When the going gets hot, Valmet Furnace Imaging gets going
Oct 4, 2019
GKN Hoeganaes Corporation, the world leader in the production of atomized steel and iron powders, installed a forerunner of the Valmet Furnace Imaging System, Fixed Mount Mid-IR infrared camera in the ladle metallurgy furnace (LMF) at its Hoeganaes plant in Gallatin, Tennessee.
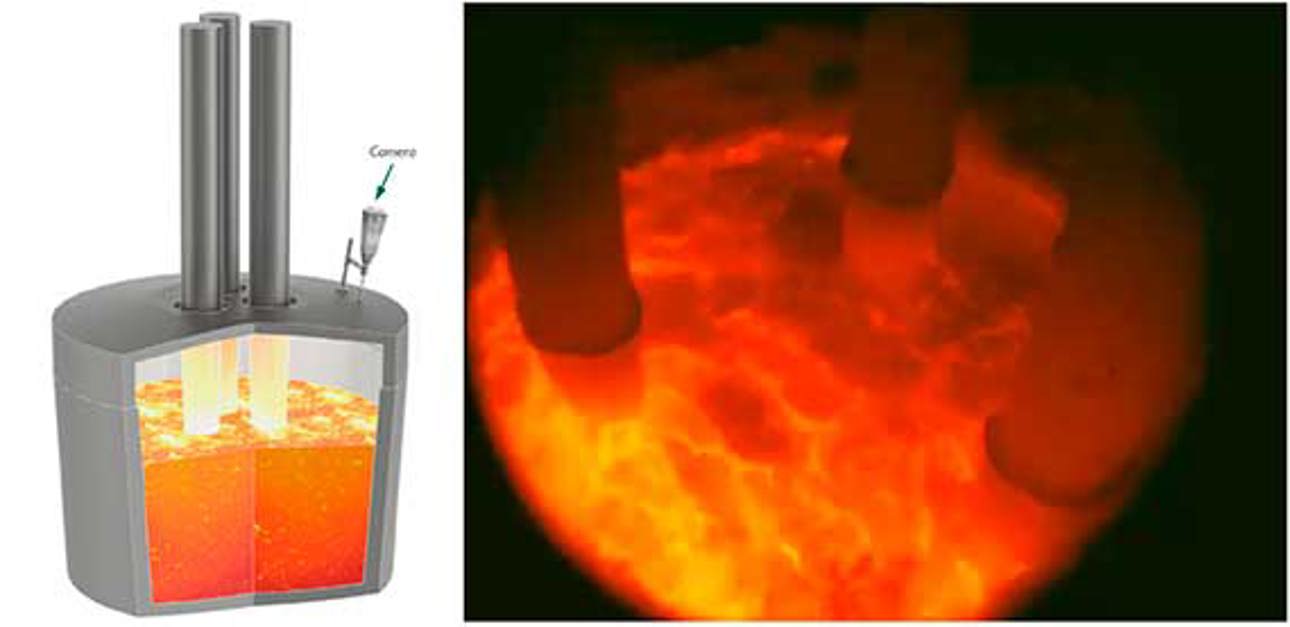
The Gallatin facility has a 70-ton electric arc furnace (EAF) with a ladle metallurgy furnace (LMF) and 12 annealing furnaces for a capacity in excess of 300,000 tons for more than 20 base grades. Designed to see through flue gas and fly ash and provide an internal view of furnace conditions while operating at full load, the infrared camera system now allows an unobstructed view of the entire LMF process. Operational expectations have been met with improvements in productivity, reduced refractory consumption, improved temperature and ladle alloying control as well as increased operator safety.
Designed for extreme environments
The rugged design of the Fixed Mount Mid-IR infrared camera utilizes a unique borescope-type lens coupled to the air-cooled imaging unit located outside of the furnace. Only the optics are exposed to the interior of the furnace with pneumatic purging providing protection from heat and debris that could potentially foul the lens.
The infrared camera operates within the mid-infrared spectrum that allows for a clear image during full load operation of the LMF, even during power on conditions. Images are unaffected by the intense UV produced by the arc, off-gassing of the process, flames produced by combusting gasses or steam generated by atmospheric conditions.
The main goal of installing the camera was to be able to see as much of the ladle as possible, particularly the gas stir “eye”. With this in mind, the camera was mounted on the water-cooled roof directly above the stir with the control room monitor conveniently positioned above the operator’s control screen. After a flawless startup, the camera had significant and immediate positive impacts on safety, productivity, and quality.
A new tool for the operator
Hoeganaes routinely processes 24 heats per day through the LMF facility. The operators have the responsibility of bringing the ladle into the furnace via transfer car. Once the ladle is in place, the operator then remotely engages air and argon to the ladle. Once engaged, the air and argon are activated. This is where the advantages of the camera are evident. Each ladle tends to stir differently and the camera gives a real-time view of what the gas stir is doing (Figure 1). Before the installation of the camera, the operator had to make sure they had a stir before powering on and would stop several times during the heat to confirm the size of the stir. Earlier they had several occasions where there is a good stir and then it goes away, or where there is a good stir and it steadily increases to the point that an electrode could break. The camera is now used to increase the stir before making alloy additions and then decrease the stir to finish out the heat. More importantly, it gives the operators a tool that provides additional confidence to perform their job. Operators agree that the IR camera is one of the most resourceful tools that they have at the LMF.
Figure 1: Typical views of the LMF in “full load” condition. Note the absence of blinding arc and detail of the stir eye area.
Safety improvements
The first and most important benefit of having the IR camera is safety, operators no longer have to directly observe the gas stir and slag characteristics. The camera was also a helpful tool for personnel when installing a remote media-coupling device, which couples itself to the ladle to provide air and argon without putting the operator in harm’s way. Once power is applied to the ladle and lime added, the operator can also tell if there is sufficient slag to cover the arc. The confirmation of burying the arc and proper stirring leads to reduced refractory wear by preventing hot spots at the top of the ladle and keeping slag cover on the ladle sidewalls. Prevention of a slag line breakout can easily save $7,500 in materials alone per incidence. Another safety benefit is the ability to see a water leak. In the IR camera view, water appears black (cold) compared to the brighter, hotter background and is easily seen (Figure 2). If electrode cooling sprays get out of adjustment, operators are able to tell immediately, accordingly making corrections and preventing reactions.
Figure 2: Examples of water (dark blobs) from electrode water cooling sprays on melt surface of LMF
Quality and savings
The IR camera also aids in maintaining the product quality. By constantly monitoring the size of the “eye” of the argon stir, operators can now make sure that they do not over stir and cause inclusions. They can also safely monitor conditions while stirring hard to reduce aluminum and sulfur levels.
An immense financial benefit has been the reduction of total elapsed time at the LMF by saving 3-5 minutes per heat. The reason is that the camera eliminates the wait period for confirmation of a stir before powering on and there is no need to stop during the heat to check on the stir. Running at full production, those 3-5 minutes can cost more than $600,000 a year in lost sales potential!
This article is abstracted from a technical presentation at AISTech 2014, held in Indianapolis, May 2014.