Dewatering elements for pulp drying
Valmet Dewatering Elements fulfill all the requirements set for dewatering at your pulp drying line
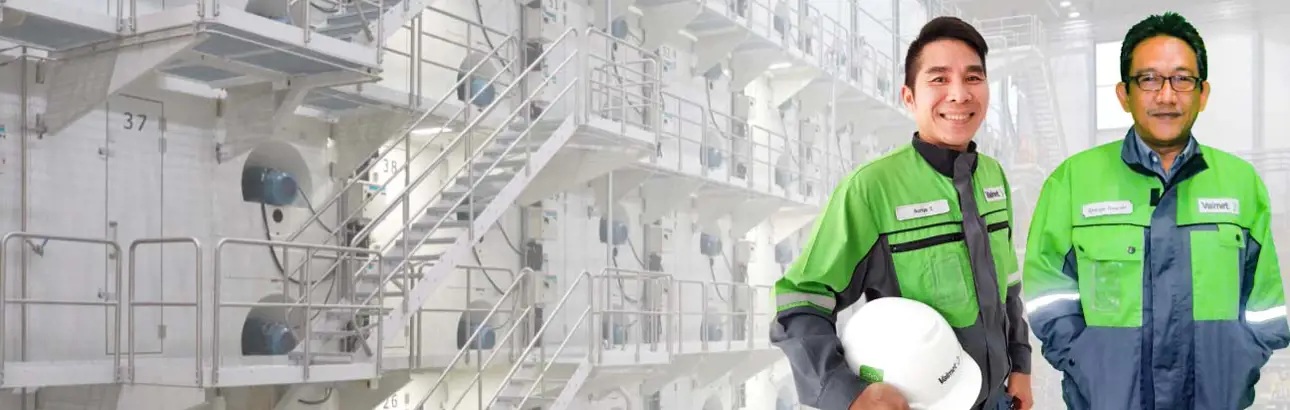
The most typical challenges with dewatering elements are related to efficiency of dewatering process, paper quality properties like formation, lifetime of dewatering ceramics, and performance of forming and press section fabrics. Whatever your challenge is, Valmet provides a comprehensive range of polyethylene and ceramic dewatering elements to your specific needs. Valmet Dewatering Elements suit all positions and OEM machine configurations and our expertise services are available close to you, all around the world.
Wear resistant materials for long lifetime
Low friction and gentle materials for paper machine clothing
High quality finishing due to low surface roughness
Easy and safe installation
Let us be your co-driver for success
Valmet solutions that combine parts and expert support will drive your production performances further. When you choose Valmet performance parts you are not just buying wear parts. You are also gaining greater availability, higher end-product quality and enhanced productivity.
With the combination of parts and expertise, we can together make a difference at every stage of your production process. We have increased production output and decreased total costs together by applying optimal performance parts to each position.
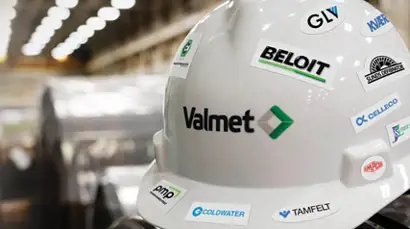
Further strengthening OEM expertise
Acquiring Coldwater has enabled us to expand our dewatering services offering through more expertise on dewatering elements and further strengthened product portfolio.
Read more about our OEM partnerships.
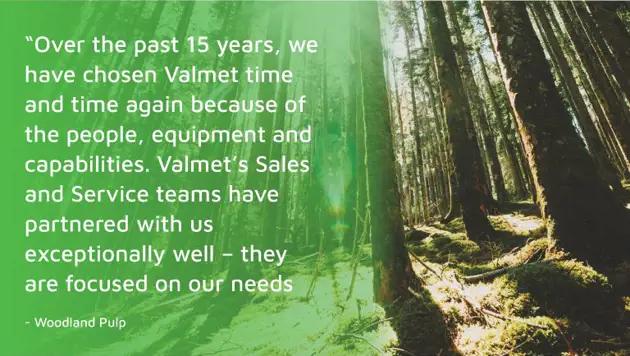
From full shift to 30 minutes
Are you looking to increase productivity and additional dewatering capacity? If so, we're excited to share how our experts helped a mill go from taking a full shift to replace table blades to now taking only 30 minutes!
Carefully selected materials for the longest lifetime and quality
Our carefully selected materials are used in different applications for different purposes. For example, we finalize our ceramics to very low surface roughness to make sure that fabric wear and power consumption is minimal.
Valmet is now able to supply complete offering of high-quality dewatering ceramics and two different types of polyethylene foils and covers. This means that you have access to complete through one source.
Typical application/ Machine concept |
Ceramic material |
Lifetime |
Surface quality (Low power consumption, |
Investment cost |
|
Premium Aluminum Oxide | ![]() |
![]() |
![]() |
|
Premium Silicon Carbide | ![]() |
![]() |
![]() |
|
Silicon Nitride | ![]() |
![]() |
![]() |
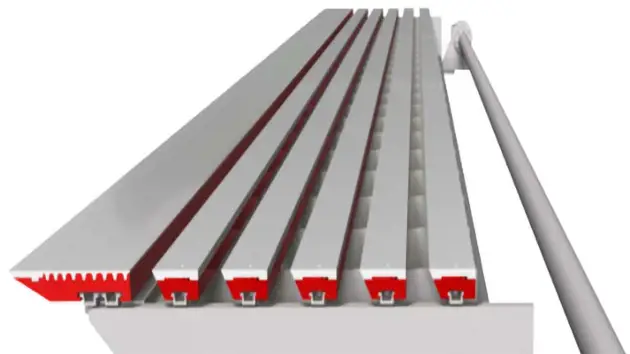
Dewatering Element Ceramic
- Wear resistant materials offer long and trouble-free operation and optimized dewatering
- Short delivery times
- Grinding and repairing service available
Dewatering Element Poly 1000 - 8000
Our polyethylene materials are formulated and
developed to deliver optimum performance across a
wide range of operating conditions
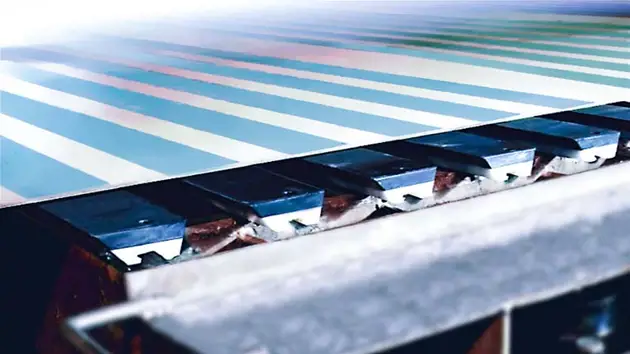
Related pages
