Beyond Circularity: POWER Beyond seeks to minimize friction through aerostatic solutions
Aerostatic bearings and seals have traditionally been used only in precision instruments. What if they could be applied into heavy industrial machinery?
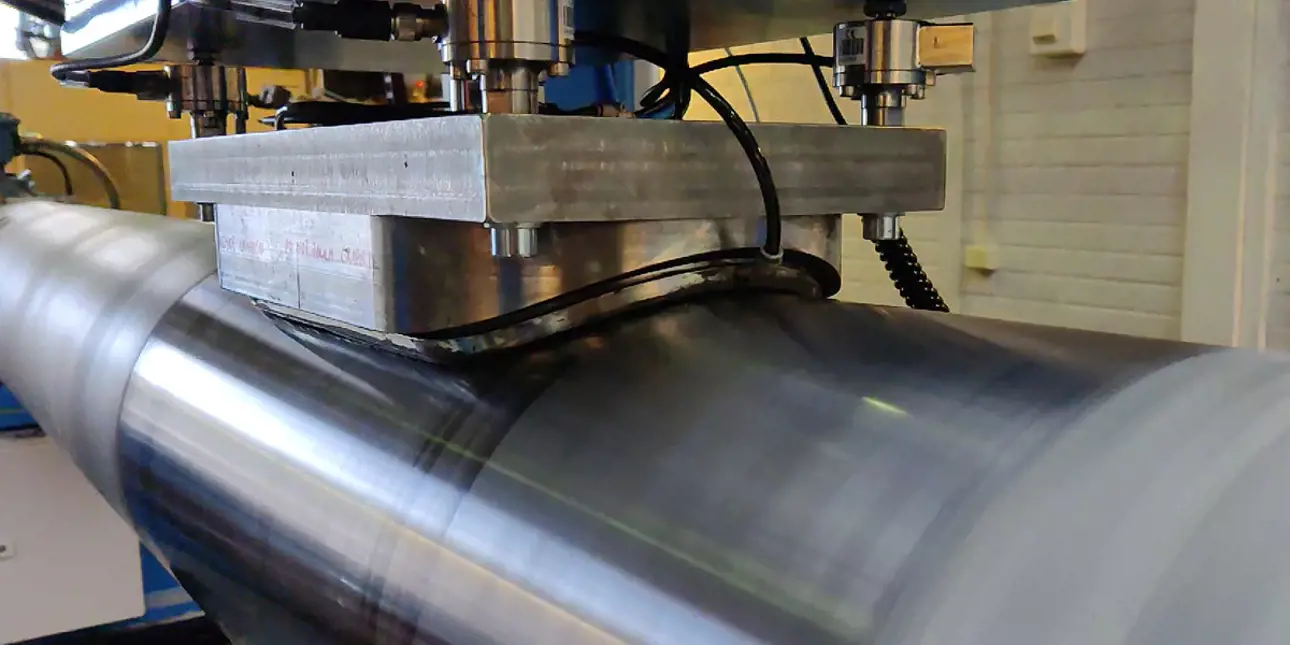
Achieving circularity requires sustainable solutions for minimizing energy usage. A significant aspect is reducing friction, with global industry estimates indicating that friction causes energy loss equivalent to the output of twelve nuclear power plants daily.
Part of Valmet’s Beyond Circularity program and its ecosystem, the POWER Beyond project is seeking new innovations and applications for frictionless aerostatic bearings, aerostatic sealing, and improved vibration control. Working together with Aalto University and other industrial partners, Valmet is especially looking to discover ways for making paper machine rolls more energy efficient.
With the global megatrends of increasing eCommerce and demand for hygienic products, there is an opportunity for making a truly positive impact by finding energy efficient solutions for producing carboard and tissue products,
says Raine Viitala, Assistant Professor at Aalto University.
Thinking outside the box
The POWER Beyond project is breaking new ground in aerostatic applications. Traditionally, this technology has only been useful in highly specific applications with very tight tolerances, namely in precision instruments and high-velocity rotors. The project is exploring robust and dynamic aerostatic bearings that can adapt to different use cases in heavy industrial machinery.
“A paper machine roll traditionally features oil-lubricated pads for deflection compensation, a method that requires energy due to pumping and friction. We are exploring possibilities for replacing these hydrodynamic bearings with frictionless aerostatic seal units and loading shoes that adapt to the roll’s surface and movement,” says Valmet’s Technology Manager Jyrki Huovila.
If proven feasible, the project can result in aerostatic applications with wide industrial appeal. Such bearings and seals would allow looser tolerances and be cheaper to produce.
Air barrier load and eccentricity testing in the Aalto University laboratory
Another key research area is improved vibration control that could enable higher drive speed ranges and more efficient machinery. Valmet is especially interested in improving the vibration stability of paper machine winders through active hydraulics.
Securing Finland’s industrial future
Aerostatic bearings have not been used in heavy machinery because they are rigid, require precise manufacturing with narrow tolerances, and are relatively expensive to produce. According to Raine Viitala, the fact that someone is finally considering aerostatic solutions for something other than precision applications has generated international excitement.
“For me, this research holds two primary outcomes. Firstly, it aims to generate technological innovations, providing the Finnish industry with a competitive advantage. Secondly, as the project team comprises mainly doctoral students, we are sowing the seeds for future innovations by offering these emerging researchers an opportunity to engage with cutting-edge technology with immediate practical applications,” Viitala says.
The project began in 2022 and will continue into 2025. The research has already produced promising breakthroughs, and the first proof of concept with test equipment was a success in a laboratory setting. Jyrki Huovila says:
“I truly believe that aerostatic bearings and seals will be utilized in paper machinery in the not-so-distant future. With Aalto researchers’ bold ideas and our technological competence combined, we can create something truly radical in this field.”
“Valmet is a leading manufacturer of paper, carboard and tissue machines. They have embraced a policy of openness and like Aalto University, are committed to sustainability through tackling difficult challenges. This means that we have a real opportunity to instigate change within the industry,” Raine Viitala sums up.
Valmet's Beyond Circularity program is implemented through seven streams. The POWER Beyond project is part of the Resource efficient industries stream.
Project summary
- Target: To discover new applications for aerostatic bearings and seals, while improving machine dynamics through active hydraulic vibration control.
- Project timeline: 2022–2025
- Research partners: Aalto University, Dynator Oy, Etteplan Finland, Fiellberg Oy, KONE Oyj, Kongsberg Maritime Finland Oy, Tiivistekeskus Oy, Tiivistetekniikka Oy, Vibrol Oy, Business Finland Oy, Valmet Technologies Oy
- Project budget: 1,8 MEUR
- More information: Aalto University: POWER Beyond – Process optimization with friction- and vibrationless technologies for energy efficiency and circularity