High quality coated board production of ITC Limited BM 1 in India
Apr 16, 2019
ITC Limited invested in new high-class coated board-making technology to respond to the demand of India’s fast-growing paper and board consumption. The continued shared journey of the two companies stems from the high technology Valmet can offer combined with the long and trusting relationship between the companies.
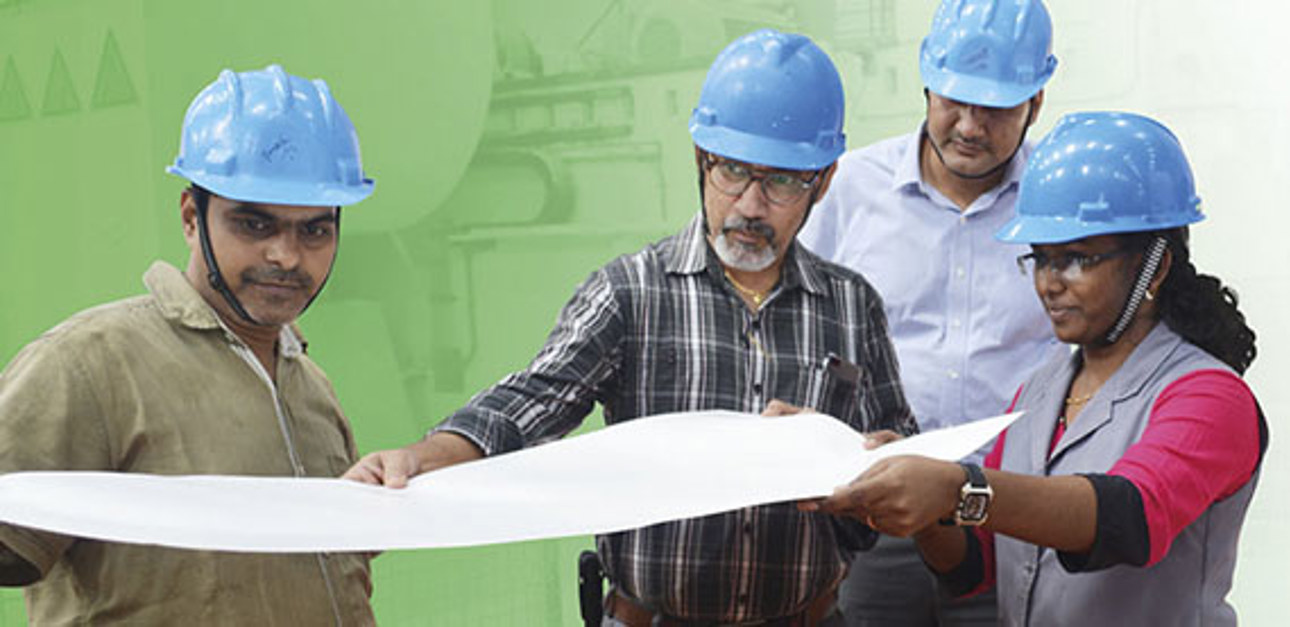
ITC’s site in Bhadrachalam is India’s largest integrated pulping and paperboard manufacturing unit. The unit produces high-end virgin and recycled board for packaging and graphic applications, as well as fine printing papers.
Consumption of paper and board is growing at over 6 per cent a year, and ITC wanted to improve their competitive situation in the market by selecting the latest technologies for manufacturing folding boxboard. After the latest investment in a board-making line from Valmet (BM 1), their folding boxboard capacity has increased remarkably.
“The main driver for this investment was the increasing demand for packaging board in India, mainly due to increased online shopping. Coated board also has an important role in replacing plastics. We needed a trustworthy equipment supplier and high technology that can convert raw material to high-quality board in a cost-effective way. We have a long history with Valmet, and we have seen many well-running, Valmet-supplied board machines. They can offer the best board-making technology and know-how that can make a difference,” comments Sanjay Singh, Chief Executive Officer of ITC’s Paperboards and Specialty Papers Division, about the newest investment of the company.
“Coated board has an important role in the future of packaging, for example in replacing plastics,” says Sanjay Singh, Chief Executive Officer of ITC’s Paperboards and Specialty Papers Division.
"We needed a trustworthy equipment supplier and high technology that can convert raw material to high-quality board in a cost-effective way."
From engineered solutions to measurable results
“We prefer global partners, like Valmet, who understand our requirements, and the market, and know us well as a company. We require excellent technology, and we need a good set of people both from ITC and Valmet. Together, we were able to commission a high-speed board machine and produce excellent board to achieve a superior position in the market today,” says Vadiraj Kulkarni, Chief Operating Officer of the Paperboards and Specialty Papers Division.
“Excellent-quality board means high printing properties, as well as good functional properties like high bulk, smoothness and stiffness. In addition, the cost dimension is essential in terms of lightweighting and energy-efficient processes. Valmet has been very committed to this project from engineering the solution to qualified end product quality,” he continues.
“We need a partner who understands us well and understands our requirements. One that does not only offer the machine, but an entire solution, and works with us as a partner to meet – and even exceed – the project targets,” says Vadiraj Kulkarni, Chief Operating Officer of Paperboards and Specialty Papers Division.
Optimal balance of scope, cost and time
The BM 1 coated board machine started up in June 2018. According to ITC’s Project Manager for BM 1, A. Harinarayanan, the start-up was smooth. “The challenges any project manager faces are related to scope, cost and time. I’m very happy about the support from Valmet: Together, we were able to stick with the original cost level, scope and time schedule. Within a couple of months from the machine start-up, we were able to achieve almost all designed end product properties and the designed production rate.”
Valmet’s delivery also included automation solutions for the production line. “With Valmet’s integrated automation solutions, the performance of BM 1 is better, the start-up was smooth and efficient, and stabilizing the process was fast. This has been the best installation of a board machine with the shortest possible time,” says Singh in summary.
ITC Limited’s BM 1 board machine produces high-quality folding boxboard grades at their Bhadrachalam site in India.
Right technology scope for sustainable production
ITC has been carbon-positive, water-positive and solid waste recycling-positive for several years. This drives ITC to constantly develop ways to be more efficient in their processes. “In addition to excellent board quality and high-speed production, we are looking for resource efficiency in order to be more competitive,” states Kulkarni. He continues: “For the first time in India, we are using innovations like Aqua cooling calendering technology, which will ensure better end product properties of the board while enabling us to reduce energy consumption.”
BM 1 consists of a multi-Fourdrinier wet end concept and a press section with a shoe press. It runs without an MG cylinder, which is uncommon in folding boxboard manufacture in India. “We are running the shoe press very efficiently. This has been beneficial in terms of board quality. The wet end overall is also very efficient. The formation is at a good level. With this wet end concept together with the press section, we can produce high-quality folding boxboard grades very cost-effectively,” says K. Nagahari, Senior Vice President of Projects at ITC Limited.
“We required board properties with as good printability as can be achieved with an MG cylinder. We believed in Valmet’s technology and know-how to be able to produce the same quality without it. We have sent out this end product to our customers for printing. The customers are very happy with the product quality,” states Singh.
“The high level of technology, knowledge and R&D capability from Valmet is very valuable for us to implement this project,” says K. Nagahari, Senior Vice President of Projects at ITC Limited.
Close collaboration
The shared journey of ITC and Valmet is almost two decades long. “We have had good collaboration together. There is deep engagement between us, and it has helped us to solve challenges also during this project. We share engagement at several levels: between the project teams, the optimization teams and the start-up teams,” says K. Nagahari.
"Valmet has been very committed to this project, from engineering the solution to qualified end product quality."
“We have had fluent communication with the Valmet team. From day one, ITC’s management and Valmet agreed to have a fixed review mechanism for this project. Once a quarter, we had a senior-level steering meeting, and we were able to review and fix any unsolved issues. At the end of the day I’m very happy that we have successfully commissioned this project by working together,” concludes A. Harinarayanan.
“ITC has a very robust system in place regarding, safety, environment and health issues. We have seen that Valmet has very high set of standards related to HSE. Working together has ensured that this project has progressed well and has ensured safety,” says A. Harinarayanan, Project Manager of BM 1 project from ITC.
TEXT: Marika Mattila
Related articles