How to prepare for a successful digital transformation
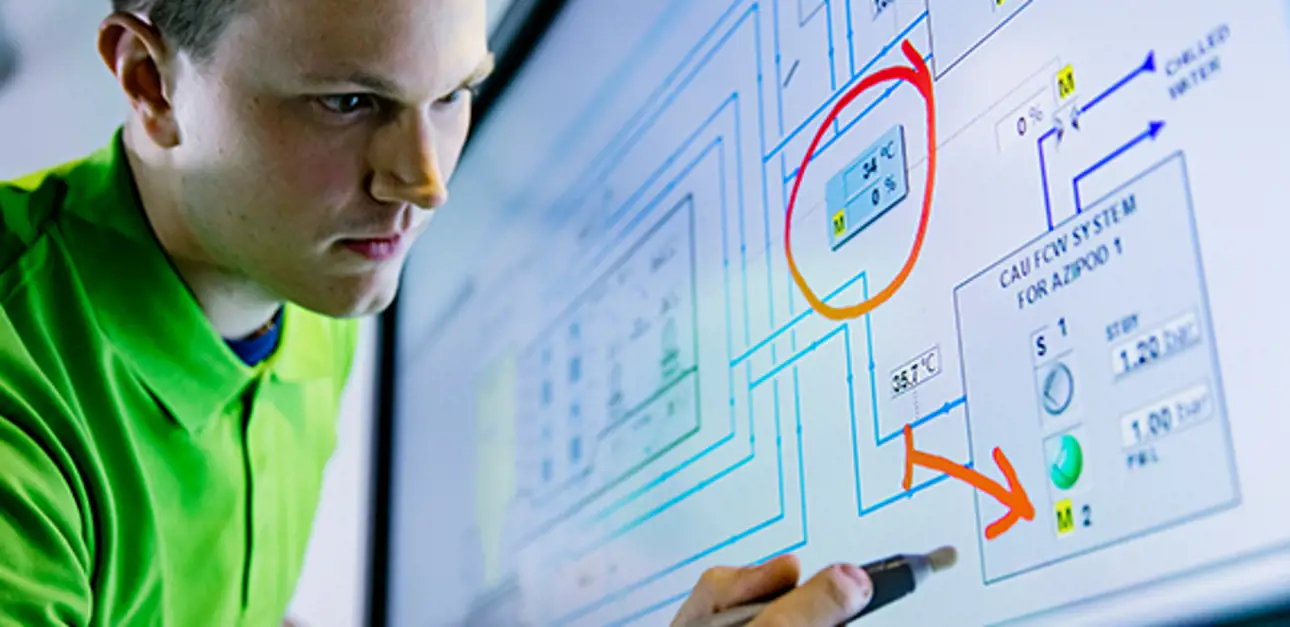
Supply chain disruptions continue to drive raw materials availability down and pulp prices up. Tissue manufacturers need to maximize efficiencies across the value chain, and many are doing it through equipment optimization.
Decision makers are taking this opportunity to evaluate their facilities’ digital readiness in order to align capital equipment investments with short and long term goals. Digitalization drives efficiency, but not every plant is equipped with the same level of digital capabilities.
Preparing your facility for digital transformation takes a realistic understanding of where you rank in terms of digital readiness. Accomplishing the transformation takes partnering with Valmet — a tissue equipment manufacturer that is a leader in digital innovation.
Determining digital capabilities
Industry 4.0 is centered around technology. Data, connectivity, and automation are all gateways to overall equipment efficiency (OEE) for tissue manufacturers — an important advantage as tissue product lines and customer demand continue to diversify.
However, embarking on a full digital transformation without first evaluating your starting point could prove costly.
To better understand and plan for improving your digital capabilities, evaluate your current status based on the following categories1:
- Unconnected: No machine networks or data capturing tools are in place
- Sensor connectivity: Machines contain sensors and/or other data-gathering tools, and production lines are networked and managed by IT professionals; operational processes are not sophisticated enough to fully leverage the data
- Data-driven efficiency: Machine network connectivity is sufficient to capture critical data (machine downtime, part defects, product tracking information, etc.) and funnel it to a centralized data repository; there is the commitment to use data for OEE but a lack of analytics and plant-level application resources
- Analytics-driven efficiency: Data scientists/IT professionals oversee data collection, analyze information, help develop plant-level applications and drive business process change within one facility, but not necessarily across locations
- Transformational capacity: Machine connectivity, security, data gathering/retention/analytics are excellent, and capable of extending across facilities and value chains; there is full and functioning support from leadership including change management teams that encompass communications, processes, training, and analyst resources
You may clearly identify with one category of capabilities, or maybe it’s not that clearcut. An honest assessment of your current status will help you Identify next steps for maximizing OEE while also informing how to derive the most value from digital transformation.
The framework of digital transformation
Knowing your starting point helps you build the framework necessary to make your journey to digital transformation valuable and successful. Use these guidelines to keep you on track2:
- Begin at the beginning: Start with assessing your core processes and data collection capabilities related to those processes.
- Don’t implement technology for technology’s sake: Focus on automating basic data collection and analyses, using a systematic approach that incorporates phases of sensors and artificial intelligence (AI)
- Make sure digitalization benefits everyone: Technologies and data should be able to be adapted and used by all levels of the organization, from the plant to the leadership team
- Build in continuous improvement: Being transformational requires benchmarks to measure change. Tie data to key performance indicators (KPIs), and share results to encourage your entire team to support digital transformation
In an industry hampered by uncertainty in supply chains and an ongoing labor crisis, automated production lines that allow manufacturers to remain nimble and responsive to shifting needs are attractive. The key is not to get swept up in all that digital transformation can do, but rather how to use digital transformation — and your strategic partnerships — to your best advantage.
Sam Operational Solution
Sam operational solution is the ideal set of digital solutions for transitioning to an Industry 4.0 manufacturing plant, focusing on several parts of the production line. Ecosystem Sam flow can be used on any line configuration and is compatible with any OEM tissue converting roll, fold, and packaging machines and layouts — harmonizing product flow, and stabilizing each machine speed:
Converting Roll Equipment
- Perini Sam perf allows for continuous automated monitoring of perforation quality while the line is running at any speed, for each sheet and roll. Accuracy falls within the range of a few millimeters and can be easily adjusted using the system’s “active” function
- Perini Sam log is the first quality control system that allows operators to check log winding and, if needed, adjust production parameters to prevent the risk of non-conformities. Controlled via HMI panel, log samples are pulled, checked, and reintroduced into the production line while the machine is running — meaning no downtime and no scrap
- Perini Sam emb monitors embossing quality live at all speeds using a set of cameras to inspect the web coming out of the enbosser. A neural network trained by a deep learning algorithm processes the images to detect defects and adjust parameter. Desired embossing quality is restored with minimal finished product waste
- Perini Sam VAR offers advanced machine fault monitoring through video recordings captured and managed within a system of cameras and software for faster troubleshooting and less downtime. Once a fault occurs, the operator can automatically migrate all recordings from the affected area to a dedicated touch-screen monitor for review and identification of the root cause
Converting Fold Equipment
- MTC Sam cut continuously monitors the position of cutting blades and automatically assesses sheet-by-sheet log cut quality, eliminating the need for manual checks and line downtime
- MTC Sam reel reads the main characteristics on the parent reel label, and sends the information to the line wherein software-driven automatic adjustments are made to line control and operating parameters
- MTC Sam vacuum automatically or manually manages the degree of actual vacuum based on head fold speed and on the desired depression set-point, minimizing downtime and saving money by aligning energy demand with need
Packaging Equipment
- Casmatic Sam pack uses HD cameras, light bars, and a deep learning algorithm to detect primary packaging defects (i.e., poor bonds, errant print positioning, wrap cracks, etc.) and initiate ejection of affected packages
- Casmatic Sam cut monitors wrapper cutting blade wear, detects packaging film perforation issues, and signals operators to take corrective action to prevent potential jams or downtime — all while the wrapper is running. The technology increases efficiencies and keeps operators out of harm’s way as they do not have to enter the wrapper for fixes.
Regardless of where you’re starting on your digital transformation journey, we’re ready to answer your questions, identify next steps, and guide you through the process. Contact the Valmet team to learn more.
SOURCES
1Sight Machine, How can knowing your plant's digital readiness determine your success?, Undated
2Plant Services, When beginning your digital transformation journey, should you invest in machines or in enabling operators?, January 19, 2022