Aromatics processing made safe and efficient with proper valve selection
Dec 2, 2013
For reliable and safe aromatics processing, the valve selection and sizing should be done carefully. Understanding the design limitations of each valve type is important to eliminate health risks, reduce maintenance needs and assure good process performance with such demanding flow media.
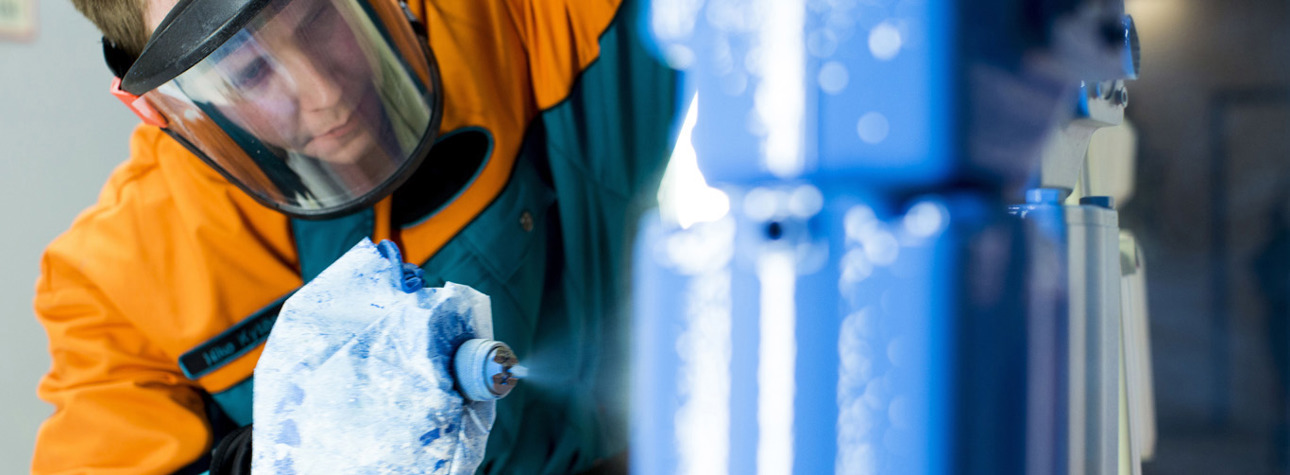
The aromatics group, together with the lower olefins, such as ethylene and propylene, provide the basic building blocks of the modern petrochemical industry. Clothing, packaging, paints, computers and compact discs among many other products rely on aromatics.
Highlights
· The aromatics group provides the basic building blocks of the modern petrochemical industry.
· Clothing, packaging, paints, computers and compact discs, among many other products, rely on aromatics.
· Worldwide, approximately 110 million tons of the main aromatics, including benzene, are produced annually.
According to Axens, paraxylene (PX) is the aromatic product in greatest demand. PX is the first link in a manufacturing chain leading to polyethylene terephthalate (PET), whose global market growth is a strong 6%/y, owing particularly to the considerable demand for plastic bottles and clothes containing synthetic polyester fibers. Benzene is used in a variety of well known products, including polystyrene, nylon and polycarbonate resins. The latter product is used in automobile glass, DVDs and optical lenses.
Bottle grade PET is in high demand, especially in Central Europe, Eastern Europe, Africa and China, where the demand is projected to grow at the highest rates, close to 7 - 9%/y. PX is the largest volume isomer of the mixed xylenes. Approximately 98% of PX demand comes from the polyester chain via one of its intermediates, purified terephthalic acid (PTA). According to UOP, the company is the world’s leading licensor of process technology for the production of aromatics. As of 2011, UOP had licensed 94 complexes and more than 500 individual process units for the production of aromatics, including more than 289 CCR Platforming processes. Axens is also a leading technology licensor for petrochemical intermediates, such as PX production. Other licensed aromatic processes have been developed, for instance, by Shell, Lurgi, Uhde and ExxonMobil.
There are many processes involved in producing aromatics. Benzene, toluene and xylenes are mainly produced by the catalytic reforming of naphtha using continuous catalyst regeneration technology, such as UOP’s CCR Platforming™ or Axens’s Aromizing™. Another source of aromatics is the pyrolysis gasoline (Pygas) produced by steam cracking naphtha. PX, one of most important xylene molecules, is used as a building block in the production of PET. The typical aromatics complex includes a combination of process units for the production and purification of PX. Many complexes also produce additional aromatic products like benzene and ortho xylene. The paraxylene separation process separates high purity PX from mixed C8 aromatics isomers. Aromatics extraction recovers high purity C6 – C9 aromatics from hydrocarbon mixtures, such as reformed petroleum naphtha, pyrolysis gasoline by extractive distillation. Aromatic treatment is used to reduce olefinic content in either a heavy reformate feed or an aromatic extract feed.
“Third generation valve diagnostics, such as Valve Manager™, give even non-specialist users a clear, immediate summary of the valve assembly’s status.”
Sari Aronen, Application Engineer
Challenges facing control
Valves in processing aromatic compounds Benzene, toluene and xylene and their mixtures are found to be extremely dry and remove any kind of grease or lubricant from metal or other surfaces. Aromatic compounds create friction to surfaces, like between the control valve plug and seat, which are in continuous movement against each other when controlling the flow. Sometimes, the control valves are also expected to be really tight (ANSI V) to avoid any leakages of these hazardous compounds and to eliminate the installation of an additional shut off valve to the piping. Pipeline purging in these kinds of conditions with heavy solvency should be taken seriously in order to avoid any impurities or debris in the piping.
Combining the challenges of frequent movement with many reversals, seating tightness and possible piping debris makes the application highly critical and demanding, and literally pushes it to the edge of optimum conditions for a control valve. There is a real risk that control valves can get stuck, and the wearing and scratching of seating surfaces may occur. This then leads to many kinds of control problems, such as hunting and poor control performance, as well as leaking. How can you make sure such problems do not occur? How can you ensure optimum control valve performance, reduce maintenance needs and assure good process performance with such demanding flow media? Here are some different option suggestions for selecting the control valve type and materials.
Eccentric rotary plug valves
Eccentricity minimises the friction in control duty, because there is no seat friction during the control operation. In addition, it minimises the risk of valve failures in challenging applications, where high cycling or aggressive flow media is present. Therefore, it is an optimum solution in an application like dry aromatic solvents.
Ball valves
Ball valves typically have a wide range of solutions for all applications. Ball valves are designed even for the most demanding conditions. Base materials and a wide variety of coatings can usually be tailor made to meet specific process requirements, which will extend operational life and minimise maintenance needs. Challenging applications often require special materials and know how, especially when using a centric valve like the segment or ball valve. A correctly selected ball valve offers a long lasting, durable solution with high capacity and sizes available from small to larger sizes.
Triple eccentric disc valves
As the name implies, the triple eccentric disc valve has an eccentric design. Similar to the eccentric plug design, there is no contact between the disc and the seat, and therefore the seat friction is minimised during operation. This ensures optimum performance and minimum wearing in control duty. A high performance triple eccentric disc valve is an economical solution for large sized control applications with moderate pressures. The standard construction is well suited especially for dry, aromatic solvents, where there are material/coating limitations due to the flow media.
Control valve diagnostics
A process plant typically makes numerous measurements of process related activity, including temperature, pressure and flow. However, these measurements relate to the process itself and are not always directly linked to the performance, status and condition of the valve.
The main way of accessing this vital information about the valve is via the valve controller. The diagnostics available through intelligent valve controllers are based on measurements carried out by the positioner itself. Leading valve controller manufacturers have recently focused on ways to help operators quickly determine the status of valve assemblies, regardless of whether they have in depth training in valve diagnostics. Third generation valve diagnostics, such as Neles Valve Manager™ gives even non-specialist users a clear, immediate summary of the valve assembly’s status. It graphically displays indexes of the valve, actuator and positioner, as well as indexes of control performance and the application environment. Index calculations can be modified according to the specific needs of users. For example, increased friction is shown as a decrease in the index. Likewise, the actuator index summarises the use history of the actuator and combines this with measurements reflecting the friction and possible pneumatic leakages in the actuator. Intelligent digital valve controllers are capable of delivering a range of process related information about the condition of a valve assembly. Recent developments emphasise more intuitive user interfaces as well as data and diagnostics that are available in real time. This trend is sometimes referred to as ‘the third generation’. The enhanced clarity and timeliness result in more correct maintenance decisions being routinely made, which in turn, can lead to significant cost savings.
Emission control
Petroleum hydrocarbon products are complex mixtures of chemicals. Risk assessments for these products, in general, focus on specific toxic constituents. The petroleum constituents of primary interest to human health have been the aromatic hydrocarbons (i.e., benzene, ethylbenzene, toluene, and xylenes). Benzene increases the risk of cancer and other illnesses. In the US, the Occupational Safety and Health Administration (OSHA) requires that a mixture shall be assumed to present a carcinogenic hazard if it contains a component in concentrations of 0.1% or greater. The American Petroleum Institute (API) stated in 1948 that ‘it is generally considered that the only absolutely safe concentration for benzene is zero’. The US Department of Health and Human Services (DHHS) classifies benzene as a human carcinogen.
Valves with a low fugitive emission level benefit end users in many ways. First of all, valves that have a very low fugitive emission level, such as rotary design valves, help end users fulfill current environmental legislation rules, which are mandatory. Therefore, health and safety issues can be minimised by reducing fugitive emissions. A leaking valve packing may represent an enormous safety issue in a plant processing aromatic compounds. There are also cost savings that can be achieved by minimizing the fugitive emissions. The lost flow medium equals lost raw material, a smaller yield of the end product and lost energy, as the pumps/compressors must do extra work to compensate for the leakage.
Conclusions
For reliable and safe aromatics processing, the valve selection and sizing should be done carefully. There are many types of valves available in the market, which may be confusing. Once the basic parameters, such as size, pressure and temperature are set, another important decision has to be made with respect to the tightness and valve design. It is important to understand the design limitations of each valve type, and decide on the most important aspects for the particular application and plant. Intelligent digital valve controllers provide a means for online valve condition monitoring. They take necessary corrective actions and plan maintenance activities before anything shows up in the process. Emissions should hardly ever be compromised, as safety and environmental regulations get tighter all the time. It is good to keep in mind that emission certified rotary valves provide a reliable and safe way to meet this requirement.
Text by Sari Aronen
Published in Hydrocarbon Engineering December 2013 as 'Choosing valves'
Text originally published in 2013, and slightly updated in April 2022, due to the company name change to Valmet.
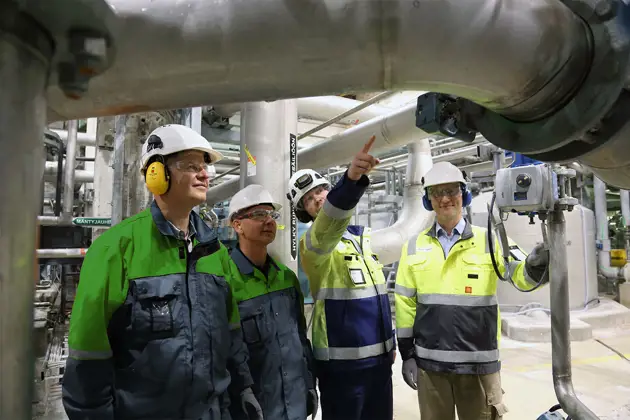
Subscribe to our newsletter
Subscribe now to our 'Go with the flow' newsletter and receive the latest insights directly to your email.
Subscribe