Take the pressure off of stressed oil and gas processes
Sep 27, 2012
Adequate risk reduction calls for efficient depressurising systems in oil and gas processes. Intelligence, which leads to safety and reliability in depressurising valves, can be found in Neles’ advanced solutions.
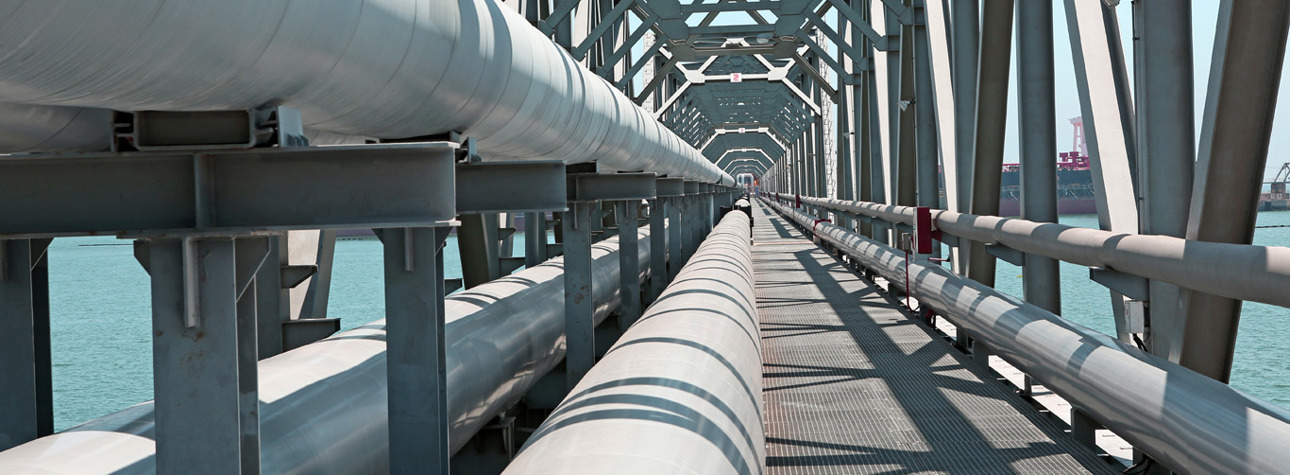
Oil and gas processing facilities today are facing growing challenges to meet environmental and health and safety requirements, while maximising product output and quality. With increasing energy prices, process plants are constantly being set new challenges to further develop their processes and maximise the yield of valuable products in an energy efficient way. Plant run time targets are increasing, meaning more challenges are set for equipment reliability and safety. Depressurising systems are used to reduce the failure potential for scenarios involving overheating, such as fire. When metal temperature is increased due to fire, exothermic or runaway process reactions, the metal temperature can reach a level where stress rupture can occur. Depressurising reduces the internal stress, extending the life of the vessel at a given temperature. A relief valve cannot provide adequate risk reduction or safety to depressurise a vessel: it can only limit the pressure from exceeding the process upset point. Therefore, depressurising valves are used to reduce the risk of losing equipment integrity.
“With increasing energy prices, process plants are constantly having new challenges set to further develop their processes and maximise the yield of valuable products in an energy-efficient way.” Sari Aronen, Application Engineer
System requirements and practices
In many cases, a process plant or unit is equipped with two different kinds of depressurising systems: a slow system and a fast system. The slow system can also be labelled an operational depressurising system, while the fast can be called an emergency depressurising system. Valve capacity should be accurately matched to the process conditions in order to verify that depressurising is not done too fast.
A slow depressurising system is intended for process control or for other operational reasons. It is meant to be used as a first means of controlling the process before the fast system is taken into consideration. Slow depressurising systems can be initiated manually from the control room, locally from the field or automatically by the distributed control system (DCS) if predetermined limits are exceeded. A slow depressurising system is, in most cases, used in parallel with a fast emergency depressurising system. It should be closed when high rate emergency depressurising valves are operated due to the limitation set by flare capacity. An emergency depressurising system is typically required for hydrocrackers, catalytic reforming units and process heaters. Fast depressurising systems are used in emergency situations to quickly evacuate the system. They can be initiated manually by the operator or automatically by the safety system. High safety integrity is required from valves to provide adequate risk reduction. Common requirements include the ability to match trim capacity to process conditions, tight shut off, noise reduction capabilities and emission control. Actuators should be single acting and spring to open, because the valve must be open in the case of air failure. High actuator safety factors (e.g. 1.5 – 2) are usually required. An operational depressurising valve is normally equipped with a solenoid valve and a valve controller for dual function of the valve. Instrumentation related to an emergency depressurising valve may be more complex compared to slow depressurising valves with redundant solenoids and voting logic to meet high safety and reliability requirements. An instrument air buffer vessel may also be required.
Solutions
The depressurising time may need to be modelled to verify the valve’s performance during depressurising. In order to match the process requirements accurately, flow capacity of the trim should always be verified by means of testing and calculation. Intelligent digital valve controllers are suitable for all kinds of operations, from process control to fast emergency operations. Online diagnostic capabilities and online partial stroke testing for emergency valves is highly recommended for critical, demanding applications such as depressurising.
Customer challenge
· The safety of operating personnel and equipment integrity are in the list of top-priority issues faced by oil and gas processing facilities.
Our solution
· Neles ensures efficient operation of the depressurising systems with a combination of properly selected and sized valves with intelligent valve controllers.
Key customer benefits
· With Neles’s solutions for depressurising systems, customers can use predictive maintenance planning and test the performance of valves while the process is running.
Intelligence
Unnecessary flaring is something that every oil and gas process plant operator wants to avoid, since it is a sign of product loss and a safety risk. Long lasting metal seated tight shut off valves provide the means for reduced flaring while the process is running by keeping the valves tightly closed. More benefits can be realised in fire emergency conditions due to their fire proof construction. Rotary valves provide the wide rangeability required with a single valve solution. Reliable valve operation is ensured even in conditions where there are particles in the fluid, due to their non-clogging design. Hidden failures can be revealed without flaring by partial stroke testing, which is applied for emergency depressurising valves by utilising the ball valve dead angle without flow passing through the valve while the process is running. Intelligent partial stroke testing can be automatically initiated through the DCS or safety instrumented system (SIS).
With the inbuilt diagnostic capabilities of the intelligent safety valve controller, the performance of the depressurising application can be tested with high diagnostic coverage and without additional isolation valves. This also provides longer proof test intervals and increased plant uptime in targeted safety integrity levels (SILs). Maximum availability and extended plant uptime is achieved with valves equipped with diagnostic tools that are capable of online condition monitoring. Trends, such as load factors, warn users automatically without manual work. An intelligent partial stroke device saves labour hours and improves the safety of the plant by revealing failures in the complete valve assembly. Modern asset management systems provide the end user with an opportunity for predictive maintenance. Common cause failures can be reduced with intelligent valve controllers in redundant instrumentation. By replacing one of the redundant solenoid valves with one intelligent partial stroke device, the safety requirements can be met using a single valve solution.
Valve diagnostics in modern safety valve controllers, such as Neles’s Neles ValvGuard™, are also available during the emergency trip. Full stroke testing with inbuilt diagnostic information can be used as a proof test during shut down periods, and a test report can be easily generated through asset management software. Therefore, intelligent valve controllers provide added value without partial stroke testing. The reliability verification of final, high end elements (such as valves in depressurising systems) can be achieved by using calculation tools in the early phase of the project. Software, such as SIL calculation tool, is able to verify the SIL capability and probability of failure in demand (PFD) value, even for complex final element subsystems relating to a complete valve assembly. This is achieved by using accurate field proven reliability data.
Conclusion
Adequate risk reduction calls for depressurising systems in oil and gas processes involving overheating scenarios to ensure safety of operating personnel and equipment integrity. Intelligence, which leads to safety and reliability in depressurising valves, is a combination of properly selected and sized, reliable valves with intelligent valve controllers. These are essential for predictive maintenance planning and testing of valve performance while the process is running.
Text by Sari Aronen
Published in Hydrocarbon Engineering, October 2012 as 'Take the pressure off'
Text originally published in 2012, and slightly updated in April 2022, due to the company name change to Valmet.
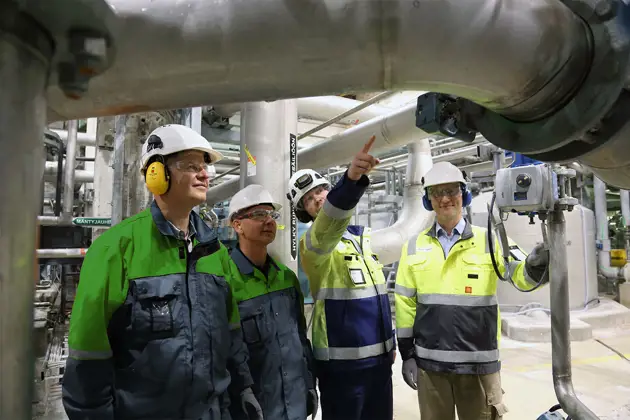
Subscribe to our newsletter
Subscribe now to our 'Go with the flow' newsletter and receive the latest insights directly to your email.
Subscribe