Boosting coating performance with intelligence
The UPM Kaukas mill in Lappeenranta, Finland, has been able to enhance web handling, runnability and roll cover performance by using Valmet’s intelligent roll cover solutions in the demanding coating process.
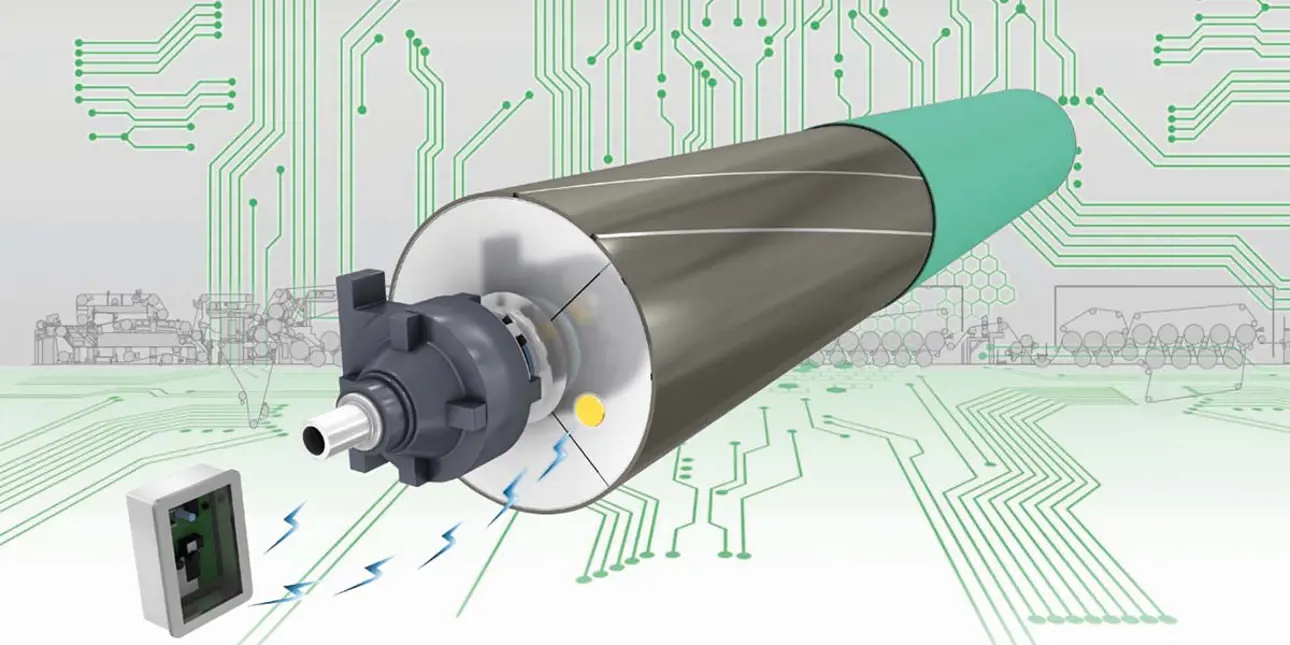
UPM Kaukas operates the Off-Machine Coater 1 – incorporating both film sizer and blade coating. The mill produces LWC and MWC paper, and demands excellent quality and maximal efficiency. It was decided to work with Valmet to update the roll covers and utilize iRoll technology.
“There were often cracks and wear on the original sizer rubber covers, leading to sheet breaks and short roll running intervals. Lightweight paper grades were especially challenging from the runnability perspective when we started up the coater and tried to make the sheet run stably at the sizer nip,” recalls Production Manager Tommi Seppälä. The blade coater area needed attention too. The rubber covers suffered significantly from visible uneven wear on the edges, resulting in rolls needing to be changed.
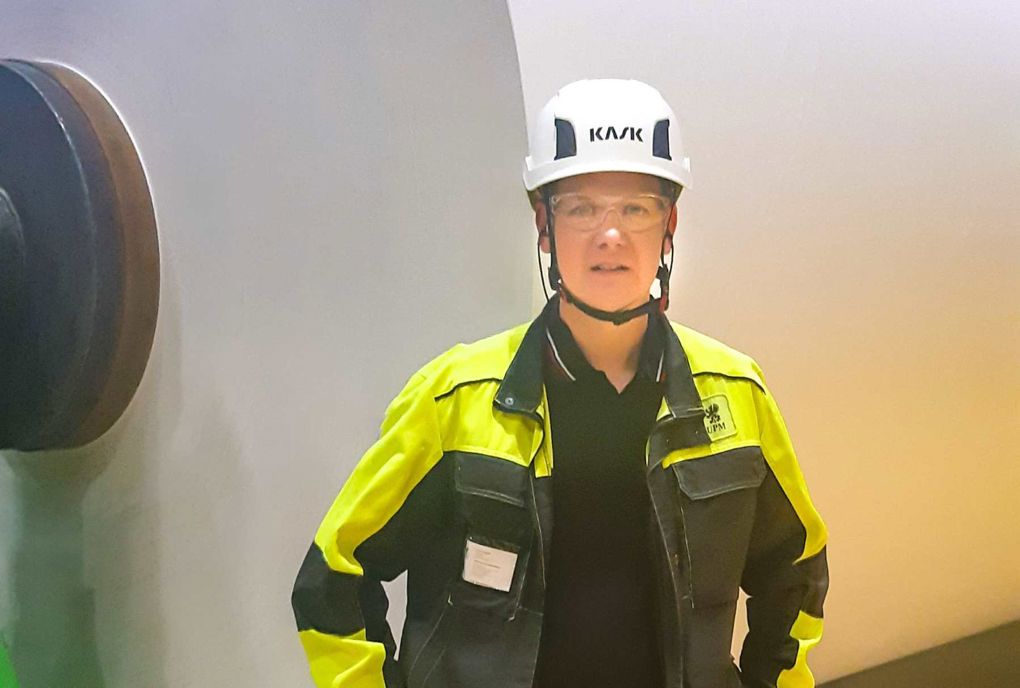
There's much potential for further ideas for using the sizer, blade coater and tension profile data," says Tommi Seppälä, Production Manager, UPM Kaukas.
Polyurethane covers and online measurements
In cooperation between UPM and Valmet, the roll cover selection was updated. The first item was to switch from traditional sizer rubber covers to Valmet Sizer Roll Cover CF covers. This extremely wear-resistant polyurethane roll cover is designed for film coating and surface sizing. It features high-quality coating film formation for ease of operation.
To optimize sizer runnability, an iRoll Sizer system was included in the roll covers. Measuring the nip load and applicator rod profiles online helps optimize nip loading settings for the best runnability, avoiding wrinkling and sheet breaks. In addition, an iRoll Tension with a Valmet Guide Roll Cover GC was installed to monitor online the profile of the paper unwound at the unwinder. This allows the monitoring of the impact of the incoming sheet on sizer area web handling.
Nip management with online data
Another important step was to change blade coater backing roll rubber covers to Valmet Coater Roll Cover CC polyurethane. Its superior wear resistance extends the operating period, reducing the need for roll replacement and grinding. An additional benefit of high wear resistance is the stability of profiles by avoiding worn out spots in the cover, thus avoiding coat weight profile effects. For online monitoring of the coater blade profiles, an iRoll Coater system was included in Valmet’s delivery.
Longer running intervals, better stability
Seppälä lists the results: “We’ve seen the biggest improvement at the sizer. With the new polyurethane covers, resistance to roll cover damage is better, enabling longer running times. With the iRoll system as the nip management tool, our operators can see the nip profile online on the control room displays and optimally adjust the loading. This helps get the coater up and running faster, as the first 10,000 meters are typically the most critical phase. Better roll cover stability also helps achieve this target."
Excellent profile stability is important in the demanding blade coating process. Valmet Coater Roll Cover CC and iRoll Coater blade profile measurement provide effective tools for this.
Running intervals have also been increased in the blade coaters. The iRoll Coater measurement system provides online information on the coater blade loading level and blade profile – information that can be utilized for maintenance support or condition monitoring. “Whereas rubber covers typically used to last from two to four months, we’ve now been able to run the new covers for more than a year with stable surface properties,” Seppälä reports.
The mill plans to integrate the iRoll measurements more deeply with its automation systems. This will make it possible to collect longer-term history data and combine information from iRolls with all QCS profile measurements for a more thorough analysis. “Visualized operator access to the data is important, but more data can also lead to the creation of new tools for maintenance. There’s much potential for further ideas for using the sizer, blade coater and tension profile data,” Seppälä concludes.
Valmet Sizer Roll Cover CF offers long running intervals and reliable operation with both smooth and grooved rods.
Related articles