Valmet goes underground to help treat wastewater
Apr 18, 2017
The Kakolanmäki waste water treatment plant, jointly owned by 14 municipalities, has been operating in the southern Finnish city of Turku since the beginning of 2009. Surprisingly located close to the center of town this state of the art plant occupies four kilometers of underground caverns which involved the excavation of 490,000m3 of rock during construction. Since the plant is built underground it has a more constant and higher temperature than surface facilities, a distinct advantage for treatment conditions. It is able to process the wastewater from 300,000 people and various industrial sources in a way that considerably reduces the nutrient load on the Baltic Sea.
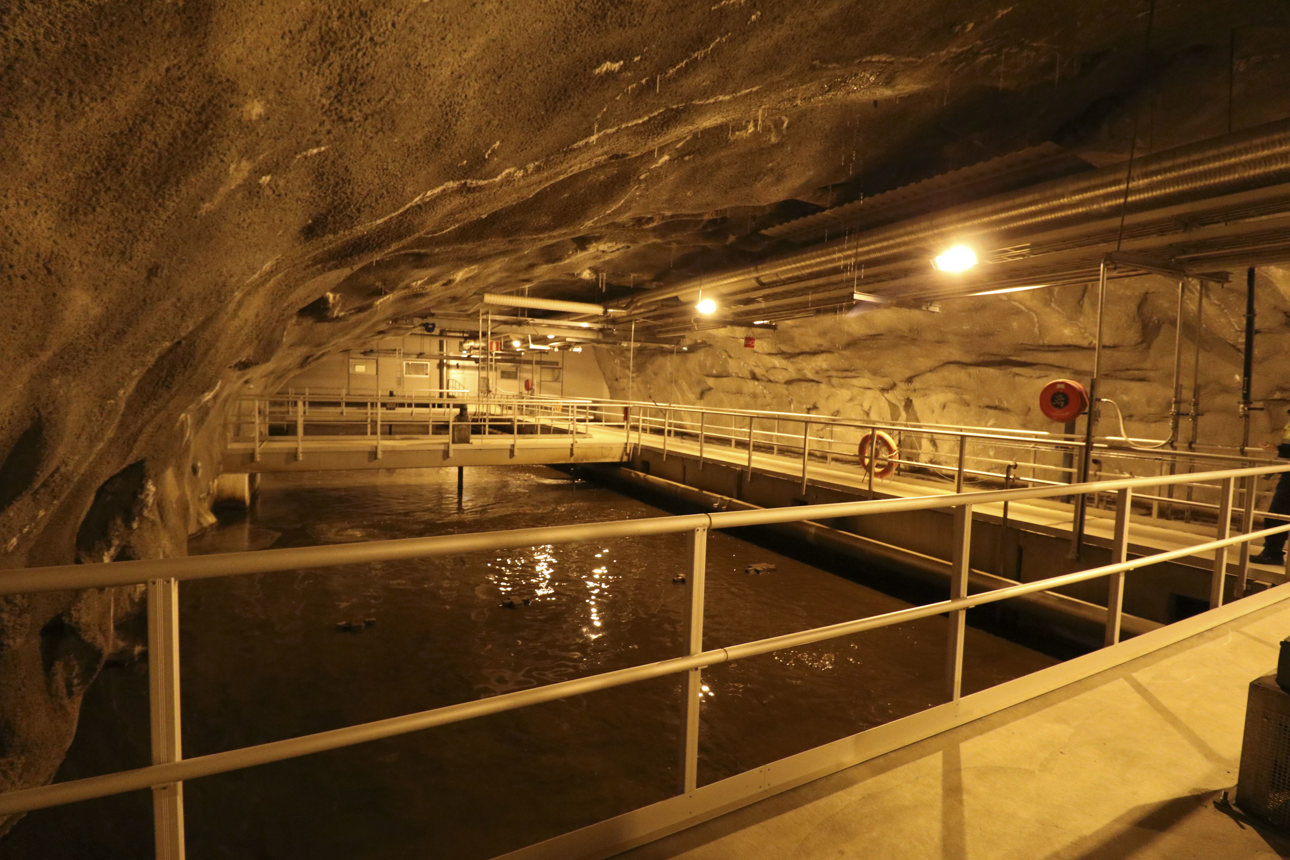
Sludge pumping control
An average of 80,000 cubic meters of wastewater a day is treated in a four line process that includes mechanical, chemical and biological processing. According to Jouko Tuomi, plant process engineer, an important part of running the plant more effectively is to employ more online measurements, “Online information is the basis of cost savings and optimization of the plant processes,” he states. “We already installed the first Valmet TS (Total Solids Measurement) in 2009 to monitor sludge from the four primary clarifiers and control pumping to the sludge storage tank. It enables us to stop pumping from the clarifiers when the sludge content drops below 3.5% and avoid diluting the sludge storage with excess water.” From the storage tank, the next stage of sludge treatment is centrifuge dewatering prior to the thickened sludge being trucked from the plant to the local Gasum biowaste treatment plant for further processing and the generation of biogas.
Valmet TS total solids measurements control polymer addition before the two centrifuges
Centrifuge optimization
The plant has two large centrifuges for sludge dewatering plus a smaller one which is used as needed. In 2015 we installed additional Valmet TS measurements before each of the large centrifuges to control polymer addition and thus stabilize centrifuge operating conditions. Centrifuge centrate is fed back to the beginning of the treatment process, which means any excess solids are inefficiently recirculated in the plant and reduce treatment capacity. In 2016 one of the centrifuges was also equipped with a Valmet LS (Low Solids) measurement to monitor the centrate solids content.
“It works really well and gives operators a continuous indication of how well the centrifuge is working and effectiveness of the polymer which is a great aid for optimization. Earlier we had to rely on 1 or 2 laboratory measurements per day and eyeball the situation. Now with polymer addition controlled and continuous centrate solids content information, control of the other centrifuge parameters, such as torque, is made much easier. The time consuming laboratory tests have been reduced to 3 times per week,” says Tuomi. “We are also able to trial different polymers and polymer qualities without loading the laboratory, while getting much more reliable information instantly.”
Jouko Tuomi, plant process engineer with the Valmet LS used to measure centrate solids
Meeting targets
For ease of transportation and successful post treatment the dewatered sludge solids content from the centrifuge needs to be 22% and in 2016, a Valmet DS (Dry Solids) measurement was installed on one of the two main centrifuges to monitor the resulting slurry solids content. An earlier model of the DS had been installed on the other centrifuge two years earlier and now with monitoring on both centrifuges, operators can be sure that the target of 22% solids content is met. The centrifuges are in use for about five days a week with dewatered sludge transported by road tanker to Gasum Oy's Topinoja biogas plant where it is digested and post-composted. The plant generates about 50,000 tons of dried sludge per year to produce biogas used to provide district heating and electricity after which the sludge is further treated in fertilizer production and utilized as a soil improver.
Valmet DS dry solids measurement in the downfall from the centrifuge continuously monitors sludge solids
Low maintenance
Tuomi has nothing but praise for the cooperation with Valmet personnel and quality of products, “They are skilled and all good types, smooth startups, first-rate training and always a fast response to questions. Maintenance needs have been minimal and although we recently entered into a service agreement with Valmet so far we have not required any exceptional assistance, but it is comforting to know that help is always at hand,” he says.
Operating in the sweet spot
The additional information provided by the Valmet measurements has proved to be a great aid to process optimization.
The four line Kakolanmäki waste water treatment plant
Source: http://www.turunseudunpuhdistamo.fi/tulopumppaus
Four kilometers of caverns excavated tens of meters underground
Source: http://www.turunseudunpuhdistamo.fi/tulopumppaus