A replacement for fossil coal in power plants: black pellets
Oct 24, 2017
Steam exploded black pellets are a renewable biomass fuel that is safer and more cost-effective than conventional “white” biomass pellets, yet deliver more energy. The Valmet black pellet plant is a complete production facility with an integrated CHP plant, from biomass infeed to black pellet outfeed. Valmet also offers revamps of existing white pellet plants.
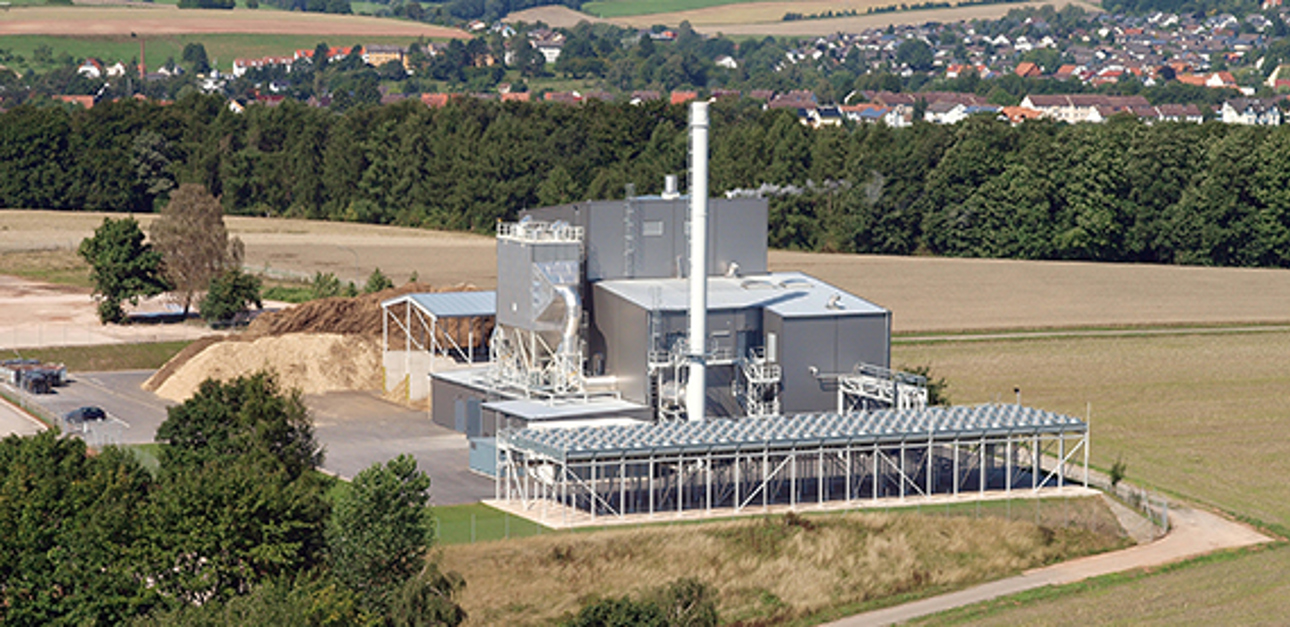
Large amounts of renewable woody biomass feedstock are widely available across the globe at competitive prices. However, transporting this biomass feedstock to its final users is often inefficient, largely due to its high moisture content. Steam treatment of the woody biomass followed by rapid depressurization solves this problem, creating a low-moisture material that is perfect for producing durable, water-resistant pellets or briquettes. Such pellets are excellent for safe, long-distance transportation, allowing power companies to take advantage of the global abundance of raw biomass.
The steam explosion process
Valmet’s black pellets are produced through a process of “steam explosion,” in which the woody biomass feedstock is treated with steam, then rapidly depressurized. After pelletizing, the material can be ground into a powder suitable for burning in large-scale power boilers or other systems suitable for pellets.
“The material is dried before it goes into the steam explosion process,” explains Mattias Erixon, Manager, Sales at Valmet. The plant feeds the biomass from a buffer bin into a pressurized reactor using plug screw technology. “The only thing added to the process is steam, and keeping the biomass for a certain period of time in the reactor.”
“The system discharges material from the reactor in a continuous infeed/outfeed loop,” Erixon continues. “As the material leaves the reactor, it passes through a blow valve into a blow line, connecting and then feeding material into the pelletizing step. The disintegration of biomass happens as it discharges from the reactor system when it goes from high to low pressure. A combination of friction in discharge and steam explosion happens when the pressure changes from high to atmospheric, causing the material to disintegrate.”
The biomass material enters the system with a particle size equivalent to normal or micro-sized wood chips, but comes out as small particles, almost a powder. This means that, unlike torrefied black pellets, which require additional densification, there is no need for further treatment between steam explosion and pelletizing. “With a normal white pellet product, you always need to reduce the size before pelletizing,” Erixon says, “but this is taken care of by the steam explosion process.”
Integrated CHP system
The black pellet plant can be integrated with a packaged combined heat and power (CHP) system that provides the steam for the drying process as well as power for the plant, and often surplus power to sell to the grid.
“How attractive this is depends on feed-in tariffs,” Erixon notes. “If you only want to provide the steam for the process, there are cheaper solutions, but in some cases, integrating a CHP and black pellet plant can be very attractive in terms of overall feasibility. You can have anything that produces steam for the steam explosion process and energy for the drying process. CHP plants are highly modular, being based on well-proven, standardized components that can be delivered and installed quickly. The plants are also highly automated, enabling unmanned 24/7 operation.”
To run the CHP plant, waste is recommended as fuel. Erixon explains: “We wouldn’t go through the process of making black pellets just to burn them at the same site. Our thinking would be that, instead of going through the process of making a product with a high energy value and certain properties, we would normally suggest using low-grade fuel, for example bark from the debarking process. Wet fuel is available as residue from the process and what you can buy on the market.”
A promising choice
The single most important factor in the pellet fuel value chain is the cost of the raw material – access to abundant low-cost raw material will greatly improve the economics of a pellet project. The steam explosion process creates an opportunity for upgrading low-grade, low-cost materials into a premium product. One such raw material is bark from kraft pulping. A modern kraft pulp mill is very efficient and may not need all its bark for internal use. Surplus bark can then be upgraded into pellets to be sold on the market as a bulk product for industrial use. Of course, bark from other wood processing industries like sawmills can be used as well. “Valmet’s pilot unit in Sundsvall produced black pellets from bark in order to verify the product quality parameters. The pilot runs confirmed the suitability of softwood bark for production of black pellets, which soon may offer a promising choice for the heat and power industries,” says Peter Björklund, Senior Process Engineer at Valmet.
Proven technology
Erixon says the design of the black pellet plant minimizes the risks inherent in any new technology by using standard, proven technologies wherever possible. For an example, he cites the use of a debarking chipper and a chip screening and storage system, “products we’re using in all of our other offerings to pulp, paper and energy customers. The next step is the belt dryer, also a proven concept that there are many references for. The steam explosion island is new technology, but we are basing that on experience and deliveries to other applications. So we have a huge amount of information that has a history in commercial-sized systems, and that we have verified in two pilot systems. A client interested in investing in a black pellet plant can rely on Valmet’s proven technology.”
“Black pellets contain and retain more energy than white pellets. They grind and burn more like coal,” says Sales Manager Mattias Erixon.