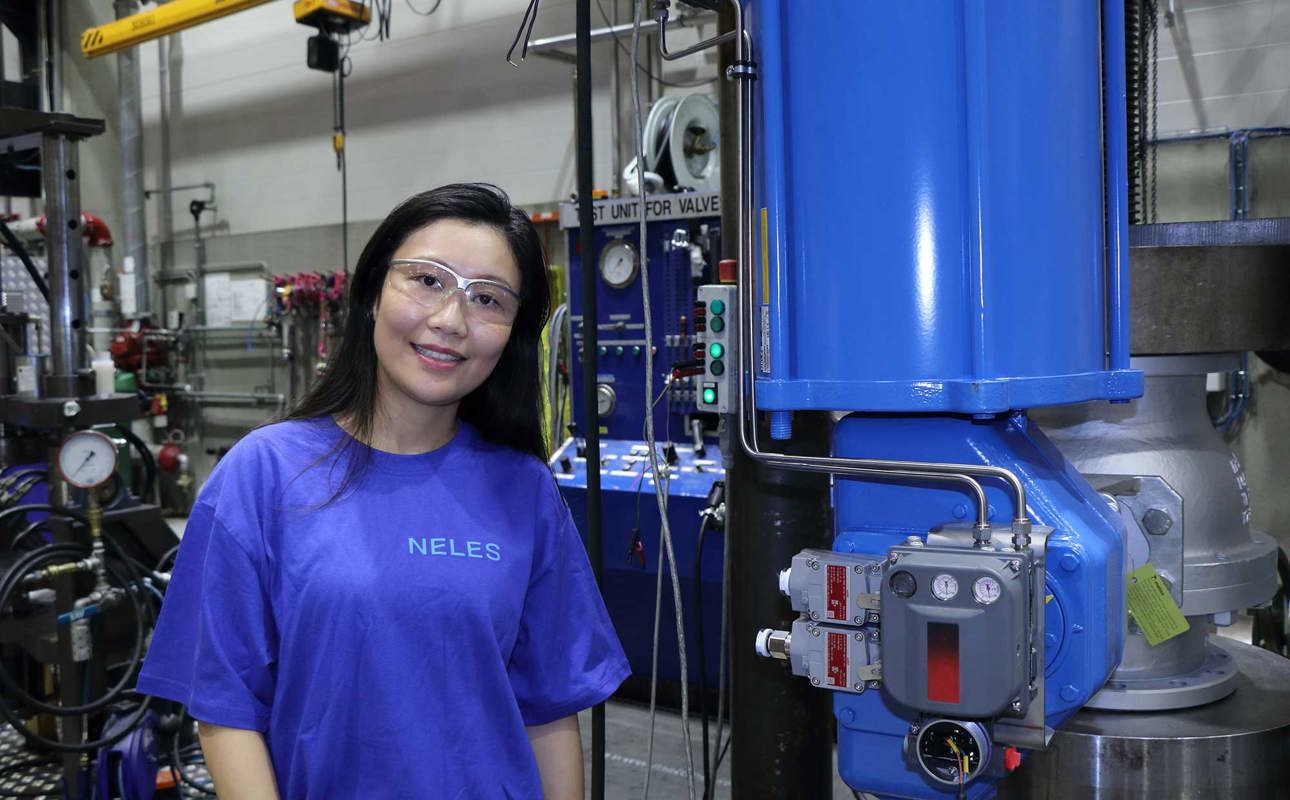
Q1: What do you do at Neles and what is your background?
I work as a project engineer in the Project department at our factory in Vantaa, Finland. We use a Lean System here; this means that the project engineers are divided into four different groups. We have a specification team, a documentation team, a product selection team and a group of inspection engineers, where I’m currently doing FATs. We are the last team in the whole Project process. Our team also offers the possibility for job rotation, which is nice.
I joined Neles (that time still Metso) in 2018. Originally, I grew up in Shanghai, China; I came to Finland to study mechanical engineering, and then I ended up staying here.
Q2. What is an FAT and why do we do them?
We basically check each single valve that goes out of the factory. FAT stands for Factory Acceptance Test. An FAT includes a pressure test, seat leakage tests, an operational test and a visual test. During the manufacturing process, we do internal tests for all bare shafts. Therefore, results of an FAT are quite satisfying. An FAT is requested because the client thinks they are critical, but we also do FITs (Factory Internal Tests) for complete valve-actuator combinations without the presence of a customer or 3rd party inspector.
Our valves are mainly used in demanding conditions and in industry areas with safety concerns. Certain valves have such high requirements that the customer wants to examine and ensure their performance at the designed conditions. I usually meet weekly with various customers and inspectors from all around the world. We will check their items and see if they match the requirements for their needs. After that the valves can be packed for shipping to our customers.
Q3. How has COVID-19 affected customer inspections? How has Neles served its customers during the time of the coronavirus?
Before Covid-19, clients would normally come here (to Finland). To prevent the spread of coronavirus, customers cannot visit our factory at this time. In order to ensure that our customers’ valves are manufactured according to their requirements, Neles carries out FAT by the inspection engineers, including photos and video. In specific cases, and if resources allow, we have offered live stream inspections.
Q4. How do you conduct remote inspections?
The remote FAT is still under development; we’re considering headset cameras and other high-tech devices. At this moment, we use apps like Teams and Zoom for face to face meetings on smartphones. The remote FAT must be evaluated case by case to comply with the inspection requirements and to allocate resources. Currently, we need at least two project engineers to perform a live stream FAT.
Our goal is to keep our customers happy. Even during the most challenging times we have been able to successfully complete FATs every day, without any interruptions.
Q5. What motivates you at work?
My job requires me to be a decision maker. The freedom of making decisions increases my motivation and job satisfaction. When I overcome a challenge, it makes my work meaningful, and doing FATs really gives me a chance to solve different challenges. It makes me feel that each effort counts in completing projects successfully.
Q6. What’s your team’s greatest achievement?
Our goal is to keep our customers happy. Even during the most challenging times we have been able to successfully complete FATs every day, without any interruptions.
Text originally published in 2017, and slightly updated in April 2022, due to the company name change to Valmet. As of the 1st of April 2022, Neles is part of Valmet.
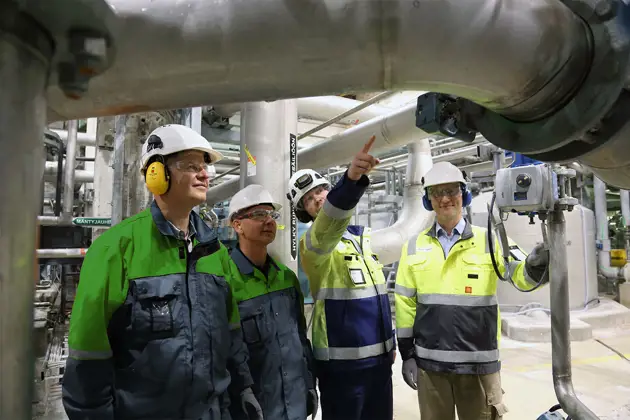
Subscribe to our newsletter
Subscribe now to our 'Go with the flow' newsletter and receive the latest insights directly to your email.
Subscribe