Everything is possible, from small targeted upgrades to rebuilding of the entire dryer
Valmet performs the full range of conversions and upgrades, to make sure the pulp dryer is perfectly adapted to each customer's needs.
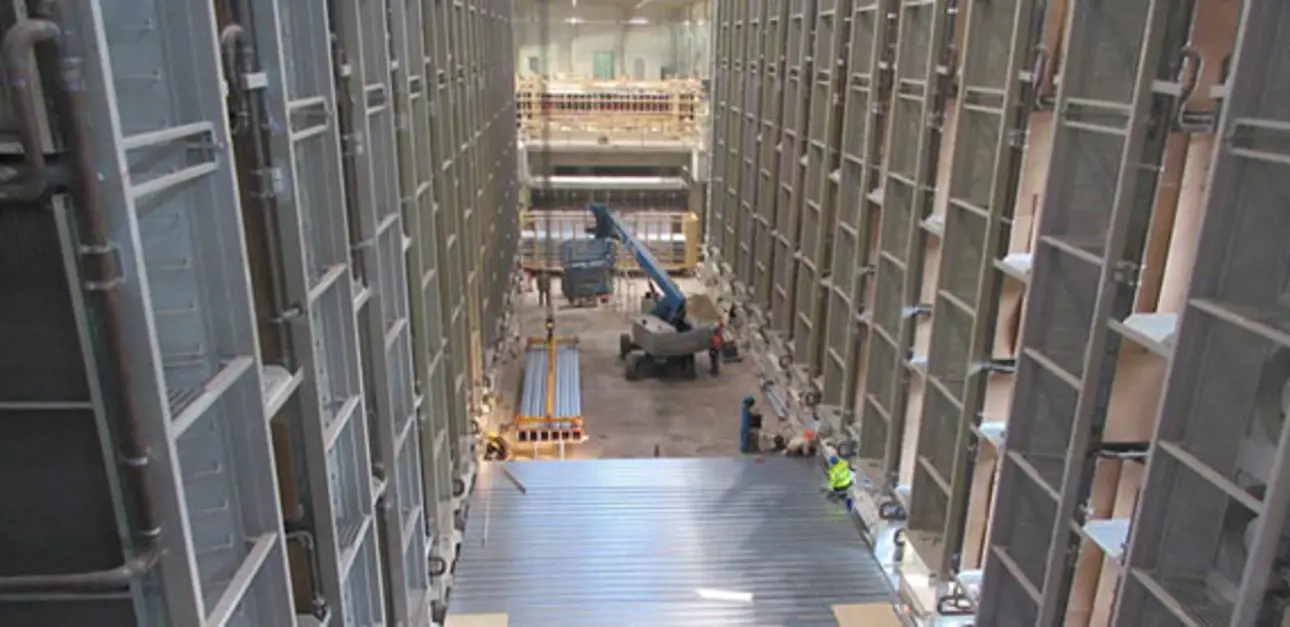
“We do many small and medium-sized rebuilds on existing pulp dryers, and also get many large assignments where the entire dryer is essentially rebuilt from scratch. Increasing production is the most common reason for such projects, but they can also be aimed at for example reducing dust formation or streamlining the workload for operators. Wear and outdated technology are further reasons for a dryer to be rebuilt,” says Project Manager Kari Koski.
Kari Koski |
|
![]() |
A concept that is tailored to each customer
Valmet's Airborne Dryer concept is module-based and can be adapted to each customer and each dryer, no matter if the dryer is relatively new or old, large or small.
A typical rebuild might consist of replacing or adding blow boxes, fans and end towers to increase the drying capacity. The conversion may also include upgrading to automatic tail threading to minimize downtime. The dryer can also be upgraded with smart technology that reduces dust formation and increases runnability.
“All rebuilds are quite different,” comments Koski. “It might be, for example, that we replace fans, steam coils and access hatches, or that we upgrade tail threading to automatic. It can also be about building new drying decks in the upper part to increase evaporation capacity or improve heat recovery. No matter what the issue is, with the latest innovations we can make any dryer maximally competitive.”
An important task for Valmet is to reduce its customer’s investment and operating costs. Therefore, all conversions and upgrades are tailored to keep the project's total costs to a minimum, while the technology added must provide the lowest possible operating costs.
Booster dryers – Increased production via a space-efficient solution
You may have several reasons to rebuild a dryer, with the most common being to raise your production capacity. With Valmet's Booster Dryer solutions, pulp output can be increased through a targeted extension that is placed either on top of, after or inside the existing dryer. Which one you choose depends on your particular needs.
Adding a Booster Dryer extension on top of or after the dryer can be done on almost any pulp dryer. On the other hand, if you want to add capacity inside the dryer, space must be reserved for that during the original planning when it is built. In that way it is already prepared for a capacity increase, which is easy to do when needed. An additional advantage with this solution is that there is no necessity to increase the physical size or footprint of the dryer. Due to the extreme flexibility it offers, and since each project is unique, there has been great interest in the Valmet Booster Dryer for expansions.
Rebuilding and upgrading of "non-Valmet" dryers
It is not just Valmet's dryers that are being rebuilt and further developed.
“More and more assignments involve rebuilds of non-Valmet dryers. The mill wants to keep the dryer frame but upgrade it with selected parts from the Valmet Airborne Dryer technology. Customers are well acquainted with our know-how and our technical innovations,” says Koski. “This type of assignment is extra stimulating because we feel the confidence to further develop a technical solution that is not originally our own. To do so we start with a feasibility study, where we thoroughly analyze the existing dryer and then carefully develop our plan. This lays the foundation for a successful end result.”
When the unexpected happens
A conversion project can be extra demanding when the work is carried out while the dryer is in operation. Therefore, planning and project management are very important. Kari Koski explains: “Careful planning and proactive project management are of great importance for the project to run smoothly and well. We have extensive experience of carrying out renovations and planning the work so that the time for downtime is minimized.”
But even if everything is prepared and planned in detail, unexpected things can happen.
“Regardless of whether it’s on a weekday, a Saturday evening or a holiday we always act quickly. Trust is earned from our customers and we ensure that this trust is well managed,” concludes Kari Koski.