Press improvements for board and paper making
Press improvements provides customized solutions for your press section
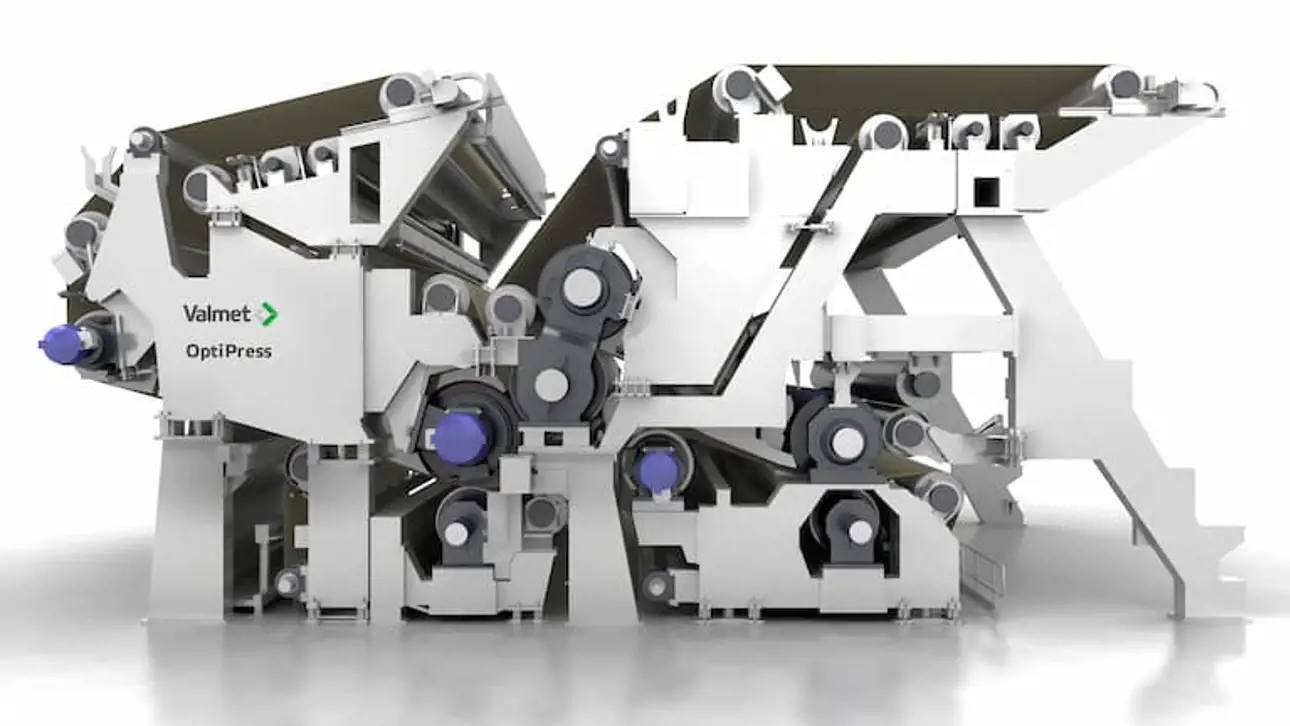
With an improvement process you can reduce your cost per tonne produced through savings in raw materials, energy, and maintenance costs. We offer a variety of customized solutions that will improve the dry content of the pressed sheet, solve runnability problems, and address a variety of press section issues.
Improved runnability
Energy savings
Maintenance cost savings
Higher availability
Challenges with water removal?
Do you experience press section water removal challenges in the form of drying capacity limitations, poor runnability or cleanliness problems? Water removal improvements are targeted at increasing the dry content of the sheet after the press section. Higher dryness reduces steam consumption, improves runnability and in some cases also enables higher operating speeds. Improved runnability means better machine efficiency and savings in energy and materials. Runnability improvements provide higher machine efficiency through reduced sheet breaks and optimized tail threading and pick-up operation.
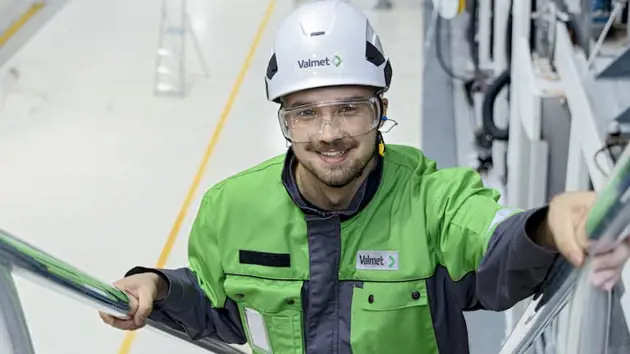
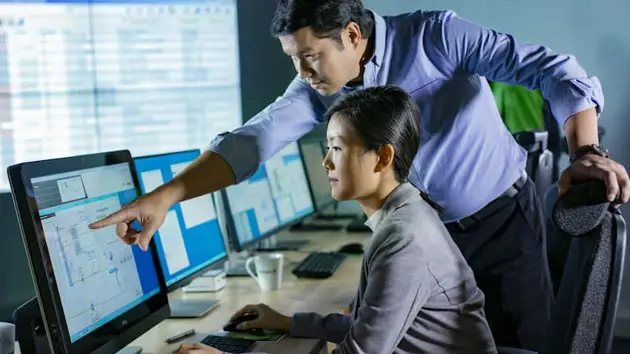
Cost saving felt conditioning solution
The performated Valmet Uhle Box Cover is an effective and straight-forward solution to increase dewatering and reduce enery consumption in the press section. The more effective dewatering performance of a perforated Valmet Uhle Box Cover stems from the long dwell time in the suction area. The surface geometry of the perforation pattern improves water removal at a lower vacuum level. The cover provides stable support for the felt over he entire suction area; there is no "diving" into slots as with conventional covers which means that felts run longer.
How to keep moisture profile in control?
Appropriate sheet dryness levels and uniform moisture profiles are vital for good press and dryer section runnability and high energy efficiency. Profile management improvements are targeted at restoring sheet dryness and moisture profiles that have deteriorated over time due to friction and other press nip loading system problems. Our solutions also provide tools for active moisture profile control.
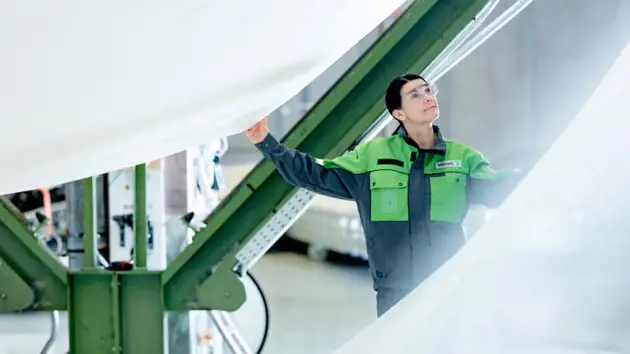
Do you want to know more about process upgrades?
If you wish to get further information like technical specifications, need a quotation, or wish to discuss different solutions, fill in the contact form and our experts will contact you shortly.
Contact usReferences and articles
Related pages
