Autopilot for optimizing boiler capacity, efficiency and emissions
Valmet DNA Combustion Manager
Unlock the full potential of your power plant with Valmet’s advanced boiler optimization. By resolving process limitations and stabilizing combustion across all operating conditions, you can significantly enhance performance and profitability. Whether you're aiming to push for a new maximum load, identify the true minimum load, or reduce emissions, Valmet DNA Combustion Manager empowers you to get the most out of your existing or new boiler.
Stable and efficient combustion in all operating conditions
Increased boiler capacity by up to 5% at maximum load
Reduced CO₂ and up to 30% lower NOₓ emissions
Maximized profitability in electricity markets through improved flexibility and boiler control
Meet performance targets with Valmet DNA Combustion Manager
Valmet DNA Combustion Manager is an advanced process control solution designed to optimize combustion in bubbling and circulating fluidized bed boilers as well as waste-to-energy boilers. This modular application continuously adapts to changes in production, fuel quality, fuel flow, and combustion conditions - ensuring stable and efficient performance around the clock.
Fully integrated into the Valmet DNA DCS and the Valmet DNA UI, the solution provides a seamless user experience for operators. As a multivariable closed-loop controller, it simultaneously manages multiple process variables to optimize combustion performance.
With a typical payback time of less than one year, Valmet DNA Combustion Manager delivers fast, measurable improvements in boiler efficiency, emissions, and operational flexibility.
Environmental, operational, and financial benefits
Valmet’s boiler optimization solution enables compliance with stricter emissions and efficiency standards. It enhances boiler flexibility and operational range, reduces reliance on flue gas chemicals, and increases the use of more cost-effective fuels. This solution is an ideal choice for adapting plant operations to the challenges of a volatile electricity market.
By unlocking additional capacity for the electricity market, it ensures availability precisely when it’s needed most.
Typical result of load maximization: a 65% reduction in steam flow fluctuations leads to a 0.6 MWe increase in net electricity production.
Measured impact of optimization on emissions and efficiency
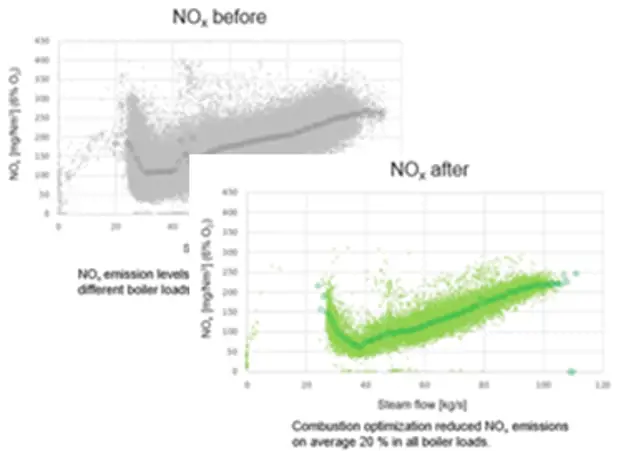
NOx reduction
Following the optimization project, average NOx levels—plotted against boiler load—typically decrease by 20–30%. Enhanced combustion efficiency reduces reliance on secondary NOx control methods, yielding savings in additive expenses.
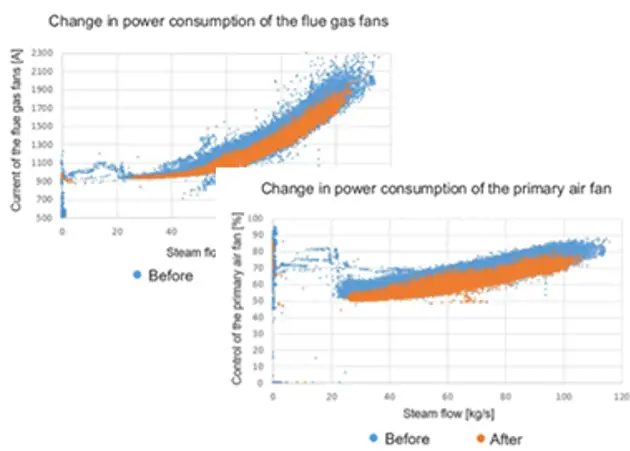
Reduced electricity consumption of the plant
The power consumption of the flue gas fan (left) and primary air fan (right) was measured before and after the optimization project.
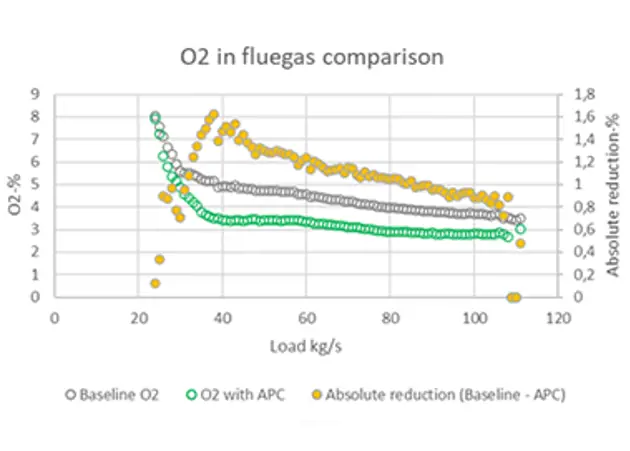
Boiler efficiency improvement project
The optimization resulted in approximately a 0.5% improvement in boiler efficiency.
Complementary solutions for enhanced boiler performance

Want to learn more about our process optimization solutions?
Share your requirements, and our experts will reach out to assist you shortly.
Contact us