Focus on fugitive emissions
Dec 9, 2019
Eliminating fugitive emissions is a matter of both safety and sustainability. These are topics that we take very seriously. In addition to delivering process performance, we want to manufacture valve solutions that minimize fugitive emissions and help monitor, measure and report leakages more accurately than ever before.
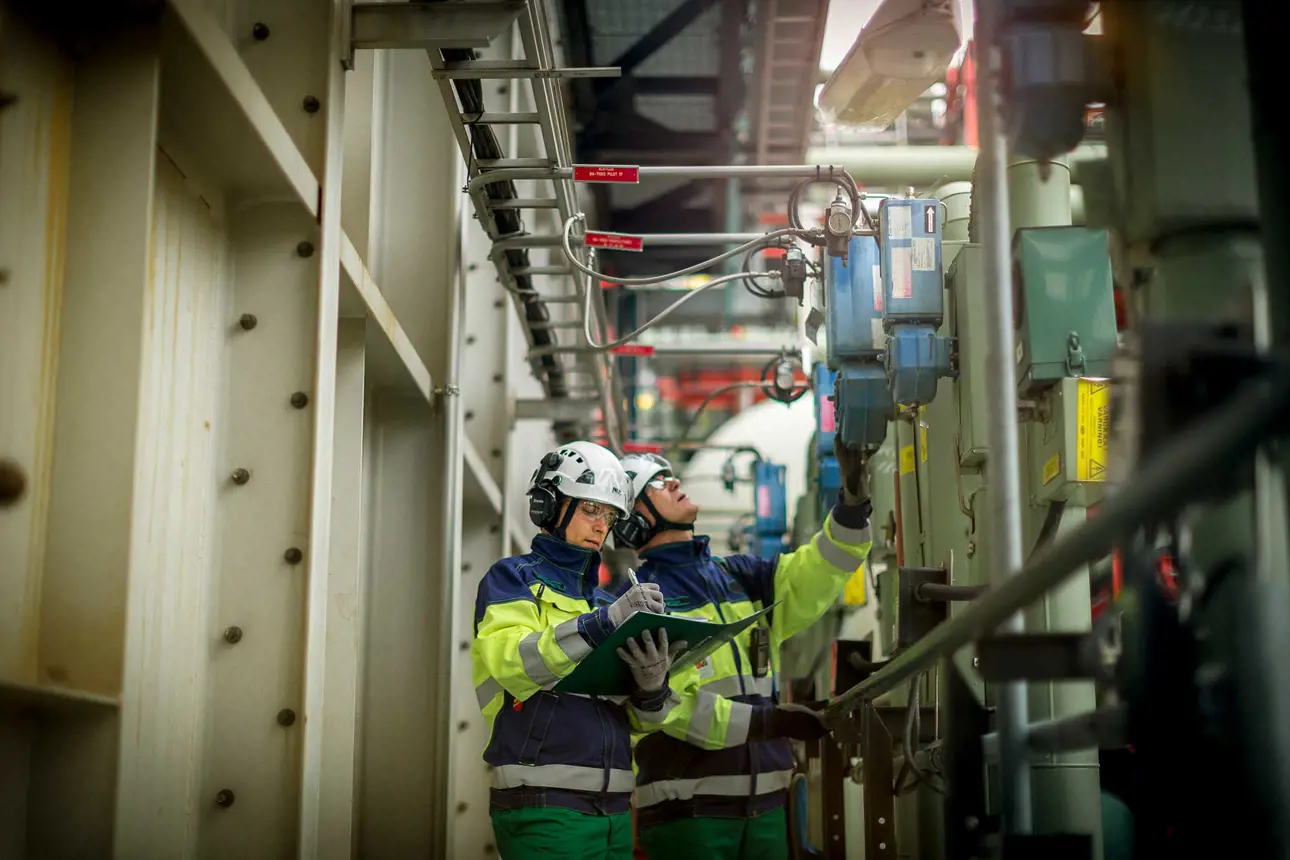
Sustainability as a driving force behind valve design
In the not too far past, valves were reported to account for a large share of baggable fugitive emissions and thus the potential release of greenhouse gases into the atmosphere. So, it is no wonder that it is not just due to losses with a monetary value, that valves today are expected to perform better than in the past. Social pressure for more sustainable industrial processes with a reduced environmental impact has helped accelerate the development of industrial processes and the devices used in them. Environmental concerns in general are one of the biggest global megatrends driving technological development. The case is the same for industrial valve solutions.
Sustainability factors are also driving legislation. Ever-tighter emissions limits are being set across the board. Meeting relevant standards and holding the right certification is quickly becoming a must. This is the kind of general development that Neles whole-heartedly supports. The sustainability demands placed on industry are coming from increasingly environmentally conscious consumers, investors and society at large.
We are seeing major oil corporations publicly including emissions reductions into their business targets. In some cases, the bonuses of executives are already tied to meeting environmental performance targets. The correct selection and sizing of valves can significantly help in achieving lower emissions. By requiring valve suppliers to comply with key standards, such as the ISO 15848, process owners and operators can be sure of stringently tested performance with minimal fugitive emissions and leakage.
Rapid industrialization and continuing global population growth have continued to increase demand for industrial goods. The first air pollution laws were put into place to curb industrial emissions in the United Kingdom already in the 19th century. Strict laws were put into place in the emerging industrial power-houses, USA and Germany in the 1960’s. Today, limitations are a global phenomenon, and they are getting more and more strict, and more specific in their content. In addition to national legislative and regulatory standards, international standards and even end user-specific standards are commonly adopted by industrial plants.
Why fugitive emissions matter
When talking about the reduction of fugitive emissions, we can see that it is not just an environmental act. Even though environmental performance is a high priority, minimizing losses due to fugitive emissions and leakages is a matter of money. The lost flow medium means both lost raw materials and smaller end-product yields. The more complex and processed the flow media is, the higher price it has per mass unit. The loss of flow medium is also lost energy, as the pumps or compressors must do extra work to compensate for the leakage. A considerable amount of money can be saved by minimizing fugitive emissions.
monitoring may provide an alternative means for fugitive emissions monitoring.
Also, when dealing with often potentially volatile and harmful gases health and safety are major concerns. A leaking packing could represent a huge safety risk at any plant and even be lethal. Pure oxygen, even if we don’t think of it as dangerous, can be highly explosive and flammable and a hydrogen leak for example can easily ignite a flame that is hardly visible to the naked eye. Potentially catastrophic incidents can be avoided by ensuring that the atmosphere outside of your valves and pipelines is free of the industrial gases flowing within.
By demanding that the most comprehensive fugitive emissions testing is carried out on delivered valves, end users can introduce significant health, safety and environmental benefits at their process plant, even as they improve their operating cost factors. Compliance with the highest current standard, ISO 15848-1, also means compliance with a majority of other common standards.
The ISO 15848 standards is internationally recognized and sets a requirement for close to zero emissions for processes involving hazardous fluids and volatile air pollutants. The standard is split into two parts. The first, ISO 15848-1, covers the classification system and qualification procedures for type testing of valves, including grades of temperature, firmness, and susceptibility to leakage. The second, ISO 15848-2, covers production acceptance testing of valves that have been approved to ISO 15848-1. This involves a simpler helium sniffer test, carried out at room temperature with five mechanical actuations. ISO 15848 defines three leakage classifications that specify maximum leakage rates, with Class A being the most stringent.
There is a clear shift among process industry end users towards favoring the ISO 15848 emission standard as the most unified tool for measuring and realizing their fugitive emissions performance objectives. This has been a strong incentive behind Neles' continuing pursuit of excellence in terms of developing a wide range of theoretical and technical knowledge as well as laboratory facilities, along with the testing and reporting capabilities needed to fulfill the current standard’s Class A/B leakage requirements.
Designing for minimized emissions and maximized safety
Long before a valve can be tested and certified, it has to be designed and manufactured. Creating a valve that performs well requires an in-depth understanding of where and for what purpose it will be used for. Also, understanding the flow media is crucial. In the design phase, knowing the industrial processes and environments a valve will serve in play a key role in mechanical design, material selection and valve sizing.
Sealing properties are always under special scrutiny. The potential for leakages does not only exist along the seal between the valve and pipeline, but within the valve construction itself. The tightness of the design of the valve stem is particularly important in reducing fugitive emissions. For example, live-loaded packing, which is becoming the standard for quality valves, can be found in the stem of Neles valves delivered for processes with a risk of fugitive emissions. Simulations for tightness and emissions performance are always a part of the design process.
While minimizing fugitive emissions is largely dependent on the physical sound design and construction of the valve itself, the utilization of process data to monitor and optimize performance can help ensure the safety of automated valves while in operation. Accurate, real-time process performance data can show and alert the plant operators of any abnormality or deviation in performance, like excessive travel, oscillation or increased friction, which may be an indicator of possible leakages. Since atmospheric gas leakage is extremely difficult to detect, smart digital solutions such as NDX-type advanced valve positioners or loop performance monitoring may provide an alternative means for fugitive emissions monitoring.
And since long-lasting absolute tightness is practically impossible to achieve, being able to rapidly react to any issues is just as important as having valves that minimize these issues. Early indicators of reduced performance will allow you to carry out further testing by bagging the valve or using the sniffing method, measuring the presence of gases in the atmosphere surrounding the valve.
Neles has been designing and manufacturing valves for industrial applications since the 1950’s, bringing to market many of the valve features that have become the industry standard and the basis for valve designs still in use today. Continuous development is in the DNA of the company, always looking to stay at the forefront of industrial valve solutions that meet and exceed customer expectations. Neles' manufacturing and testing facilities are state-of-the-art, and the people working on your valves are both experienced and highly dedicated.
Servicing valves and changing seals is just a small part of what service means to Neles. Comprehensive lifecycle services are available to ensure that you get the best possible performance from your Neles valves over the entire operating life of your plant. Well-planned predictive maintenance ensures long-term plant performance, reduces the risk of unforeseen failures and helps achieve safe and sustainable operations. Neles' service network with its comprehensive geographical coverage ensures service availability globally.
Testing is the key to knowing
Every valve that leaves the Neles factory is always tested to ensure performance. Valves in demanding services, often deal with high pressures and potentially harmful liquid or gas flow media. In these cases, meeting the customer’s process requirements and the limitations set by legislation and certification criteria is always a given.
A large portion of Neles™ metal-seated and Jamesbury™ soft-seated valve products are certified to meet the requirements of the global ISO15848-1 standard, complying with many standards mandated in specific regions, including TA-Luft (Germany) and EPA 40 CFR parts 60/63 (USA). Meeting these tight requirements is also a mandatory requirement in the majority of current projects in the oil and gas industries worldwide, and increasingly in other process industries as well.
Neles' fugitive emission knowledge is based on strong in-house capabilities where fugitive emission theory and testing are combined with skilled working personnel. The company has a large valve testing laboratory where the fugitive emission development and type approval tests are done. Neles valve products are designed and tested to ensure minimizing fugitive emissions even at high operating temperatures, meeting the demands of even the harshest hydrocarbon processing plant environments.
By minimizing fugitive emissions, these valve products help Neles' customers improve health and safety for workers, allowing plants to meet regulatory standards, reduce product losses and ultimately improve the environmental performance over the entire lifecycle of the plant.
Text by Jukka Borgman and Ilpo Miettinen. For additional information, please contact toni.kotiranta@valmet.com
This article was originally published in Fugitive Emissions Journal, December 2019 as ‘Metso: Sustainability is a serious business – Responsible design and rigorous testing makes for better valve solutions’.
Text originally published in 2019, and slightly updated in April 2022, due to the company name change to Valmet.
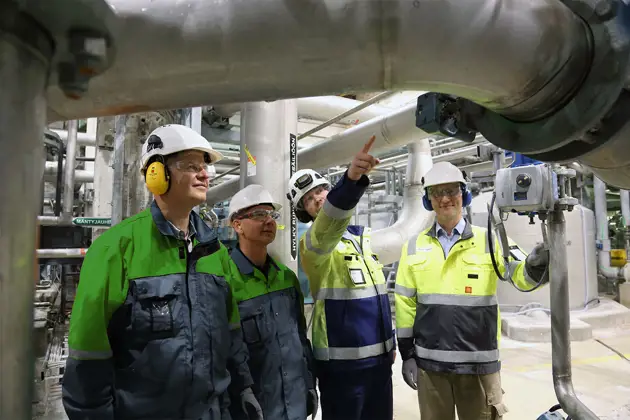
Subscribe to our newsletter
Subscribe now to our 'Go with the flow' newsletter and receive the latest insights directly to your email.
SubscribeRead more about sustainability and innovation