The advantages of mill-wide optimization
Jun 4, 2020
The development of the Industrial Internet in the direction of Artificial Intelligence (AI) and autonomous mills will enable mill-wide optimization of processes. Good examples of this and good results can already be seen in the energy industry, which has been taking concrete steps toward this target with centralized remote control rooms and daily heat network optimization.
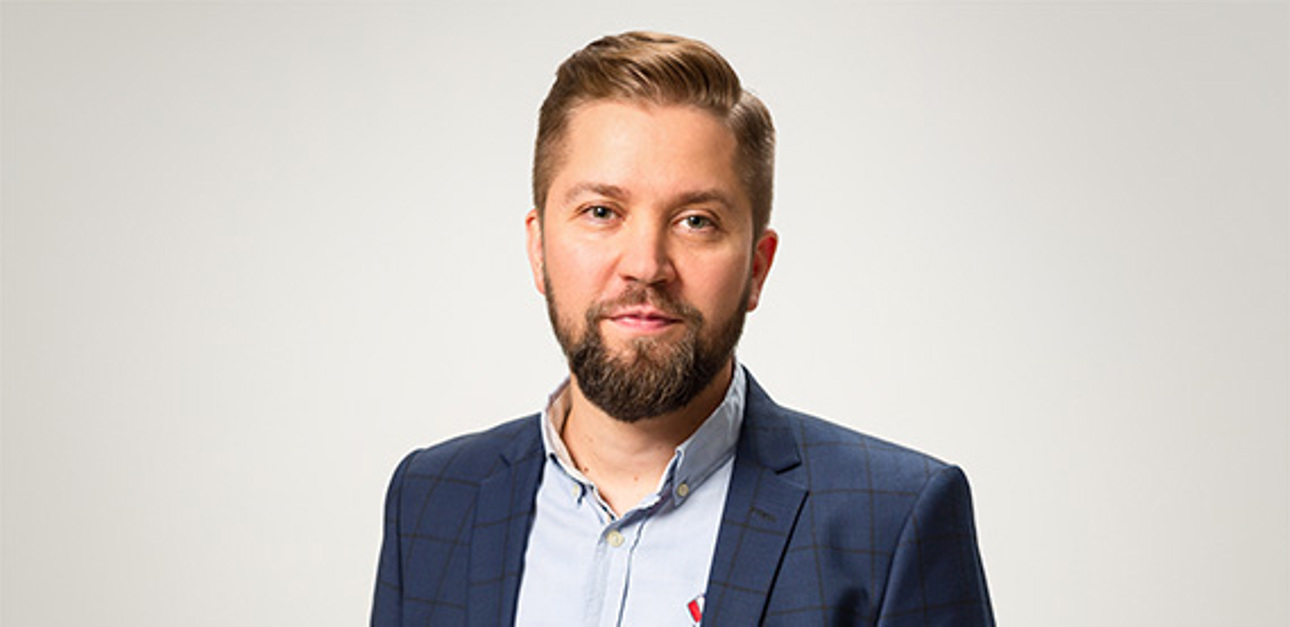
There are two main reasons why companies are interested in moving towards autonomous mills and mill-wide optimization. The first is to improve reliability and the second is to develop operational performance. In both areas, digitalization and the Industrial Internet are key elements.
“When we say ‘autonomous’ we mean machines or mills that can act independently without being controlled by humans,” says Samuli Lehtonen, Director, Operations Performance Optimization, Industrial Internet at Valmet.
“With autonomous systems you can achieve big improvements in reliability because, instead of being reactive, they can provide predictive and prescriptive information. They identify what needs done when, so that maintenance is planned and carried out well before any issues arise. This prevents unexpected downtime and it’s much more efficient and cost-effective than trouble-shooting after a problem has already happened.”
“On the operational performance side of things, we can develop autonomous machines that can learn how to optimize and run themselves. For example, you could have a pulp mill wash press that knows the optimal way to start up and can do it automatically, as well as being able to decide when it needs to change start-up sequences. The idea is that machines can optimize themselves at each step of the process and improve overall performance.”
For example, if you combine and optimize the control systems of a fiber line and paper machine you will get better results than if you optimize the lines individually.
Finding opportunities between processes
“A lot of these things can be done already, however they are done for individual machines or individual process islands. For example, in today’s pulp and paper mills, a lot of the planning and preparation is still done manually on a daily basis. The mill experts decide on the next day’s production rates and adjust things accordingly. This way of doing things makes it very difficult to achieve an overall optimum situation, and almost impossible to do the calculations. This is where Industrial Internet applications can clearly help.”
“At Valmet, we are working on coordinating processes as one big entity, so that production, quality and costs can be optimized from a mill-wide perspective. This lets you improve the profitability, efficiency and environmental impact of your whole mill. There is a big need for this approach in the pulp & paper industry, and there are many opportunities. However, it’s not yet well developed within the industry.”
“Mills are becoming aware that there’s big money and many opportunities between the processes. To clarify, when we say ‘between processes,’ we mean that even if a whole process is optimized, the data is not shared with any other processes in the chain. There’s a gap in the data, and therefore a gap in the control and automation. By eliminating these gaps we can work towards mill-wide improvements. For example, if you combine and optimize the control systems of a fiber line and paper machine you will get better results than if you optimize the lines individually,” says Lehtonen.
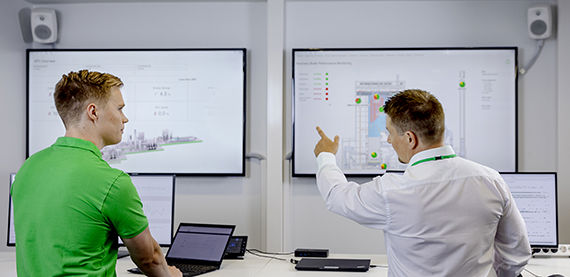
"Quite often the focus is on just one thing, like understanding bottlenecks, increasing production or finding ways to save costs on raw materials. With a mill-wide approach companies could see improvements in all these areas. And this is where we are going with digitalization and the Industrial Internet,” says Lehtonen.
Network-wide optimization in action
While there are no fully autonomous mills in the pulp and paper industry yet, other industries are already seeing positive results from large scale autonomous operations. For example, the energy industry has already been taking concrete steps toward autonomous plants by having centralized remote control rooms and heat network optimization as a part of their daily work.
“At Valmet, we supply energy management systems as part of our Industrial Internet solutions portfolio. These give you a good idea of what can be achieved by bringing different processes together and optimizing them on a network-wide basis,” says Lehtonen.
“One recent example is our solution for the energy company Helen, which optimizes their district heating production and network in the city of Helsinki, Finland. The solution coordinates and automates everything from individual pumps and network flow to managing the capacity of whole heating plants, and it also predicts things like delays and different intra-day variations to improve overall network efficiency.”
“We integrated the solution into Helen’s existing production planning and Valmet DNA automation systems, and other existing process control and information systems so that everything works smoothly together. It lets Helen see the big picture so they can make decisions about electricity trading and when to use the network for energy or heat storage. This network-wide approach has reduced their energy procurement costs and also helps them reduce their emissions.”
Another example is the Industrial Internet ecosystem partnership between Valmet and Fabio Perini, a company that specializes in the production of machinery, lines and integrated systems, for the converting and packaging of tissue paper. The two companies’ solid expertise combined with data from tissue mills and converting plants will provide a new dimension to tissue mill optimization. The collaboration aims at providing an unbroken chain of production data from the tissue machine to the converting line and utilizing artificial intelligence-driven applications in the tissue production process to make the converting operations downstream more efficient.
“We have developed ways to evaluate how much benefit a mill can expect to see from mill-wide optimization.
Identifying bigger benefits
“When we think about the pulp and paper industry and the kinds of benefits that companies are looking for, they usually want to increase the profitability of their mill without having to make big changes to their equipment. However, quite often the focus is on just one thing, like understanding bottlenecks, increasing production or finding ways to save costs on raw materials. With a mill-wide approach companies could see improvements in all these areas. And this is where we are going with digitalization and the Industrial Internet,” says Lehtonen.
“What we are really trying to do with the Industrial Internet solutions is to help our customers to overcome the challenges that they are facing at the moment and help them use their assets in the optimal way. These solutions make this possible, but customers need to be prepared to share data, process flow sheets and so on. Then we can identify pain points and possible use cases.”
“We have developed ways to evaluate how much benefit a mill can expect to see from mill-wide optimization. For example, a good method is to reoptimize the past. With this approach, we do data discovery to analyze a mill’s old data – at least a year’s worth – and then we calculate what the savings would have been for different optimization scenarios. Based on our experience and calculations, integrating and coordinating different process areas or islands can result in savings up to millions or tens of millions of euros.”
Making everything work together
“For mill-wide optimization to work, the main thing that is required is to have a coordination application for automatic decision making that can harness recent advancements in optimization technology. The application accounts for interactions between processes, storage levels and delays, process and quality constraints, and future shutdowns and slowdowns. Mill-wide optimization can be a stand-alone solution, but you will get the best outcome when it is combined with advanced process control systems (APCs) to execute the decisions. The automatic decisions and recommendations provided by the system are impossible to perform manually, providing a completely new and efficient way to improve overall profitability.
“Many companies are already exploring the potential benefits in their strategies and we have technology that lets us do many things. At the same time, we need to recognize that increasing automatization requires a change in customer processes and the way they work. Some level of change management will be required to help people get the most from the technology. In addition, we’re seeing that as the younger generation comes in, they want and expect better scheduling and planning tools. So in the future we predict that it will be easier for company-wide teams to work together remotely from different locations, and perhaps the core-competencies will be centralized. Either way, mill experts will still be needed, but they’ll have better tools and better information to do their job and to improve overall mill performance,” Lehtonen concludes.
Related content