Increased capacity with extremely fast parent roll change
Valmet Dual Unwind
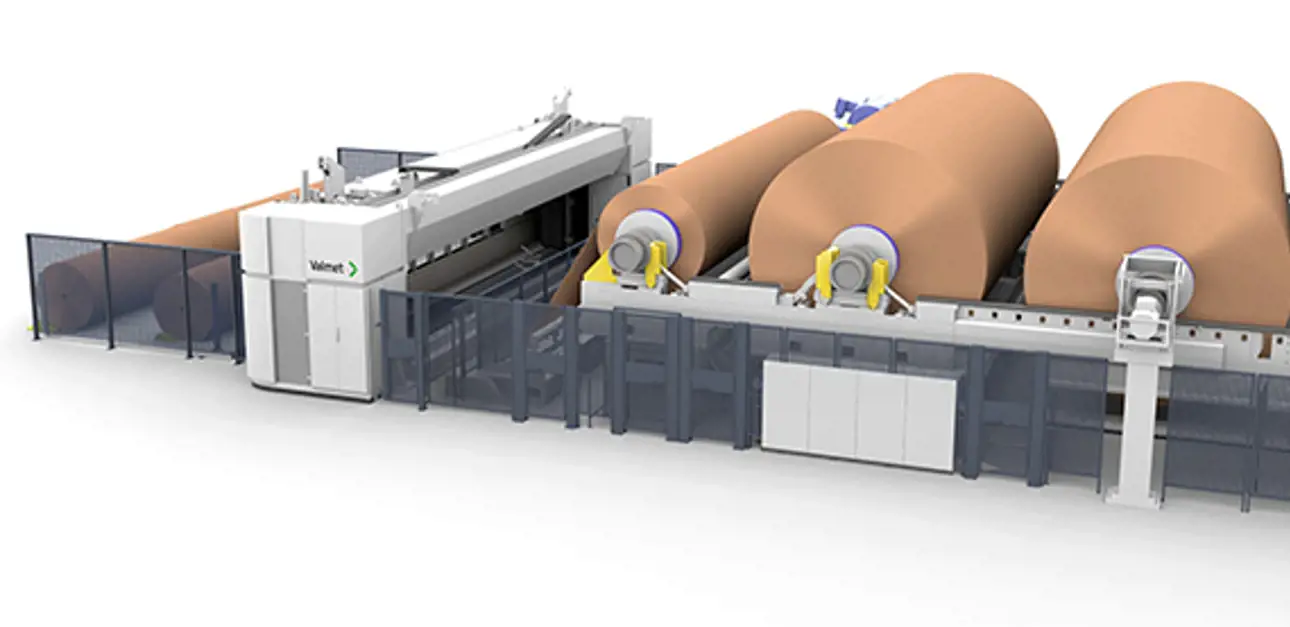
Why store spools in two positions? Why pause production when changing the parent roll? Why not have a winder with two unwind stands instead? Valmet Dual Unwind is an exceptionally fast way to make a parent roll change at the winder. You’ll end up with more production and higher winder capacity. Valmet has a proven technology with a solid 10-year track record with over 50 references!
New thinking at the paper machine finishing area
A decade ago, Valmet launched a revolutionary winding equipment that would significantly increase capacity. The first one was delivered to Propapier. After this first start-up, over 50 Dual Unwind solutions have been sold already to increase winding capacity. Dual Unwinding makes it possible to get rid of additional reel spool storages at the winder. There is no need to pause the production due to parent roll change as earlier. The Dual Unwind sequence is fully optimized and independent of a crane.
Dual Unwind in numbers
> 50
systems sold
< 1 min
parent roll change time
30-50 %
capacity increase
Old type of finishing area
New type of finishing area with Dual Unwind
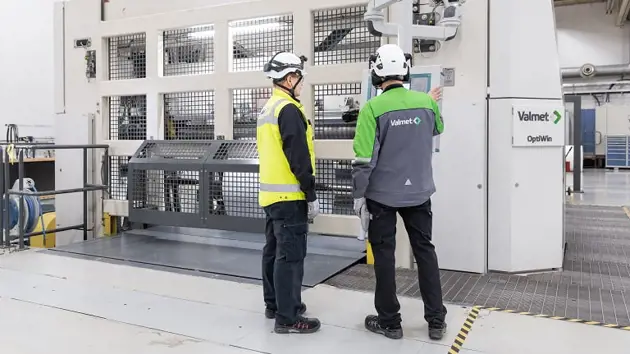
Want to talk to our winders and roll handling experts?
If you wish to get further information like technical specifications, need a quotation, or wish to discuss different solutions, fill in the contact form and our experts will contact you shortly.
Contact our expertsHigher winding capacity
With Dual Unwind, you’ll get:
- One-minute parent roll change
- Typically 30 % more capacity for winders - even over 50%!
- For winder modernizations and new winders
With conventional parent roll change solutions, fast manual changes are 5-6 minutes. However, typical measured parent roll change times in the industry are on average some 9-12 minutes. With this in mind, a one-minute parent roll change with Dual Unwind is very fast. This alone leads to big savings with the capacity increase at the winder. Depending on the winder, the capacity gain can be substantial.
The movements of parent rolls are arranged to happen simultaneously with the set changes, which is a robust solution to ensure there are no compromises to the roll structure and quality during winding. The second unwind stand is designed only for unwinding the last set from the parent roll. This allows the primary unwind stand to receive a new, prepared parent roll during winding.
The dual unwind can be delivered with two different splicing technologies, a conventional flying splice or a butt-joint splice, BJS, which will prepare a sellable splice.
Butt-joint splicing delivers:
- High-quality splices that run through the printing press
- Excellent splicing quality and reliability
- Suitable for all paper/board grades
- Automatic tail threading from parent roll to slitter section
- Unwinding from above and under
Butt-joint splicing
Interested in pilot trials?
Get in touch with our pilot trial experts to discuss how you could benefit from our pilot trial services.
Contact our pilot trial expertsHow do you plan a successful rebuild?
Rebuilding a paper or board machine can improve the competitiveness of your business and your processes. Download our e-book to learn more.
Download e-bookPlanning a grade conversion?
The world is changing fast; the consumption of papers is decreasing and boards increasing. Update your paper machine with Valmet to produce more profitable products.
Discover moreLearn more about the services and automation solutions for winders
Explore our latest board and paper press releases
- Jun 13, 2025Dr. Jin-Doo Kim awarded with a Medal for Extraordinary Achievement for decades-long work for promoting board and paper technologies
- May 26, 2025Valmet to supply a fifth Advantage tissue production line to Lila Group in Turkey
- May 21, 2025Valmet to supply a major paper machine rebuild to Sylvamo in North America
- Mar 27, 2025Successful start-up of Zhejiang Forest United Paper’s PM 6 production line
- Mar 27, 2025Valmet to supply two winders to Wuzhou Special Paper in China
- Mar 6, 2025Valmet to supply a high-capacity winder to Jingxing Holdings in Malaysia
- Jan 21, 2025Valmet to supply an off-machine coater to a customer in Asia-Pacific
- Nov 12, 2024Valmet to supply a complete papermaking line to one of its major customers in Asia-Pacific
- Oct 21, 2024Valmet’s change negotiations completed in Finland in its Paper business line’s Board and Paper Mills business unit
- Oct 3, 2024Valmet to supply an OptiConcept M board making line to Anhui Linping Circular Development in China