Selecting the right pressing technology for your tissue machine
Press section
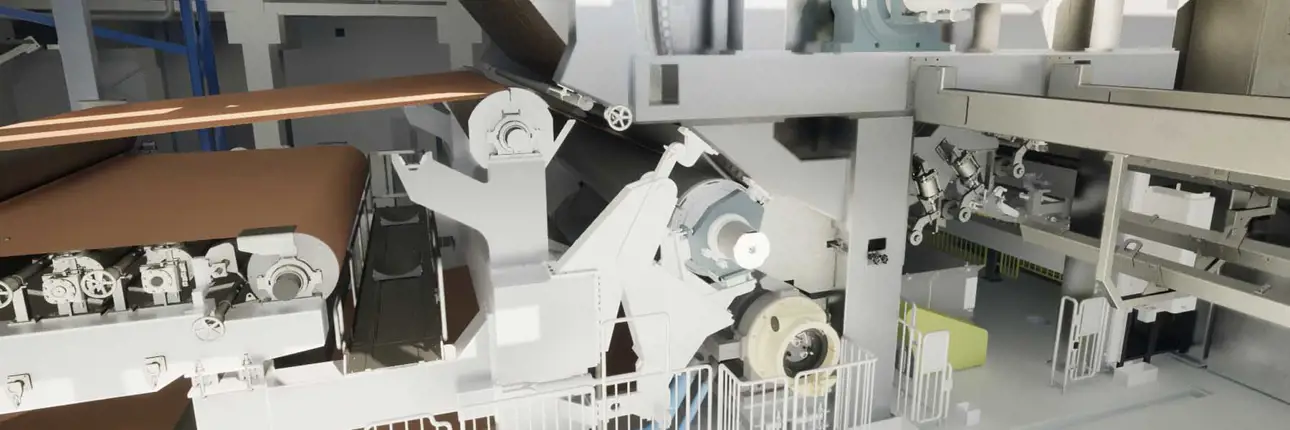
The pressing section is a crucial part of a tissue machine, playing a vital role in the production of high-quality tissue products. This section is responsible for removing water from the paper sheet, enhancing its strength, and improving its overall properties such as tissue quality, softness, and bulk. Understanding the pressing section is essential for optimizing the tissue manufacturing process.
Explore our pressing products
The primary function of the tissue machine press section is water removal, where wet pressing enhances sheet dryness to optimize paper machine drying capacity. Energy conservation is increasingly crucial today and will grow in significance in the future. Additionally, the press section significantly influences tissue quality in terms of softness, bulk, and machine performance.
Controlling water removal for improved paper properties
The importance of the pressing section cannot be overstated. It directly affects the final product quality, productivity, and efficiency of the tissue machine. By controlling the water removal process, the pressing section ensures the desired moisture content is achieved, resulting in improved paper properties and reduced drying costs.
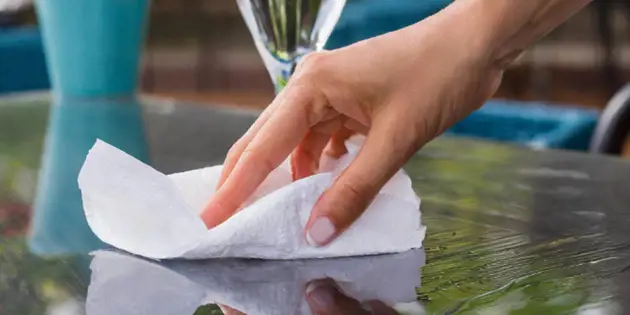
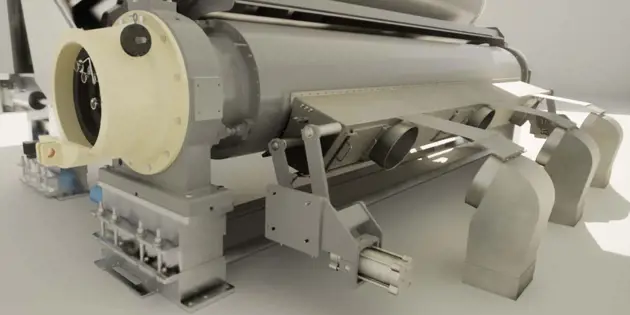
Understanding the various techniques and technologies
Various pressing techniques and technologies are employed in tissue machines. These techniques include suction pressing, shoe pressing, and nip pressing, each offering unique advantages and characteristics. By understanding the different pressing techniques, tissue manufacturers can choose the most suitable technology for their specific requirements.
Valmet offers a range of advanced solutions for the pressing section of tissue machines. Our innovative technologies, such as the Advantage ViscoNip press, ensure optimal dewatering and paper properties while maximizing energy efficiency. With Valmet's expertise and reliable equipment, tissue manufacturers can achieve superior results in terms of productivity, paper quality, and cost savings.
The importance of fabrics and roll covers
The selection of the right fabrics is essential. The choice of fabrics should take into account factors such as fiber type, machine speed, and desired paper properties. The fabrics should have the right surface characteristics and permeability to effectively remove water from the paper web.
The design and condition of the roll covers play a significant role. The roll covers should have the right surface characteristics to ensure efficient water removal and prevent sheet sticking. Regular inspections and maintenance of roll covers are necessary to avoid any issues.
Explore more!
Maintenance plan for best efficiency
Best practices for maintenance and operation of the pressing section should be followed. This includes regular cleaning, lubrication, and inspection of the equipment. Proper training of operators and regular performance evaluations can also contribute to the optimal functioning of the pressing section.
By considering these factors, troubleshooting pressing issues, and following best practices for maintenance and operation, tissue manufacturers can optimize the pressing section of their machines, resulting in high-quality products and improved overall performance.
Explore our service offerings
Q&A section - Learn more about the press section of a tissue paper machine
Q: What is the role of the pressing section in the tissue machine?
A: The pressing section in a tissue machine is responsible for removing excess water from the tissue sheet formed in the forming section. This process is crucial for achieving the desired thickness, density, and strength of the final tissue product.
Q: How does the press section impact paper quality and properties?
A: The press section enhances paper quality by removing water, consolidating fibers for improved strength, enhancing formation, controlling bulk and density, improving surface properties, and increasing dewatering efficiency.
Q: What are the key components and functions within the pressing section?
A: Key components of the pressing section include press rolls, felts, and doctor blades. Functions include water removal, fiber consolidation, and sheet compaction.
Q: What are the factors to consider for optimal pressing performance?
A: Factors for optimal pressing performance include press nip pressure, dwell time, felt design, drainage characteristics, and sheet moisture content.
Q: What are the best practices for maintenance and operation of the pressing section?
A: Best practices for maintenance and operation of the pressing section include regular cleaning, monitoring and adjusting press nip pressure, ensuring proper felt alignment and tension, conducting routine inspections for wear and tear, and maintaining optimal lubrication of moving parts.