Below the noise limit
Vantaan Energia, one of Finland’s largest urban energy companies, set tight noise limits for equipment suppliers at its new waste-to-energy plant in Vantaa. With new-generation Neles™ Q2 ball valves it is possible to run the plant’s steam network at a nearly 30 dB lower noise level than with standard valves.
Decibel meter digits stop at 74.5. We are in the turbine hall of Vantaan Energia’s new waste-to-energy plant to see how the low-noise Neles™ Q2 ball valve is functioning. Taking into account the 5 bar pressure of the 200°C steam flowing in the pipes and the background noise caused by the process environment, the result is surprisingly good. Probably better than anyone present dared to expect.
Three tough challenges
Noise, smells and emissions are three factors that must be controlled at a waste-to-energy plant. Markku Vuorisalo, who is in charge of the plant’s automation maintenance, says that in Vantaa all of them are well under control.
“It is a question not only about the environmental permits but also about prejudice from surrounding neighborhood and our staff’s working environment,” he says. According to Vuorisalo, no harmful emissions, smells or noise are emitted outside the plant walls. Everything possible has been done inside the plant, too.
”With regard to smells, there are of course challenging places, but our people seldom work in them and when they do, they protect themselves carefully against the smells,” he explains. ”As far as noise goes, our plant can perhaps not be described as quiet but wherever possible, we have tried to lower the noise level with technical solutions.”
It is single components that have an impact on the total noise level. If the earlier mentioned steam valve would be a standard one, it would make a lot of noise at a high frequency, and the noise would not stay within the plant walls. Now it is possible to carry out a conversation right next to it.
In a real process environment
The 80 dB limit that Vantaa set for the steam valve is extremely tight. In everyday language, it is considered the noise limit. In occupational safety and health, 80 dB is the level when earmuffs must be acquired for the staff. When 85 dB is exceeded, the earmuffs must be worn. The decibel scale is logarithmic and difficult to understand for a person unfamiliar with it. For the human ear, an increase of ten decibels means doubling the noise volume.
The measurements are highly important for Valmet since the Q2 valves at the Vantaa waste-to-energy plant are the first ones installed in Finland. The plant was inaugurated in September 2014, and the valves were installed in the previous spring.
Markku Vuorisalo does not want to draw any conclusions but emphasizes that there have been no problems.
“History data provided by the automation system informs me that the package consisting of the valve and the actuator behaves very well although the control is not yet quite optimally tuned.”
Investment based on the overall technological concept
Although we are now interested in the Neles™ Q2 control valves, these two valves represent just part of Valmet’s delivery of 28 control valves. Markku Vuorisalo reminds us that the control valves are primarily carrying out the task for which they were acquired. It is possible to control steam pressure and flow in many ways. Noise represented just one acquisition criterion, and the deal was awarded to Valmet based on its overall technological concept.
A new-generation Q ball
Yli-Koski admits that the result exceeded even the valve designers’ expectations. He reminds that noise attenuation decreases valve capacity no matter how it is done. “The new Q2 trim has a two-stage structure and a capacity that is quite OK compared with the standard product.” The new generation Q2 valve features many smart features and patents.
“Its design was started afresh. The structure is totally new and completely different from its predecessor,” Yli-Koski says.
The ball valve is made of stainless steel and available in sizes from DN50 (2”) to DN900 (36”) for pressure classes from PN10 to 100 (ASME 150 to 600). Special materials are available on order.
Making use of mixed waste
The Helsinki region got its long-awaited waste-to-energy plant when Vantaan Energia started up its new plant in early September 2014.
The main part of the waste combusted at the plant consists of mixed household waste collected in the Uusimaa region. Whereas it was earlier landfilled, it is now turned into electricity and district heat, covering about half of the needed district heat in the city of Vantaa.
Utilization of waste replaces fossil fuels and lowers Vantaan Energia’s carbon dioxide emissions annually by about 20%. Plant efficiency, 95%, ranks among the highest in Europe. The annual 320,000-ton mixed waste amount is no longer landfilled. In fact, landfilling of mixed waste was banned in Finland in 2016.
About 150 waste trucks arrive at the plant on every working day. They dump their loads in a hall that is under negative pressure and thus does not emit any smells to the surroundings. Negative pressure is created by utilizing the process as combustion air for the boiler is taken from the waste bunker and the reception hall.
The bunker has a capacity for about ten-day production. Source-separated waste is not further separated at the plant but combusted well mixed as such.
Waste is combusted in two grate incinerators at a minimum temperature of 850°C. In case it is wet or of poor quality, combustion is secured with gas burners. The combustion lines are identical, and flue gases are cleaned and measured redundantly.
Steam is superheated in the waste incinerators and led into a heat recovery boiler where is further superheated with a gas turbine and auxiliary boilers. Then it continues its journey to the steam turbine and further through heat exchangers to the network.
Incinerator slag and fly ash are transported to the Ämmässuo waste treatment center where metals are separated. The end product from flue gas cleaning is treated at the Ekokem plant.
vantaanenergia.fi/en
Text: Tapani Leppänen
The article has been translated from an article shorted and published in the Kenttäväylä magazine issue 2/2014.
Text originally published in 2020, and slightly updated in April 2022, due to the company name change to Valmet.
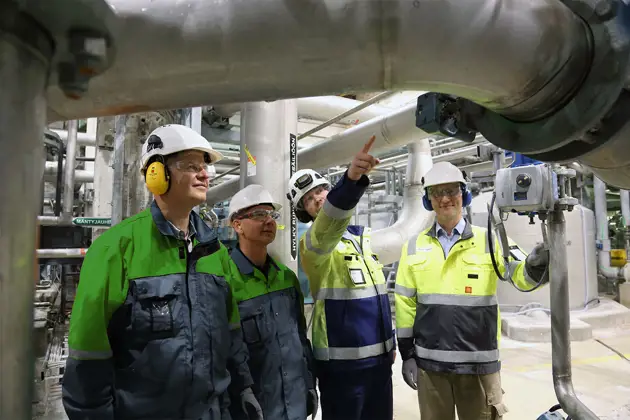
Subscribe to our newsletter
Subscribe now to flow control newsletter and receive the latest insights directly to your email.
SubscribeRead more about waste-to-energy and power plant success stories