Energy efficient OCC line at Orora Botany Mill
Orora set tight demands for it's new recycled fiber line: high capacity (1,300 oven-dry tonnes per day) while using exceptionally dirty raw material and only one pulper station. Valmet met the needs with energy efficient system that features a three-unit de-trashing loop for efficient debris removal.
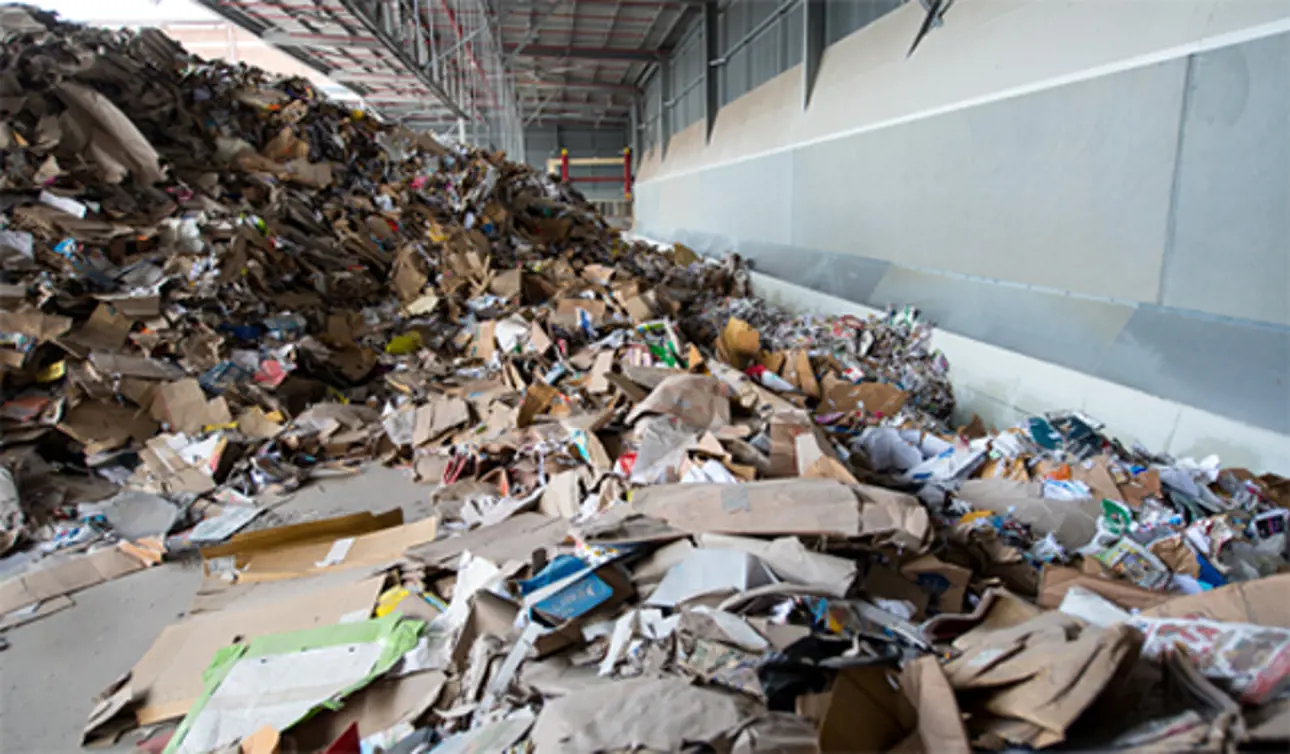
The top performing OCC line is a perfect match for Orora’s Board Machine No. 9, the Valmet supplied new papermaking line that started up in 2012. With a design capacity of 400,000 tonnes per year, B9 is the largest paper machine operating in Australia. As raw material, B9 uses 100% recycled fiber from domestic containerboard and mixed waste.
High OCC line capacity despite exceptionally dirty raw material
The recycled fiber (OCC) line at the Orora Botany mill has an OptiSlush pulper to break down the recycled material into fibers and remove most impurities. HC Cleaners remove coarse heavy particles, such as staples, stones and glass. The line has OptiScreen coarse screening, fractionation to separate long and short fibers, LF fine screening, and LC cleaners.The line has a design capacity of 1,300 oven-dry tonnes per day into the high density towers. Due to exceptionally dirty raw material, the system features a three-unit de-trashing loop for efficient debris removal. The loop system is a world first and enables maximal outthrows removal and high capacity with only one pulper station.
Low energy consumption
Orora is pleased with the performance of the OCC line. It produces very clean results with “few specks and very low stickie counts,” says Jacob Chretien. It is efficient in energy terms: “energy consumption is as low as was designed,” he says.Also wear is surprisingly low. “Wear-related issues on all components after the full-flow cleaners are much lower than we expected,” says Chretien. “The pulper, fractionation and LF fine screening equipment are all exceptional and perform equal to or better than we expected.”
![]() |
"Energy consumption of the OCC line is as low as was designed" says Jacob Chretien, GM of Technical - Paper & Recycling |
Wax is an issue for the mill. “We do struggle on occasion with wax, which is a
function of the feedstock and the amount of waxed boxes used in the Australian market,” Chretien explains. Fortunately, this is a much less significant problem than had been expected.
Recycled fiber-based production
B9 uses 100% recycled fiber from domestic containerboard and mixed waste. Some readers may not realize that Australia’s few large urban centers are widely dispersed across a vast island continent. Geography like that would normally place a heavy transport cost burden on collecting recovered fiber. Fortunately most of the recycled fiber used at the mill is conveniently drawn from the Sydney area, says Karl Achleitner, General Manager of Operations.
“Transport costs are not a significant issue,” he says. Production Manager Tero Ylikoski points out that recycled fiber can vary widely in terms of quality, and that sourcing mixed waste takes careful management, as well as making trade-offs between raw material cost and runnability. “There is a calculated risk in receiving mixed waste,” Ylikoski points out, noting the greater likelihood of finding non-fiber material in cheaper supplies.
Single supplier advantage
While machinery for most projects on this scale is supplied by several vendors, B9 was ordered solely from Valmet. Jacob Chretien, GM of Technical - Paper & Recycling, explained that Valmet was chosen to supply the complete line because it “had delivered a number of entire production lines which were similar to what we needed to meet the market requirements in Australia”.
Read more about the top-performing board machine B9 and why maintenance agreement with Valmet has made the Botany mill "the envy of the paper industry" here.