Control system migration, one step at a time
Nov 29, 2017
When Iggesund’s Workington board mill in the U.K. decided to replace the coating kitchen control system, they turned to Valmet for a special solution. Rather than having a complete shutdown, replacing the end of life TDC3000 control system and starting up with the new, the mill intended a step by step approach that would not interrupt production.
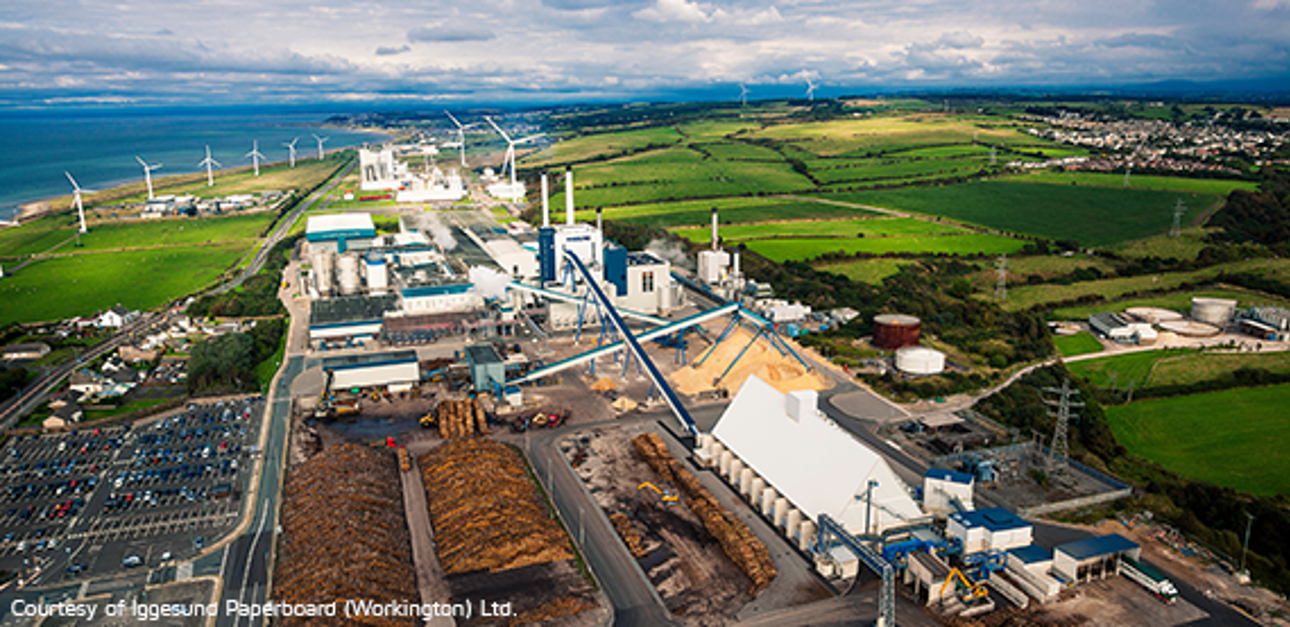
Andrew Hughes, Lead Project Engineer for the mill explains, “We had already done the migration of the water treatment plant two years earlier to Valmet DNA which had been successful and this was the next step on our migration roadmap. We had an intensive look into different suppliers as this was a substantial investment with impact to future plans. We also decided that downtime in the coating kitchen was unacceptable as it would also stop the board machine. The phased approach we were looking for met a lot of skepticism but the more we looked at it the more feasible it looked.”
The 60 day system migration
The batch process nature of the coating kitchen made it possible, by running certain grades for instance, to free up certain pieces of equipment and ultimately Hughes and his team came up with a plan to complete the migration in twenty-four steps with minimal interruption to production. "The plan called for the complete migration to occupy a 60 day window, migrating in stages which also allowed us to monitor each one and test it before changing over. With the big bang approach, taking maybe a two week shut, mill resources would have been stretched and any problems would have only been seen at startup."
For the phased approach a new rack room with cabinets for DNA was needed as both the old system and the new DNA would be running at the same time during the 60 days. The point of commonality to the two systems are tens of marshalling panels throughout the coating plant where signals are gathered together and passed to the rack room via trunk cables. This meant new trunk cables to each marshalling panel could then be connected as needed for each phase of the migration. "Not as simple as it sounds," continues Hughes, "as not all the cores of a particular trunk cable could be connected during the same phase, it required a lot of planning."
![]() |
![]() |
|
Andrew Hughes, Iggesund Lead Project Engineer | Hannes Martikainen, Consultant Automation Engineer |
Web based function descriptions
Hannes Martikainen, Consultant Automation Engineer, had a key role in planning. He spent several months reworking the functional descriptions of the whole coating plant. "The functional descriptions are web based and accessible from the DNA control system, so the operator can for instance pick a pump or valve and see what its function is, interlocks and other information with one right click, also likewise access the batch sequences shown graphically with flow charts," says Martikainen.
Remote factory acceptance testing
Not only satisfied with challenging Valmet over the phased migration, the mill also decided to perform a remote FAT (Factory Acceptance Test). Rather than sending production personnel to Finland to test the functionality of the system prior to delivery a room was set up at the mill with remote desktops and direct connection to Valmet’s factory in Tampere. Hannes Martikainen was on hand in Tampere to represent Iggesund and, with the help of Skype, it enabled mill personnel to take part in a very flexible way without the risk of shift shortages at the mill.
The remote six week FAT in June and July 2016 enabled all operators and technicians to take part and contributed greatly to them taking active ownership in the system. Each functional description could be checked and comments logged into the system for attention and finally marked as accepted. "At the end of the remote FAT we had only 8 faults out of 1,800 functions checked, a really great result," says Hughes.
![]() |
![]() |
According to Rob McMillan, Central Engineering Lead Engineer, "The hardware FAT was done, after the remote FAT, in Tampere and it went really well, a very slick operation. As well as the point to point I/O tests, an important part for me was to power off the system and then switch back on, it went well, DNA came up without problems." |
Smooth migration
Work in the coating kitchen area commenced with some 190 trunk cables to the marshalling panels being installed. With cabinets installed and the site acceptance test complete, the beginning of October saw the start of the 60 day window and the migration phase started with a starch cooker. Number one was to disconnect the old system points, reconnect the marshalling panels and then connect the DNA cabinets; altogether 2,200 I/O points were involved.
![]() |
![]() |
One of marshalling panels where signals are gathered together and routed to the rack room via trunk cables. |
"For each phase we built in time in case we had to revert back to the old system but we did not need to switch back at all, it was very smooth," says McMillan. "They are top notch people from Valmet, we were all one team and they bent over backwards to help."
Another part of the migration was to move the rather isolated coating kitchen operator stations to the mill’s main control room. During the 60 days a temporary DNA process station in the old control room enabled operators to look out for any problems while still operating the remaining processes. "All the preplanning paid off and we completed the migration on schedule, a few changes to the plan but everything came together and the support from Valmet was great," says Hughes.
Up and running
The new coating kitchen operator station is now in the main control room which improves communication and running of this vital mill process. System performance has met expectations and provided other gains to increase productivity. For instance, redesigned queuing logic on the batches now means as a mixer starts creating a coating batch, weighing product for the next batch is started which saves time and improves efficiency.
The two main coating mixers (picture below) each produce about 200 batches per month, with four storage tanks feeding the three coating stations on the machine. Additionally there is a starch mixer, sodium bicarbonate mixer and a fifth mixer for carboxymethyl cellulose (CMC) and Polyvinyl Alcohol (PVOH) preparation.
Data stored in one uniform solution
As with any modern process plant, the coating kitchen is the source of a vast amount of real-time data that has to be stored and processed efficiently for later analysis. Valmet DNA Historian solves this by combining process interfaces, calculations and databases into one uniform solution. One of the DNA Historian functions, dubbed the "Time Machine" by mill personnel, enables the replay of the operator’s screen to look at past events and identify actions and process responses when things don’t go quite right. It’s seen as a great teaching tool and helps identify problems for instance when pumps don’t start as they should or other problems arise. All process history, including trends and alarms, are stored automatically – a solid foundation for troubleshooting and process performance development.
Gray displays mean all is well
A special feature of this delivery by Valmet is the choice of gray scale displays. All the colors have been stripped from the graphics, common in hazardous industry control systems, so that when everything is alright the screen is shades of gray. "If you walk past a screen and everything is gray, it’s running. Any colors then alert you to an abnormal situation. Different levels of gray still show whether a pump is running or not, whether a valve is open or closed but a color will appear when its status is not as is should be. It works well," says Hughes.
Minimized risk and downtime
![]() |
![]() |
For Ulf Lofgren, Mill Director, system migration is a necessary evil, “To migrate from one DCS to another, it costs money, benefits are smallish but the risks are potentially big,” he says. “But of course it’s something you have to do, when you get to a point where the system you have is beyond repair and you just have to jump. The approach we took minimized the risk and downtime. The operators also had a long time to get used to DNA while taking part in the development of it, the screens they use and how they wanted it to work.” |
“This was really phase 3 of our migration, we already installed Valmet DNA in our power plant in 2013, phase two was DNA for the effluent treatment plant which was relatively low risk for us. So with the coating kitchen we were moving up in significance and risk, here was fierce completion but in the end we went with Valmet and that was a good decision. There have been some improvements with better control but we did not really anticipate them, so they have come almost as nice side benefits,” says Lofgren. “Flexibility from both our side and from Valmet really helped the whole project.”
About Workington board mill
Manufacturing folding box board (FBB) is a technically advanced process. Incada, the paperboard produced at Iggesund Paperboard’s Workington Mill, is of the highest quality and holds a prominent position in the market. Continuous development and adaptation to customer needs and expectations are essential for success in a highly competitive market. Since 2013, the Workington integrated pulp and paperboard mill has been powered entirely by fossil carbon-free bioenergy. Bleached mechanical pulp is processed to suit the special demands of paperboard manufacture and is combined with purchased bleached chemical pulp into a multi-layered board construction which is ideally suited to the demands of modern paperboard packaging.