Roll covers for board and paper making
Increased production efficiency with Valmet’s roll covers
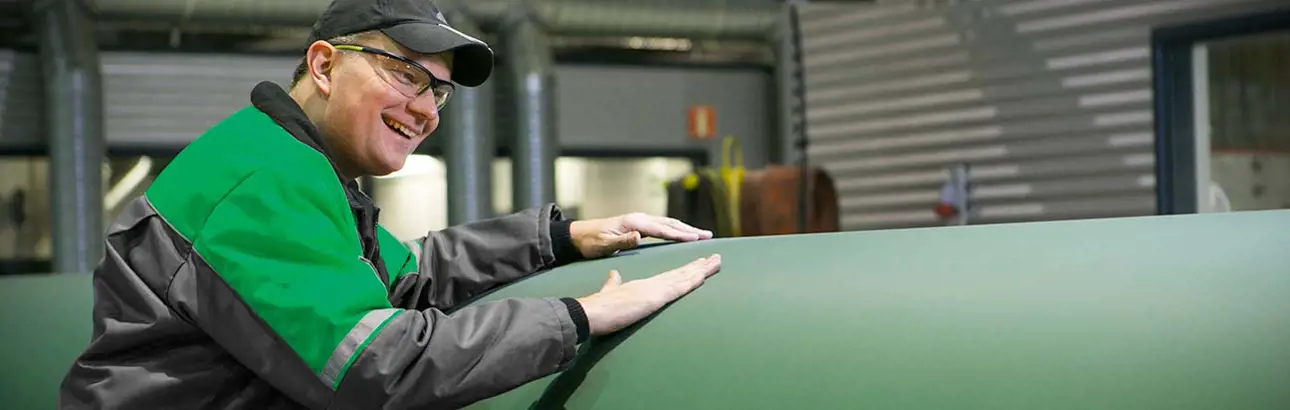
Valmet’s long experience in the papermaking industry and broad process expertise help you to choose the right roll cover for each board and paper making application. Our roll covers and coatings are based on state-of-the-art polymer and thermal coating technologies that provide excellent wear resistance, stable roughness and hardness, and durability in demanding operating environments, enabling trouble-free run periods.
Durability for long lifetime
Long grinding intervals
Optimal board and paper quality
The right cover solution for each process condition
Modern board or papermaking lines include hundreds of rolls operating in different positions. Each position has its own operating environment, which the rolls and their covers must meet. The major technical parameters for roll covers to be considered in papermaking applications are abrasive contact, local moisture level, temperature, mechanical load and the chemical environment. Good wet condition solutions may differ markedly from solutions which work best in dry conditions.
Roll cover wear is also an important issue to be considered in developing covers for different applications. Development at Valmet is based on longstanding know-how in material testing in the laboratory, as well as experience of real life applications. Depending on roll position and cover type – hard ceramic or soft polyurethane, for example – the cover behavior and actual wear phenomena are different, and finding an optimum solution requires specific know-how and understanding.
Questions?
If you wish to get further information like technical specifications, need a quotation, or wish to discuss different solutions, fill in the contact form and our experts will contact you shortly.
CONTACT US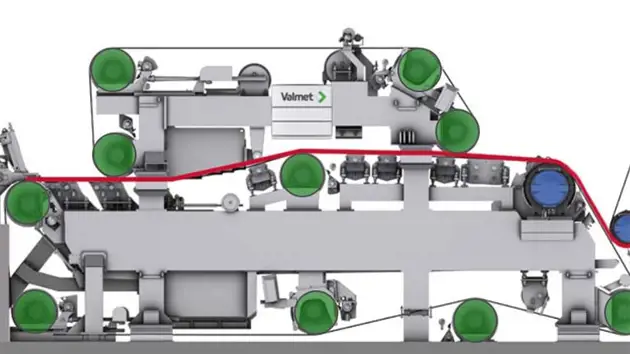
Explore our roll cover products from interactive demo.
By exploring this roll cover application tool you can easily see different cover options for every board and paper making process.
Start exploringiRoll technology for controlling paper and nips
Valmet roll covers can be used with iRoll – the most versatile and sensitive online profile measurement tool in the industry. This technology provides real-time insights into the papermaking process, making it possible to adjust and optimize performance to the highest level. Valmet's latest Industrial Internet offering combines process technologies, services and automation to provide applications and services to improve the reliability and performance of your processes. Customers can also have remote monitoring and real-time support from Valmet’s experts through the Performance Centers.
Valmet's iRoll is the fastest and most sensitive on-line profile measurement tool in the industry. iRoll technology enables to improve production efficiency and product quality by assuring optimal runnability of paper and board products
Close to you through 26 roll service centers
Our global roll workshop network around the world ensures professionals can easily carry out roll cover inspections; perform onsite coating, patching and repair services; and provide application support and general troubleshooting in your location. We also offer support ranging from grinding, recovering, and servicing rolls, to complete roll service management
Valmet Rolls and Workshop Services is a winning combination of the latest technology and rock-solid maintenance expertise. We help you eliminate unplanned shutdowns, increase the running times of rolls and equipment and improve the end product quality.
A more sustainable future with a new generation of roll cover materials
A major part of the raw materials used in roll covers – polymers, resins and other industrial chemicals – has traditionally been manufactured from fossil-based raw materials, and refined and processed from crude oil. Valmet is now taking a giant leap toward a more holistic approach with a focus on sustainability, aiming to replace as many of the roll cover raw materials as possible with more sustainable alternatives. The target is to use recycled materials and renewable resources, and more broadly to save energy.
Using recycled consumer plastic or glass as the reinforcing fiber or filler in composite roll covers, or bio-based resin and hardener in the polymer matrix, are good examples. What are the benefits of bio-based materials?
“They remove the dependency on crude oil,” states Dr. Jani Turunen from Valmet. He continues: “We only approve renewable materials derived from non-food chain plants or plant parts, meaning their use does not affect global food production. Cultivation and harvesting of plants must not endanger the growth of natural forests either. In the best cases, bio-based materials can be produced from plant parts that would otherwise be waste. Lignin, carbon black made of lignin and nanocellulose are good examples, and all three can be utilized as reinforcing fillers in roll covers.”
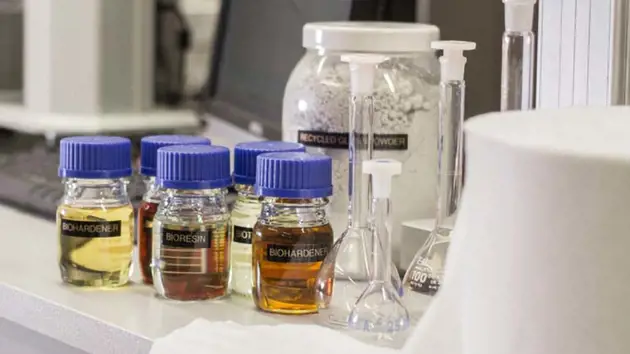
keyboard_arrow_leftBack
{{currentHeading}}
{{productForm.Name}} {{"("+productForm.Size+")"}}
Start the discussion about roll covers
Are you interested in learning more about paper machine roll covers and coatings? You're in the right place! Discover the best paper machine roll covers and roll coatings to support your production.
Rolls are the backbone of the papermaking process. Since the invention of the modern paper machine, they have been crucial in ensuring efficient and economical production. From simple felt guiding rolls to more demanding process rolls like press center or film sizing soft rolls, each type of roll and its cover must perform flawlessly. This highlights the importance of rolls in papermaking.
Modern papermaking lines feature dozens of rolls, each operating in unique positions with specific requirements. Roll covers and coatings must withstand various technical parameters, including local moisture levels, temperature, mechanical load, chemical environment, and wear. These diverse roles and requirements place high demands on cover materials.
Valmet has been a pioneer in roll cover development for decades. Valmet: leading the way in roll cover innovation through our cutting-edge roll cover solutions, including polyurethane, composite, and rubber covers, as well as hard coatings. With a global network of over 26 roll service centers, Valmet offers comprehensive roll covering and coating services, including inspections and grinding. We help you find the optimal roll cover or coating for your papermaking process.
Ready to enhance your papermaking process? Get in touch with our experts. Contact us today to start a discussion with our roll cover experts!