Up for the challenges of cellulosic ethanol production
Jul 27, 2018
Pretreatment is one of the most critical and challenging areas in the cellulosic ethanol production process. Valmet’s BioTrac system, part of the front end in a biorefinery and used for prehydrolysis, contributes to both the quality and quantity of the ethanol produced.
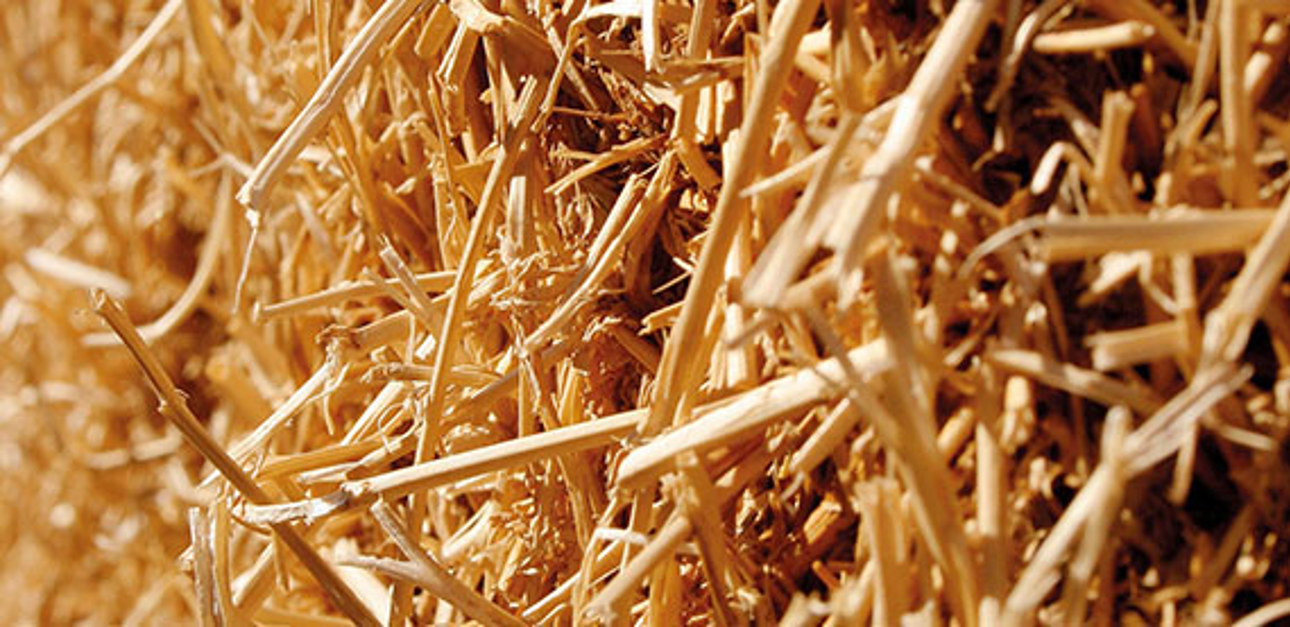
Pretreatment makes the cellulose accessible in the following biotechnological stage by transforming the material, both physically and chemically. With a process solution designed for a specific raw material, the pretreatment stage can be very efficient, increase yield, and maximize the amount of ethanol produced. Equipment plays a critical part in the pretreatment area and is vital in achieving a fully implemented process solution.
Achieving balance in pretreatment
There are several challenges in the pretreatment area, and most plants have experienced them. They include feeding bulky, heterogeneous material into the system, together with contaminants such as silica and sand, which can lead to wear problems. Bulky material is difficult to handle when feeding into a high-pressure reactor: The material must act as a steam-tight plug, to minimize blowback, but at the same time the energy input must be minimized to reduce wear on the feeding system. To achieve this balance, Valmet has a very flexible system to optimize the feeding of bulky material.
Other challenges include the physical behavior of the material as it passes through the system, and then discharging it.
“You need to manage all these challenges, otherwise you will get unnecessary sugar losses and formation of inhibitors, which will affect the subsequent process steps. It will also be a problem to obtain consistent production. Raw material in the cellulosic ethanol process is more challenging than in traditional biomass-based industries, with feeding and wear being the two main challenges,” says Francois Lambert, Manager of Biofuels Technology at Valmet.
Patrik Pettersson, Process Engineer, and Francois Lambert, Manager of Biofuels Technology, from Valmet. | ![]() |
High availability with BioTrac
Based on knowledge gained in the non-wood pulping and panelboard industry, Valmet has managed to minimize wear on the discharge line and has successfully developed a solution to feed non-wood materials under high pressure in a safe way. When dealing with high temperatures and high pressure, it is extremely important to reduce risks in order to improve safety. In the BioTrac system, the biomass is pre-compressed to accomplish a steady feed into the reactor while improving safety and providing high availability.
The BioTrac system for prehydrolysis of biomass is flexible in terms of both raw material and process. It can easily be adapted to downstream process steps. The layout of the system varies according to the application, but it often consists of either one or two reactors, although more may be used if required. The patented feeding system combines a force-feed screw and a plug screw feeder. Valmet’s impregnation system has been developed to achieve even impregnation in a very short time and to prevent chemicals from remaining on the surface of the material.
“Basic research has been going on for many years, creating a knowledge bank that covers different raw materials and their behavior. We have been building pilot and demonstration plants since the 1990s, which we have used to further develop our knowledge about non-wood together with our customers and partners. Continuously serving and supporting our customers, we have followed them in their successes and transferred knowledge acquired from those plants into our full-scope offering,” says Patrik Pettersson, Process Engineer at Valmet.
Proven, safe equipment
Valmet’s technology originates from the traditional pulp, paper and fiberboard industries – where Valmet has extensive experience – and has been further developed to meet the new challenges of biorefining. Valmet’s extensive experience in non-wood pulping and feeding of non-wood materials has been highly valuable when applying this technology in the pretreatment stage. Non-wood materials are not a homogeneous category, and each material needs to be assessed separately to get the right feeding solution.
In the bioethanol industry, the main focus has been on the downstream stages of the cellulosic ethanol production process, so the design of the equipment has not received as much attention. To better utilize the valuable raw material and prepare the material for further processing, the pretreatment stage needs to be reviewed. Proven, safe equipment is vital to meet the challenges and increase production of cellulosic ethanol. Valmet is a reliable partner and up for the challenges of cellulosic ethanol production, from pilot plants to full-scale production.
Bulky materials are challenging to feed, but the BioTrac system can handle it.