Aiming higher with an optimized causticizing process
Online liquor analysis and advanced controls stabilize the liquor conversion chain and increase white liquor active alkali by 4,7 %. With extra process visibility problems were uncovered, leading to further improvements and ROI potential.
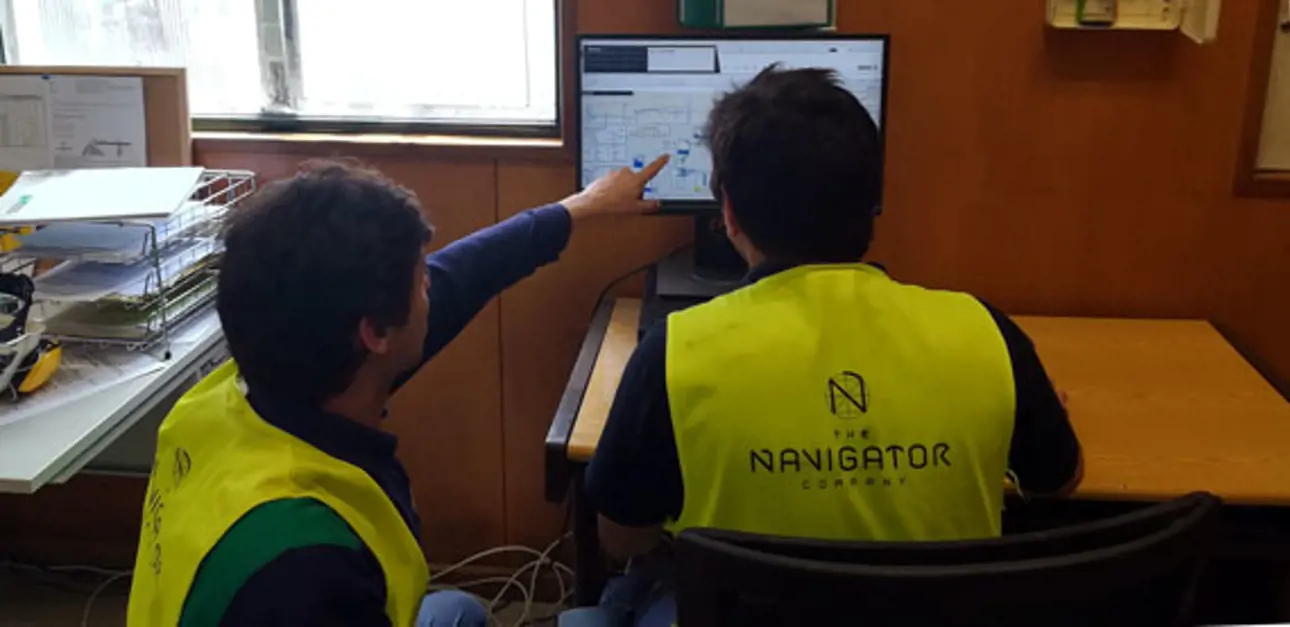
Online liquor analyzers and advanced process controls increase stability in pulping and recovery cycle operations, which improves operational efficiency and quality, and decreases material and energy consumption. As a secondary benefit, they also serve as a valuable diagnostics tool, uncovering previously unseen process instabilities and limitations.
This has been the case at the Navigator Company’s Cacia mill in Portugal, which has an annual output of about 370,000 tonnes of bleached eucalyptus pulp, intended for processing into specialty papers such as high-quality décor, filter, cigarette and tissue paper. In 2018, Valmet commissioned a multi-point online recovery liquor analyzer and causticizing optimizer in the causticizing plant, resulting in significant process improvements.
The Valmet Recovery Liquor Analyzer collects samples at six locations.
All targets achieved
Fernando Martins, Recovery Plant Manager, summarizes the reasons behind the investment decision: “We planned to obtain better white liquor quality, stabilized causticizing efficiency, and sulfur and alkali indices, plus lime and natural gas reduction.”
In achieving these goals, he sees an advantage in Valmet’s comprehensive approach, which offers analytical instrumentation, controls and an operator interface in one supplier package.
“We made a reference visit to a mill, where we saw the exceptional results that they obtained with this solution. It was the only equipment on the market with such good results,” he concludes. He also notes that the project team “spoke the same language as the operators,” thus promoting a successful outcome.
After only a few months of operation, the results of the project were seen in the increased stability of the entire process from green to white liquor, consistently higher causticizing efficiency, more stable white liquor with a higher active alkali and other operational benefits.
The mill’s controls and operator interface are based on Valmet DNA, linked to an existing distributed control system (DCS).
Stabilizing controls
The process stabilization starts at the dissolver, where smelt is diluted with weak white liquor. The combined chemical components of the green liquor TTA from the smelt and dilution white liquor are measured by the alkali analyzer. TTA optimizing controls continuously monitor the TTA correlation with density measurements, and the density setpoint is adjusted to keep the TTA constant. In addition to the TTA control from the dissolving tank, the TTA is fine-tuned just before the slaker.
The online liquor measurements and advanced process controls have allowed target shifting of key process indicators.
Once the input of green liquor has been stabilized and the strength maximized, the control of the slaker is the most critical in the chemical conversion process, because it sets the initial reaction rate, which then carries through to the causticizing vessels and the final white liquor a couple of hours later. The ratio of lime to green liquor is determined by the rise in temperature from the green liquor to the top of the slaker. This deltaT is created by the exothermic reaction between lime and water. The control responds quickly to the quality of lime feed, regardless of the source. This control is supervised in a cascade loop by feedback white liquor measurements taken downstream.
This temperature rise model is used when the slaker is not boiling. If it boils, the unknown part of the exothermic reaction energy is used to evaporate water. When this happens, another strategy must be used. At Cacia, the advanced process control switches automatically to the boiling mode to maintain white liquor quality.
Advanced controls have stabilized KPIs including, from top to bottom, TTA of green liquor to the slaker, AA of white liquor and causticizing efficiency
Work in progress
The online measurements and advanced controls have stabilized the entire chemical conversion process and allowed the target shifting of key process indicators. With improved stability, overliming has also been eliminated.
Francisco Figueiredo sees the project as a success: “Valmet provided very good team support. They were always available and solved problems quickly.” Project Process Engineer Fabio Branco adds: “It was a very easy project. All the schedules were met. Navigator and Valmet worked together to solve every challenge.”
However, the improvements in the process will not end with the acceptance of performance guarantees. Heikki Imelainen, Valmet’s Senior Application Engineer, explains the project implementation philosophy: “We study the entire process when we tune any advanced process controls on the site – not only the area under control, but also all input materials and the process after the last control point.”
The mill staff and Valmet have worked together to diagnose some previously unseen process limitations which, when solved with the planned improvements, are expected to lead to further benefits and more return on investment.
Article first published in Paper 360.
Text and photos Mark Williamson
Related content