Optimized sludge dewatering saves costs
Mar 22, 2019
By investing in a Valmet Sludge Dewatering Optimizer (Valmet SDO) and online solids measurement units, Lappeenrannan Lämpövoima’s Toikansuo wastewater treatment plant has been able to boost sludge dewatering efficiency and lower costs in further sludge treatment, among others.
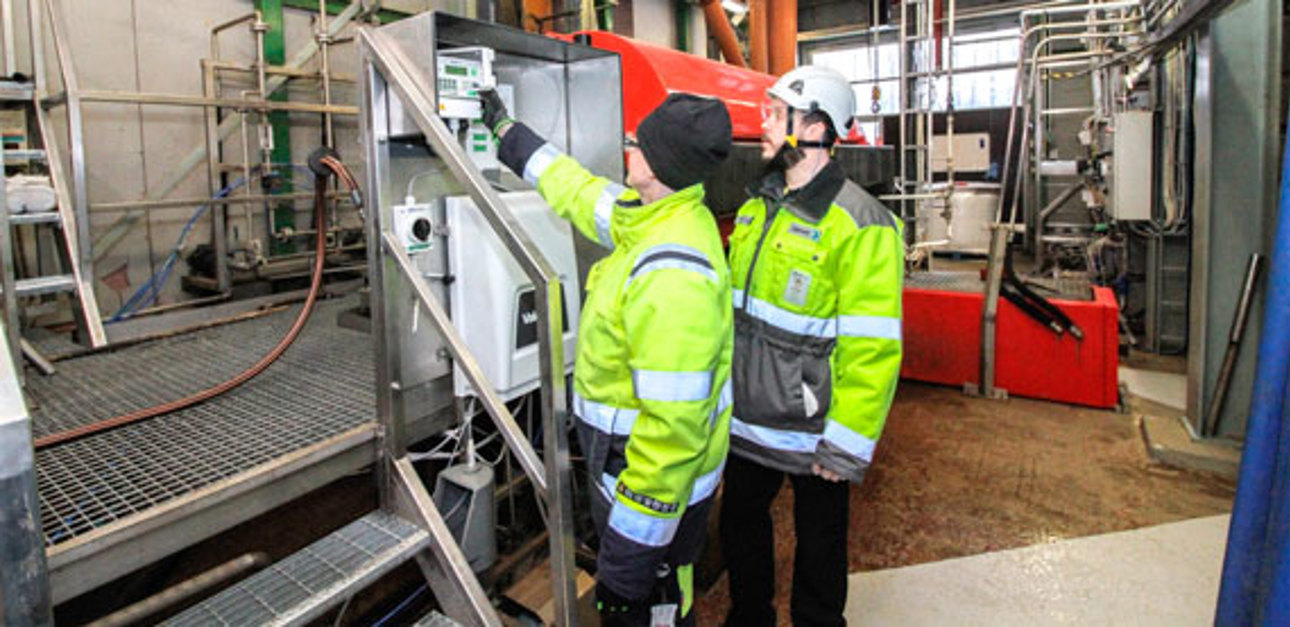
With a population equivalent of 100,000, the Toikansuo wastewater treatment plant, located in the city of Lappeenranta, Finland, produces about 600–800 tons of sludge per month, which is transported to the nearby waste treatment plant for composting. The wetter the sludge, the more it weighs and the more its later treatment costs. More sludge tons need to be transported, too.
“Our target has been to increase the sludge dry content and thereby decrease the amount of sludge that is sent to composting. This would bring savings in our disposal costs,” says Päivi Rissanen, a wastewater treatment plant operator atLappeenrannan Lämpövoima.
Lappeenrannan Lämpövoima’s Toikansuo wastewater treatment plant
Earlier, the plant ran its dewatering processes manually and observed sludge quality only visually. Laboratory measurements of the sludge feed, dry cake and reject solids content were carried out about once a week.
“We considered other suppliers’ online total solids measurement solutions, too. When we found out that Valmet had a dewatering optimization solution with which it would be possible to lower sludge disposal costs, we chose Valmet to be our supplier. To my knowledge, Valmet is the only supplier that offers this kind of dewatering optimization application,” Rissanen continues. “We expect optimization to improve our dewatering process and make sludge quality more consistent.”
Dryer cake, higher dewatering performance
The Toikansuo plant has two dewatering units that usually run from six to eight hours every day of the week. In early 2018, Valmet supplied two Valmet Total Solids Measurement units (Valmet TS) for the drying unit that produced wetter sludge than the other one. One Valmet TS was installed to measure the sludge feed into the dewatering unit and the other one to measure the dry cake. This reliable total solids measurement solution, based on microwave technology, is suitable for all wastewater sludge treatment applications in the range of 0–40% total solids.
Valmet Total Solids Measurement (Valmet TS), based on microwave technology, is suitable for all wastewater sludge treatment applications in the range of 0–40% total solids.
Also, the plant had a Valmet Low Solids Measurement unit (Valmet LS) installed to measure reject water within the solids range of zero to 5,000 mg/l and a Valmet SDOto improve the control of the sludge dewatering process. The first results achieved with all Valmet solutions have been very promising.
“We have been able to reach a few percentage increase in the dry solids content. However, the optimization application has been on only for a short time, so we have not been able to see trends over a longer period of time,” Rissanen says. “Thanks to online measurement data and Valmet SDO, we have more boldly increased the amount of the sludge feed into the dewatering unit. We are now closer to its maximal capacity of 40 cubic meters per hour than before. This means that its performance is now higher.”
Valmet Low Solids Measurement unit (Valmet LS) measures reject water within the solids range of zero to 5,000 mg/l.
Unlike at many wastewater treatment plants, there is no digestion tank or any intermediate treatment before the sludge dewatering at Toikansuo. As sludge is fed directly into the dewatering unit, all process changes, winter or summer running modes, or disturbances have an impact on the sludge quality. This means that there is more variability than at a plant where the sludge is anaerobically digested and more homogenous. But luckily, the plant now has a Valmet SDO to solve this issue.
Fewer disturbances and inspections
The Toikansuo wastewater treatment plant is not staffed 24/7. When there is nobody around, the process is monitored via a remote connection. Valmet’s measurements and optimization solution are connected to the Valmet DNA automation system used by Lappeenrannan Lämpövoima’s energy production via a Valmet Industrial Internet solution. There is a user interface in the wastewater plant control room, too.
Team leader Miikka Kippola is one of the seven technicians who run the dewatering units. He has noticed the benefits brought by the new online solids measurements and the optimization application. “Dewatering unit performance is more stable than before, and there are fewer disturbances. The entire time, we now know the sludge throughput, polymer consumption and dry solids content. Earlier, we ran the process almost randomly, but now the application controls everything automatically.”
Additionally, the technicians no longer need to check on the dewatering unit four to five times per day and add the needed chemicals. Instead, they can use all that saved time for other tasks and monitor equipment performance in the control room.
Equipment performance is monitored in the control room
Higher reliability through a service agreement
Päivi Rissanen appreciates the efficiency with which Valmet people have worked on the project. Close cooperation, hands-on training and fruitful discussions have been carried out in a positive atmosphere. “The more we talk with each other, the better understanding we have,” she adds.
What about the future? Well, a lot is going on. The Toikansuo plant aims to reap even more benefits from its new online measurements and optimization application. Also, there are plans to add one solids measurement unit to measure the raw sludge and ensure its sufficient dryness before it enters the sludge thickener.
The plant and Valmet will continue to further improve the process in close cooperation. For example, there are ongoing discussions about including the solids measurement application and the Valmet SDO in the service agreement that Valmet has with the parent company to monitor energy operations. “The service agreement with its regular maintenance actions will ensure measurement reliability and availability long into the future,” Rissanen emphasizes.
Related articles