New opportunities with OptiSizer Hard
Improving board properties further
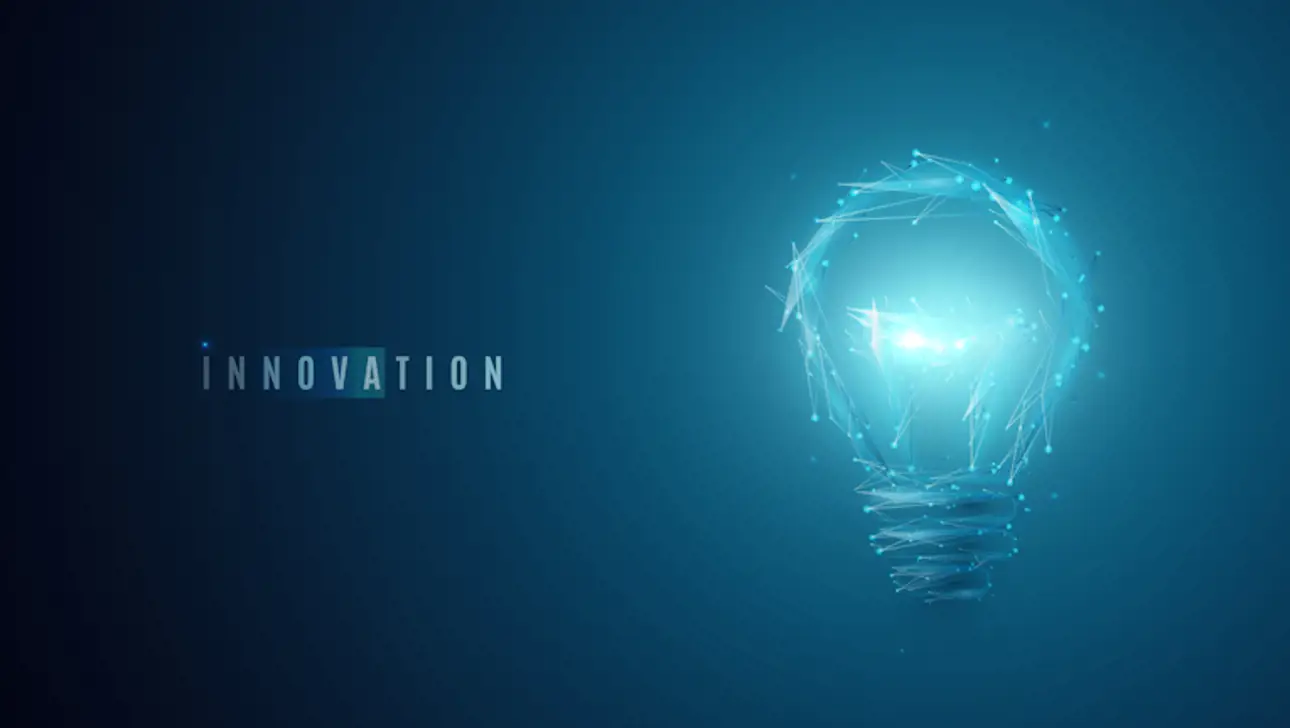
The R&D work did not stop after the first OptiSizer Hard was started-up. It was seen as a good place to improve further. There have been a number of pilot trials and the results with a new application method and a new concept combining OptiSizer Hard and OptiCalender Metal Belt seem to be clear.
Spray application on roll
Just recently launched version of OptiSizer Hard uses "spray on roll" application method. It means the starch is sprayed on the nip rolls which transfer the starch into the nip where it is further transferred into paper web. The new application method under investigation is almost the same, but instead of spraying, the starch is applied as a curtain. The curtain application beam forms a curtain of starch, which is a new innovative method in surface sizing. This application method gives totally new operating window for sizing compared to pond, film or spray application as seen in Figure 1.
Figure 1. Operation window of sizing with curtain application (curtain sizing). Size can be only starch or combination of starch and other components, like hydrophobic size, pigments and dyes.
Figure 2. Principle picture, how curtain sizing and metal belt pre-calendering can be utilized in coated board making process
Cartonboards with enhanced properties
The new opportunities in size composition with curtain application make it possible to produce coated cartonboards with enhanced properties. The optimized balance between size coverage and size penetration into board can be adjusted by size rheology. For example, starch with extremely high solids contents and viscosities can be applied to improve performance in board stiffness and pre-coating coverage. Very good surface strengths are reached, which might lead into a possibility to reduce coating color binders. Reduction of wetting and increased pressure in the nip also reduce or eliminate the unwanted roughening effect of sizing.
Mixing new materials in size
With no risk of plugging rods, it is also possible to mix new materials in size. With curtain application, there is also no recirculation of starch back from the sizing unit. They make it possible to mix cross-linking agents or similar strength-promoting agents in the size press infeed and have them react immediately after application. In conventional circulation, this type of mixing would most likely cause problems in screening, pumping and applicators in the form of crystallized deposits. Such possibilities include, for example, mixing highly refined fibers, micro or even nano-scale fibrillated cellulose to sizing process. These materials promote the possibilities to form good base for producing barrier-type properties for water, grease or different gaseous contaminants. Of course chemicals and pigments, which are already now used in the sizing can be also applied with curtain sizing process. These chemicals can be for example hydrophobic sizing agents, color dyes, waxes, etc.
The new process has already been demonstrated repeatedly in the Valmet Paper Technology Center pilot trials. High gains in board stiffness have been reached with starch application. High starch solid contents (20-40%) give possibilities to improved runnability of size press (less wetting of sheet) and savings in drying energy.
Combining sizing with long nip metal belt calendering
When the new sizing process is combined with long nip metal belt calendering, the stiffening effect is further improved. This combined process has potential for a completely new performance level of coated boards. The high amount of heat transferred in the calendering process is enough to re-activate the already dried starch in the sheet and further improve the stiffness by improving the bridging of the fiber network. At the same time, the topography and smoothness of the sheet are improved significantly.
When curtain sizing with high solids size (20 – 30%) is used for coated board and pre-calendered with metal belt calendering (OptiCalender Metal Belt) prior coating sections, the results are quite interesting as seen in Figure 2. The pilot trial shows, that it is possible to increase coated board stiffness 15 – 30 % with same PPS s10 roughness level. This make it possible to remarkable fiber saving. Another option is to improve smoothness, if stiffness level is already on target level.
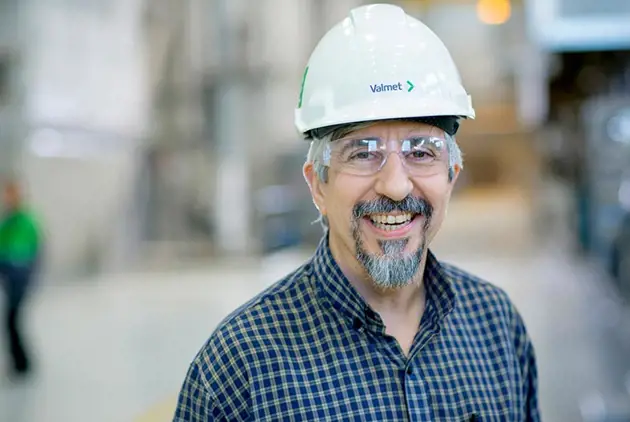
Interested in pilot trials?
We offer the opportunity to experiment and develop paper and board products and processes without having to put your own production on hold. Follow the activities in the trials on site or remotely through live streaming cameras. Pilot trials are very cost-efficient compared to expensive tests in paper and board maker's own production.
Contact our pilot trial experts