Valmet Manual Dewiring Station
Safe conveyors for manual dewiring
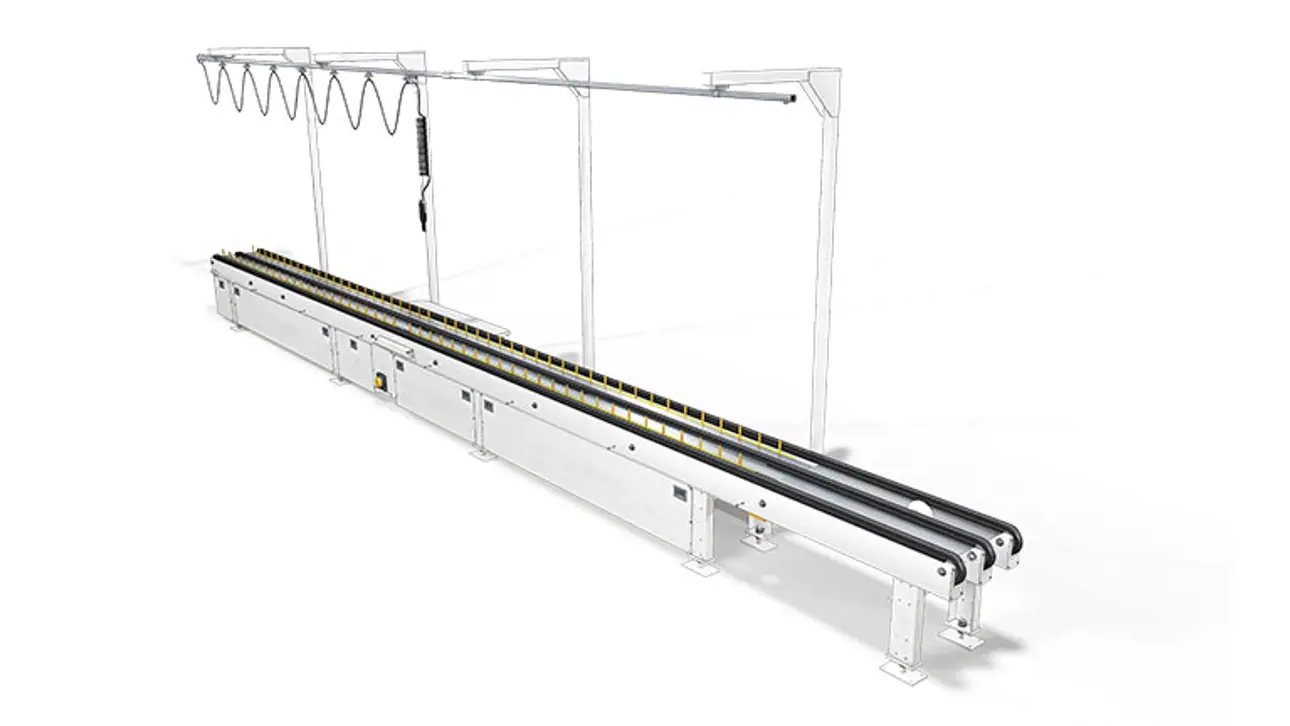
Valmet offers safe and efficient dewiring stations for single bales, functioning either as reject bale conveyors or to provide manual dewiring in lines serving continuous or batch pulpers
Maximum safety
Dewiring stations for all needs
Safe dewiring for batch and continuous pulping
Specialised dewiring solutions
Our Manual dewiring stations MDB (Manual Dewiring Batch) and MDC (Manual Dewiring Continuous) cover all your manual dewiring needs for pulp receiving lines.
Efficient bale reject conveyor
Bales that trigger the metal detector after automatic dewiring are diverted to a bale reject conveyor for manual dewiring. An MDB-L conveyor is ideal for this task, providing efficient and safe handling conditions for inspection and dewiring.
Safe dewiring for batch pulping
The MDB-H conveyor consists of a heavy duty conveyor, a pneumatic bale lift and a manual cutting tool for steel wire attached to an overhead guide rail system. The conveyor uses 50 mm chains and is commonly used in Manual dewiring stations on lines serving batch pulpers. The chain return parts on the conveyor are behind fixed protection to ensure highest possible safety. The conveyor is furthermore equipped with a rope pull safety switch is present along the conveyor beam on the operator side in order to further increase the safety for the operators. The MDB-H conveyor is equipped with a separate bale loading zone. The conveyors can also be furnished with a work platform and an integrated forklift protection and bale guard, as well as visual and auditory signals, to further improve the ergonomics and safety for the operators.
Safe handling of cut wire
Wire compaction is an integral part of a complete, optimised Manual dewiring station. Valmet Wire Winder, a safe and easy-to-use compacting machine for wire from bales and bale units, ensures smooth, efficient handling of wire collected at Manual dewiring stations. The wire is manually loaded into the machine, which produces wire coils with a width of 500 mm and
maximum weight of 150 kg. The finished coil can easily be picked up by a fork-lift truck for onward transport.
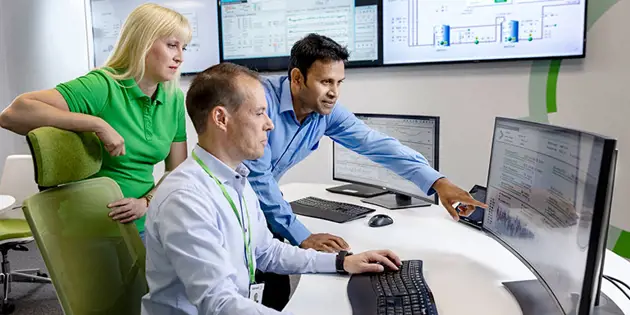
Our expertise is at your service
We at Valmet are committed to moving our customers performance forward and ensure smooth, disruption-free operation while respecting and protecting your most valuable resource.
Contact us