Innovative gap forming technology yields excellent results
OptiFormer Gap with shoe and blade forming section
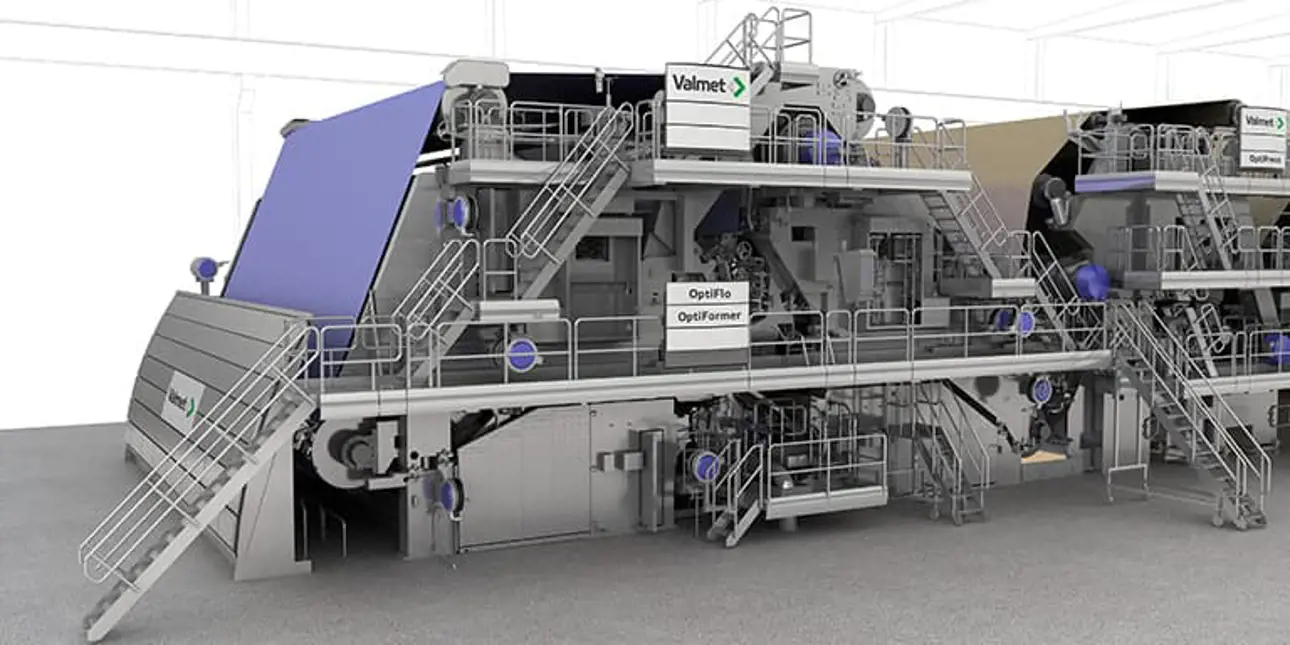
Valmet’s novel gap forming technology OptiFormer Gap utilizes innovative shoe and blade technology to gain superior paper quality. This new concept has been studied extensively on the pilot machine scale, and results from several running production machines compare very well with the pilot results. The formation has beaten all other references.
Good strength properties and uniform CD profiles
Adjustability and cleanliness at a new level
Uniform visual appearance of the end product
High-speed potential and excellent formation
Excellent formation in a wide basis weight range with gap forming
Initial dewatering of OptiFormer Gap takes place under non-pulsating conditions utilizing Valmet’s VacuShoe technology. Water is removed in the VacuShoe chamber area (jet landing area) through both the inner and outer fabric producing good retention and symmetric filler distribution at high filler contents in the paper. This very gentle initial dewatering of shoe and blade technology with stabilized jet impingement and minimized free jet length enables an exceptionally wide operating window.
Non-optimized headbox slice geometry (left) versus optimized headbox slice geometry with OptiFlo Gap headbox (right).
After the paper surfaces have been formed, the dewatering continues in the blade dewatering phase, where the loading elements generate pressure pulses and shear forces inside the sheet. This finalizes the excellent formation and high dewatering capacity.
Dry content after the forming section ranges from 22% to 25%. This sufficiently high dry content after the forming section secures good runnability of the sheet at following process stages, e.g. dewatering control at the 1st press nip.
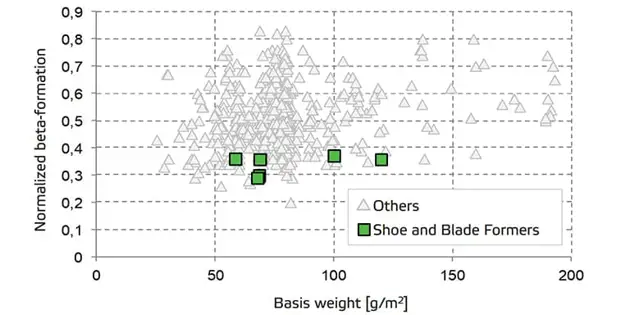
OptiFormer Gap with shoe and blade technology provides excellent end-product quality. A formation comparison (based on production machine data) of different forming methods. Grade: fine paper. Speed over 1800 m/min.
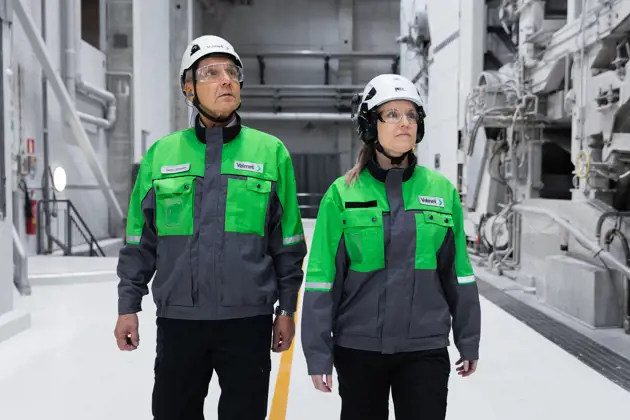
Want to talk to our forming section experts?
If you wish to get further information like technical specifications, need a quotation, or wish to discuss different solutions, fill in the contact form and our experts will contact you shortly.
send an inquiryShoe and blade technology: adjustability and cleanliness at a new level
Forming section with shoe and blade technology can be operated with a variety of grades without having to readjust the forming parameters. A shoe and blade technology allows completely free adjustment of the slice opening, jet/wire ratio, and the jet landing point without causing any sheet disturbances.
OptiFormer Gap with shoe and blade technology ensures excellent runnability through improved cleanliness in the gap area. Unlike the traditional forming section with a forming roll, possible dirt particles are trapped between the fabric and closed roll, but because dewatering happens in the stationary shoe area, dewatering removes dirt from the fabric surface causing no light spots on the paper. Closed breast roll surface also reduces the amount of misting around the headbox slice area. Therefore the top and bottom slice areas are very clean and dry.
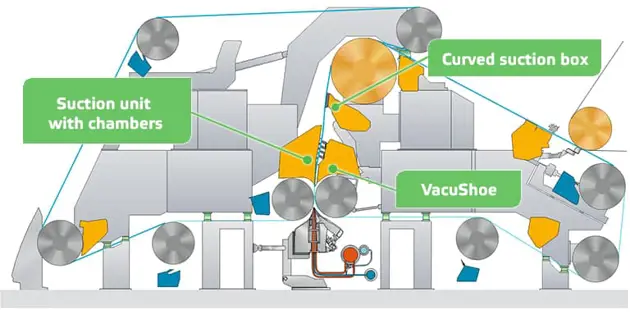
Key components of OptiFormer Gap with shoe and blade technology. OptiFormer Gap with shoe and blade technology is well suited also for rebuilds.
See the shoe and blade technology in action
The video displays the shoe and blade technology in Valmet forming sections with both paper and packaging grade applications. In addition, we show multiple different forming section layout options where shoe and blade technology has been used.
Looking for forming fabrics?
Valmet has constantly improved their forming fabric technology and created fabrics providing excellent runnability, high wear resistance, long running time, good paper profiles and good retention. Specialized forming fabric designs for packaging grades continue to improve drainage.
Read moreHow do you plan a successful rebuild?
Rebuilding a paper or board machine can improve the competitiveness of your business and your processes. But where do you start? Download our e-book to learn how to develop a winning rebuild concept, how to minimize rebuild related risks, and how to ensure smooth ramp up to full production.
Download e-bookPlanning a grade conversion?
The world is changing fast; the consumption of newsprint and printing paper is decreasing and the consumption of containerboards or cartonboards are increasing. An old paper machine can be updated with a grade conversion rebuild to produce more profitable products. Turn a new page for your paper machine with the help from Valmet.
Discover moreExplore our latest board and paper press releases
- Jun 13, 2025Dr. Jin-Doo Kim awarded with a Medal for Extraordinary Achievement for decades-long work for promoting board and paper technologies
- May 26, 2025Valmet to supply a fifth Advantage tissue production line to Lila Group in Turkey
- May 21, 2025Valmet to supply a major paper machine rebuild to Sylvamo in North America
- Mar 27, 2025Successful start-up of Zhejiang Forest United Paper’s PM 6 production line
- Mar 27, 2025Valmet to supply two winders to Wuzhou Special Paper in China
- Mar 6, 2025Valmet to supply a high-capacity winder to Jingxing Holdings in Malaysia
- Jan 21, 2025Valmet to supply an off-machine coater to a customer in Asia-Pacific
- Nov 12, 2024Valmet to supply a complete papermaking line to one of its major customers in Asia-Pacific
- Oct 21, 2024Valmet’s change negotiations completed in Finland in its Paper business line’s Board and Paper Mills business unit
- Oct 3, 2024Valmet to supply an OptiConcept M board making line to Anhui Linping Circular Development in China