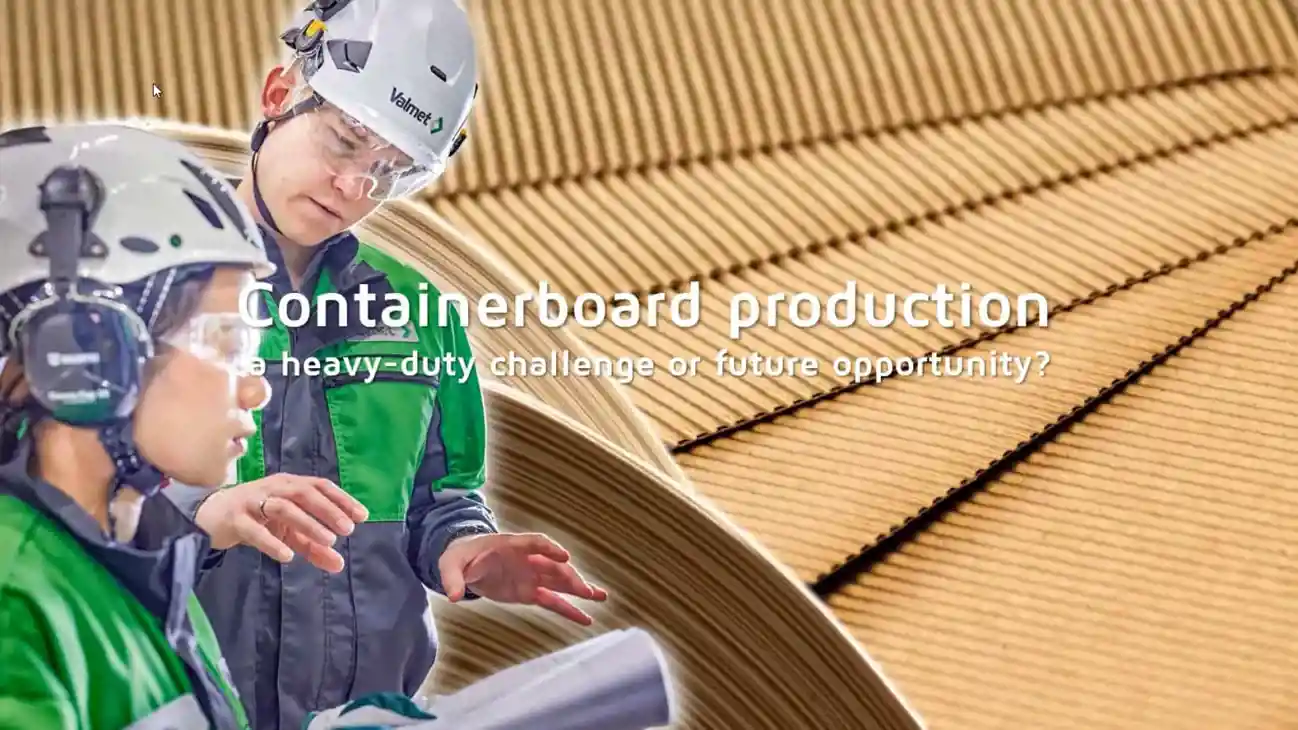
Valmet’s way to serve containerboard production with fiber workshop services, rolls, covers, and roll maintenance optimized for your needs.
Do you want to know more?
If you wish to get further information like technical specifications, need a quotation, or wish to discuss different solutions, fill in the contact form and our experts will contact you shortly.
Contact our expertsAre you ready to achive these results with us?
25%
Lower amount of web breaks
10-15%
Lower steam consumption
50%
Reduce profile related broke

Wet pressing in containerboard production
A key to higher energy efficiency, and often a significant enabler of a capacity increase, is optimal wet pressing performance. Increased nip dewatering improves drying capacity and increases sheet dryness, with a remarkable effect on energy costs.
For example, increasing post-press dryness by 1.5 percent unit means savings of approximately €1.3 million in drying energy costs (case linerboard 400,000t/a).
Energy savings
Increased dry content after press
Material savings
Stronger sheet due to higher dry content
Production efficiency
Higher sheet dryness
Fewer breaks and better runnability

Hard news for boardmakers
Modern, wide, high-speed containerboard machines operate in demanding conditions in terms of machine component wear. Forming section wire rolls offer a typical example of components that require uncompromised wear protection. Read the whole article
We prefer a situation in which the lead rolls can be left in the machine for several years without having to repair or even think about them.
Explore Valmet Rolls and Workshop Services offering for containerboard production
Related videos
Questions?
Provide your information below and let our experts contact you to discuss in more detail about your targets. You can also send us questions and we will get back to you shortly.