Finding a better way forward with Aqua layering headbox technology
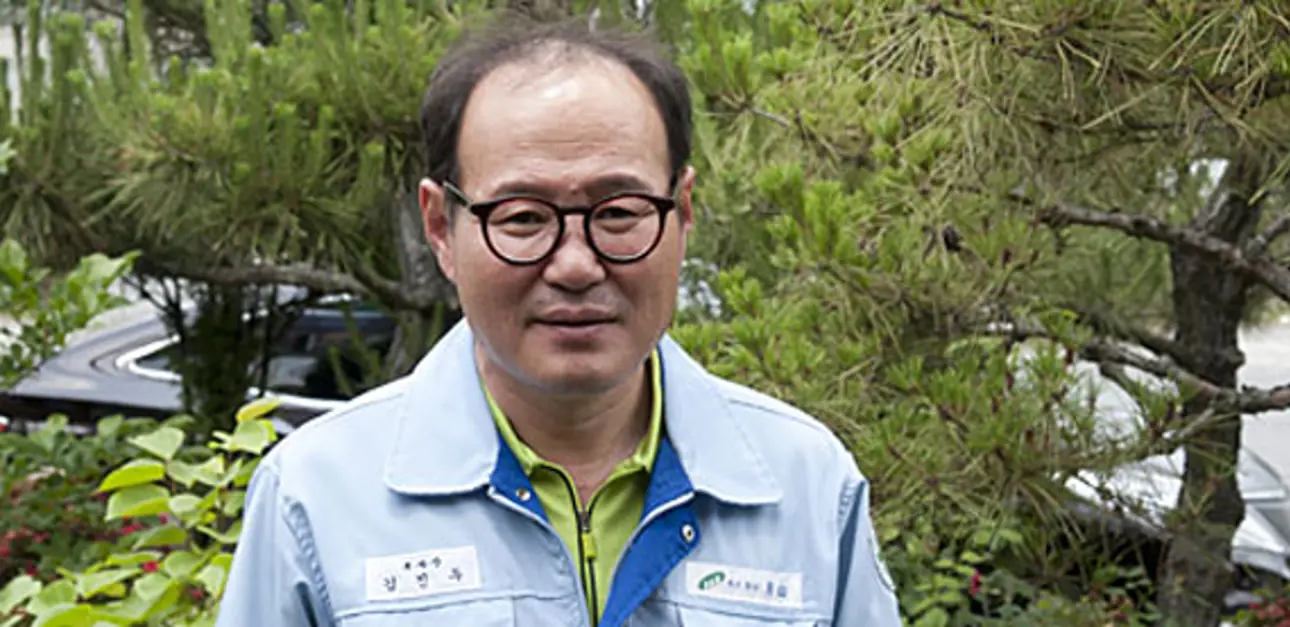
Mr. Jin Doo Kim, Vice President of Dong Il Paper, explains that Dong Il's strategy for survival is to adopt new technologies and make continuous improvements all the time.
“Gaining a competitive edge requires a creative mindset. Adopting new technologies first is a brave move that can help to differentiate your product in the marketplace. But being first does not last forever. That’s why you have to find a better way forward every day.”
That is what Jin Doo Kim, Vice President of South Korea’s Dong Il Paper believes. Dong Il’s strategy for survival is to adopt new technologies and make continuous small improvements all the time. “My point of view is simple: if you want to stay alive in the market in the future you have to differentiate,” explains Kim. “Our company can’t rely on big capital, so we have to be smarter. Talking is easy, but making a difference in the world requires hard work. I want to encourage our people to look for new things.”
The latest project that Dong Il took on was to invest in Valmet’s advanced headbox technology. PM 1 in Wolsan started up again after a wet end rebuild in January 2014. Valmet's delivery covered the key components: an innovative new two-layer headbox and vacuum-assisted forming board for middle ply. Dong Il had plenty of confidence to go ahead with the rebuild, as the new type of headbox was not the first new piece of technology they had adopted. Dong Il and Valmet have been cooperating for more than a decade already, which has helped Dong Il establish a competitive edge in the Korean market.
New aqua layering technology
“We are lucky to have demanding customers that want to get better-quality linerboard” Kim explains. “But using old corrugated containers as raw material naturally involves variations in quality. We want to eliminate variations from the end product as much as we can. To solve this challenge we realized we needed something totally new. Otherwise we would be just increasing our costs by using better fiber, more expensive chemistry, or more refining and thus more energy consumption.“
The answer was Valmet’s OptiFlo Fourdrinier headbox, featuring the new aqua layering technology. This novel solution provides excellent layer coverage, excellent CD profiles and excellent formation with no streaks or tiger stripes. Aqua layering technology guarantees layer coverage with a thin water layer as a headbox wedge that stabilizes the layers. The new layering technology also enables more efficient wet end starch application: starch can be fed between the layers. This provides a chemically optimal feeding point for active starch interaction and improved end product strength.
30% less starch
Jin Doo Kim is pleased with the new headbox combined with the new Valmet Vacuum Forming Board*. The new technology has proven to be beneficial, and the mill has already seen a significant increase in the strength properties of the end product. “Unlike with conventional technologies, a rapid starch feeding response can be measured when starch is fed through the aqua layer. In both cases compression strength can be improved by 15%, but almost 30% less starch is needed with aqua technology. Even in chemically challenging process conditions, this technology produces great results," Kim says. The new type of layering allows the quality and strength properties to be adjusted for cost savings. Dong Il has been carrying out raw material optimization testing, such as feeding functional additives or even reject between the layers. “There is a lot of potential with this technology, and I believe we haven’t yet found the ideal combination to capitalize on the benefits of the aqua layering. Cost savings can be achieved while maintaining strength.”
Power of co-operation
“We at Dong Il believe that working together with Valmet has increased our people’s skills. Even I have grown and learned!” Kim laughs. “Valmet always have the right people with a deep understanding to resolve any issues with paper technology.” Jin Doo Kim explains that over the years the mill has made quite a big technological leap. They started by buying a small machine running at 400 m/min and set the target of getting it to run at 800 m/min with Valmet’s help. “I don’t think anyone in the Korean market thought this would end well. They all believed that the investment was too big and the target was impossible,” Kim says. “Just two weeks after start-up we reached 800 m/min, and have been continuously modifying the machine so that now it’s running at 1,100m/min. The production has grown from 350 tonnes per day to 1,300 tonnes per day. This is what we can achieve when we are supported by Valmet. We have developed a certain confidence in each other. If we are working on a project with Valmet, we have no doubts.”
After the rebuild the Dong Il Wolsan mill is able to produce high-quality recycled liner with lower costs.
Creating a brighter future
Going forward is a core value at Dong Il. “I really do my best to prepare for the future. We’re currently number one in Korea, but we keep on moving forward,” Kim explains. “We produce a million tonnes a year for the Korean market and the target for the next few years is to boost that by 50%.” Jin Doo Kim also sees the complexity of the industry and change in customer needs. Paper is one packaging material among many, and it has to compete against glass, plastic and metals. “Fiber-based materials account for 30% of the industry, and a little bit over 30% are plastics. The percentage of fiber-based packaging is falling every year, and the metrics for plastics is going up.
This is a worldwide trend at the moment, but why? To compete against plastic or metals we need to create fiber packages with functional layers like a water barrier. Then we can combine the two best elements – recyclability and product functionalities. It all comes back to thinking differently and to having a pioneering mindset. I believe there is great potential and we should actively develop new concepts to help us survive. It is important to build a view for the future, without hesitation.”
OptiFlo headbox with aqua layering technologyValmet's OptiFlo headbox with innovative aqua layering technology makes it possible to produce a two-layer sheet with very good layer coverage using only one headbox and forming unit. The aqua layering technology has been developed for the most challenging stratified solutions where layer purity is a key feature. It produces a perfect, disturbance-free, purely layered structure that boosts strength properties.The new aqua layering technology uses a thin water layer as a headbox wedge to stabilize layers and to form an even film while layers of stratified paper are being joined together. It prevents mixing of stock layers and also enables feeding of functional additives between the stock layers. This type of layering provides possibilities to adjust quality and especially strength properties. Cost savings can be achieved, for example, by using different furnish qualities, cheaper raw materials, and functional wet end additives between the layers. Furthermore, as layering is done with one headbox and forming section only, the investment is both cost and energy efficient. |