Former improvements for board and paper making
Customized solutions to ensure better operational reliability and provide a good return on your investment
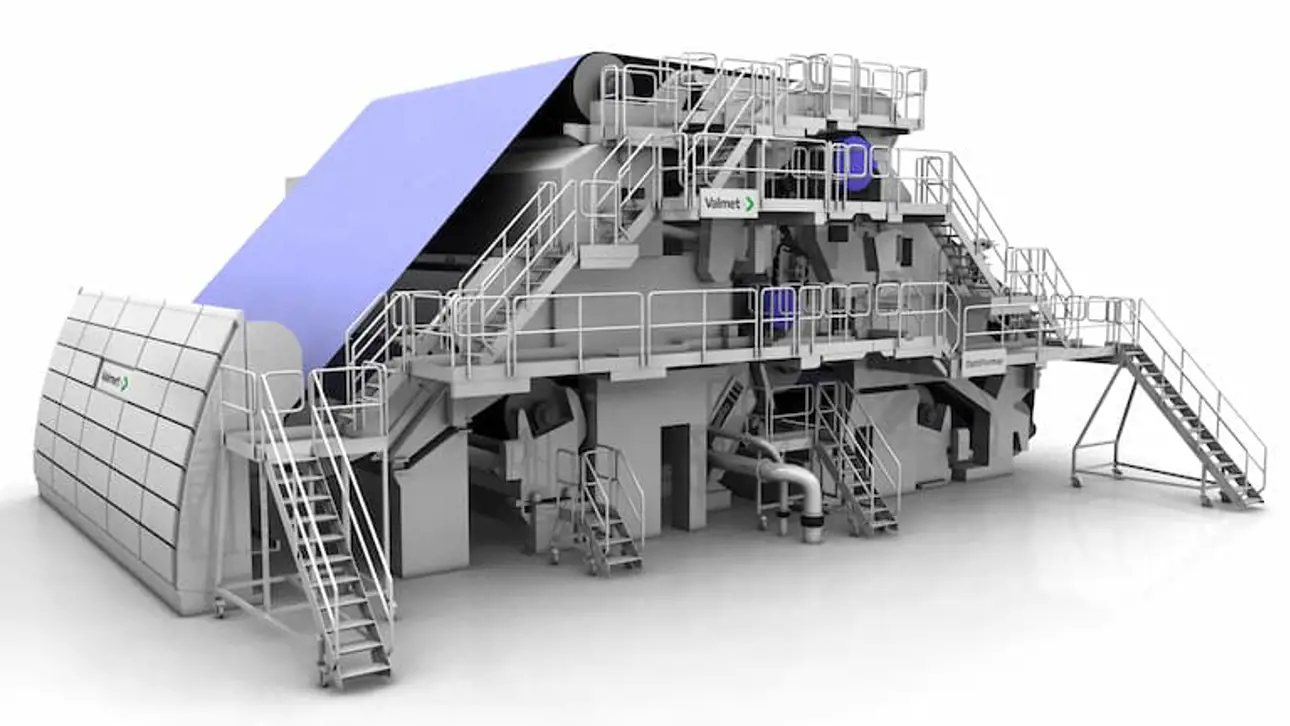
Former improvement solutions help you to ensure that your forming section is performing at the highest possible level. With the customized solutions you will improve paper quality, solve runnability problems, improve dewatering, and ensure better operational reliability. You can also expect measurable results, a good return on your investment and cost-effectiveness.
Paper quality improvements
Runnability improvements
Former dewatering improvements and optimization
What are the benefits from improved paper quality?
Paper quality improvements help to improve formation, optimize running parameters, and solve other paper quality issues. You can revieve one or more of the following benefits:
- Improved formation, strength properties, profiles, and machine cleanliness for optimal end product quality
- Savings in raw materials by reducing the use of chemicals and improving the furnish mix
- Improvements in production efficiency through better runnability and fewer breaks
- Energy savings with optimized running parameters
What are the benefits from improved runnability?
Runnability improvements are aimed at raising the stability of forming section runnability to a new level. You can achieve one or more of the following benefits:
- Improved machine cleanliness, edge area control and fabric control for stable runnability
- Energy savings through reduced break energy waste and optimized dewatering
- Improved efficiency through better runnability and reduced break times
- Savings in fresh water consumption
- Longer lifetimes of fabrics and ceramics
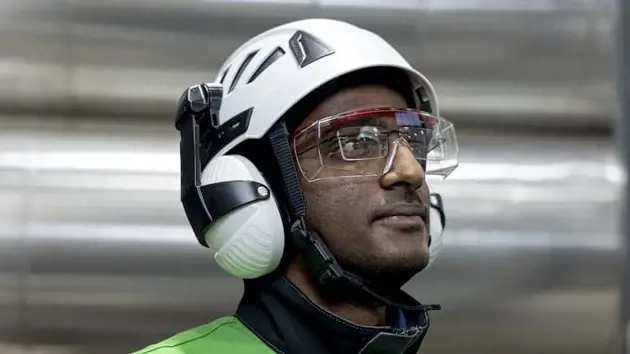
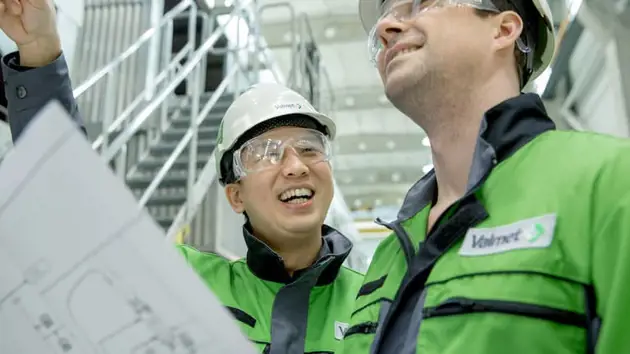
What are the benefits of improved former dewatering?
Former dewatering management targets maximal dryness with minimal effort. You can achieve one or more of the following benefits:
- Higher sheet dry content for improved production efficiency
- Energy savings through optimized water removal and vacuums
- Raw materials savings with improved retention and savings in chemicals
- Maintenance efficiency through longer lifetimes of fabrics and ceramics and improved cleanliness
Condition management for former improvements
Condition management is designed to ensure trouble-free operation and cost-effective maintenance of your forming section.
- Taking the right actions at the right time reduces maintenance costs
- Improved mechanical condition of the forming section ensures peak performance
- Better runnability and minimal downtime boost production efficiency
- A well-maintained forming section facilitates good profiles and optimal use of raw materials
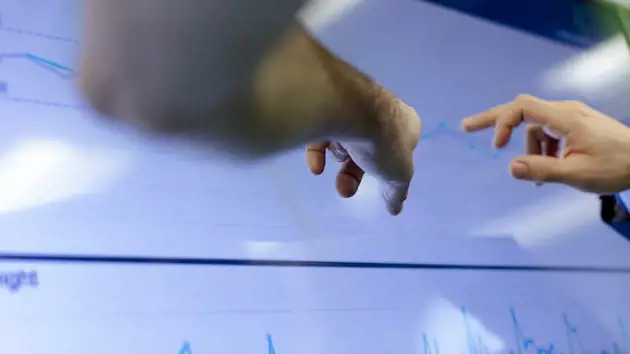
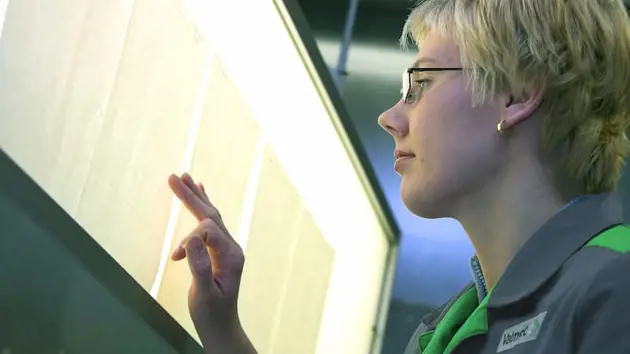
Forming section configuration optimization
Flexible Forming System optimizes the forming section configuration for each specific paper grade, while gaining quick, automated positioning during grade changes. Upgrade existing fourdrinier equipment with an adjustable table setup that is customized to your wet end process.
Cost savings with Breast Roll shaker 120
Formation is one of the most important structural properties of paper and paperboard. It affects several of the properties important for final uses, such as strength and visual properties. Valmet Breast Roll Shaker is an effective solution to improve the sheet forming process. It improves formation by creating shear forces in the web to break up large flocs.
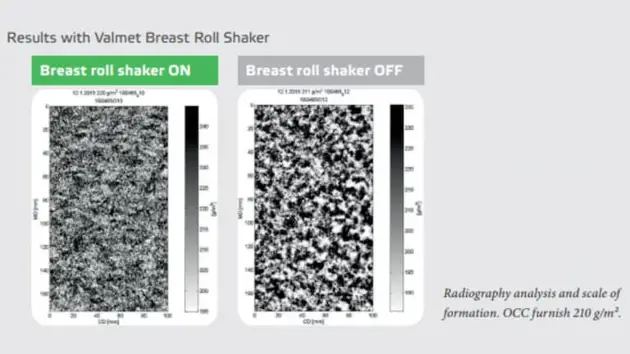
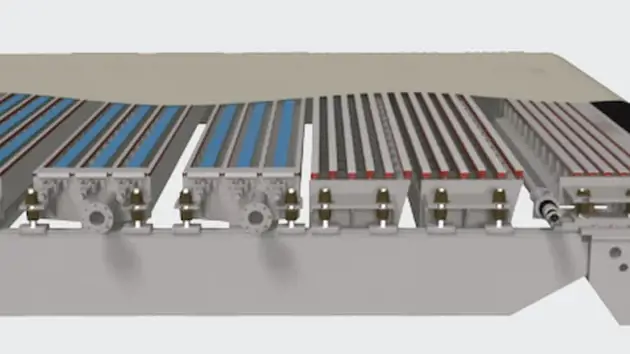
How to optimize your forming table
The Valmet FFS® is custom designed to enhance your forming table performance. It consists of a combination of Flexible™ Forming Board, HydroFlex™ and VacuFlex™ units. This system, engineered to fit on your existing fourdrinier structure, offers adjustability to provide your papermakers with the ability to optimize the forming section configuration for each grade. The system can also be complemented with a Microwave Consistency Meter to give instant process feedback to further enhance the table optimization. The entire system is operated through our Valmet FFS controls package.
Do you want to know more about process upgrades?
If you wish to get further information like technical specifications, need a quotation, or wish to discuss different solutions, fill in the contact form and our experts will contact you shortly.
Contact usReferences and articles
