Solutions for groundwood pulp production
Cutting production costs in an energy-intensive production process
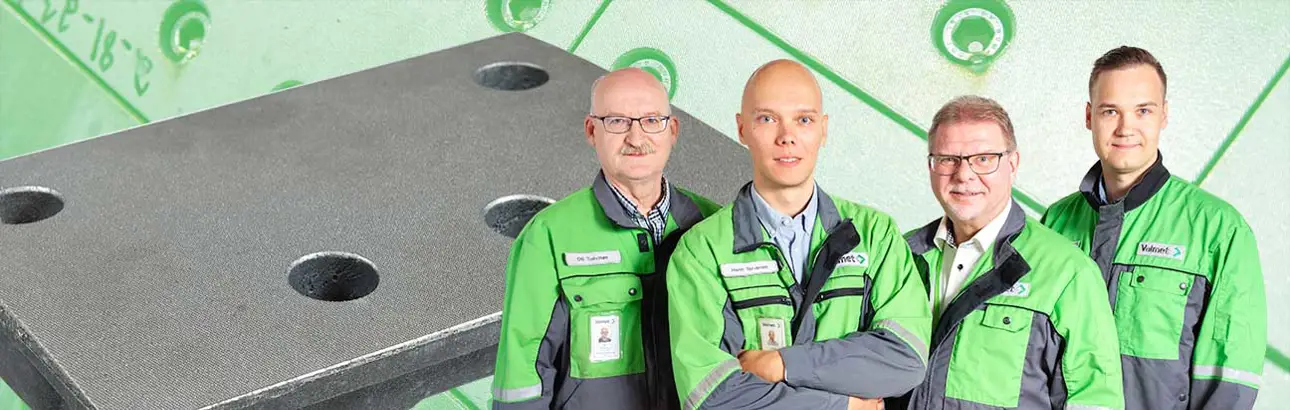
Galileo is the grinding segment concept Valmet has developed jointly with mechanical pulp producing customers. The project aimed to cut production costs in an energy-intensive production process. And, its careful aim meant the project hit the bullseye!
Energy savings
Increased production
Improved fiber quality
Reduced CO2 emissions
Verified savings
Actual experiences from more than 40 grinders all over the world show that Galileo has enabled a decrease in specific energy consumption (SEC) by as much as 25 to 35 percent.
Galileo’s secret is a steel surface coated with industrial diamonds that replace conventional ceramic stone surfaces. The diamonds are set in a specific, precise pattern depending on the wood species, process conditions and desired pulp quality. Galileo not only reduces production costs, but it also increases pulp production and provides more uniform end-product quality.
Global climate impact to reduce CO2 emissions
While saving energy, Galileo diamond grinding surfaces save around 45,000 tonnes of CO2 emissions in mechanical pulp grinding processes globally every year. This really makes a difference – the annual CO2 emissions reduction is equivalent to driving 300,000,000 kilometers in a car (producing 143 g/km CO2 emissions).
Save around
45,000
tonnes of CO2 emissions in mechanical pulp grinding processes.
Remote monitoring and continuous optimization
The remote monitoring of a customer’s process is an essential element of the Galileo delivery. By following the Galileo performance online, both the customer and Valmet gain valuable information of the grinding process and Galileo’s performance. Continuous follow-up of the process is invaluable because it enables both parties to react quickly to any process changes or upsets.
Valmet believes so strongly in Galileo’s grinder segment concept that the contracts are based on the pay-for-performance model, which places the customer and Valmet in the same boat, rowing in the same direction.
Galileo is now used in PGW and GW grinders all over the world. Valmet also now has the first order for chain grinders. This means Galileo can now be installed in any type of groundwood producing grinder.
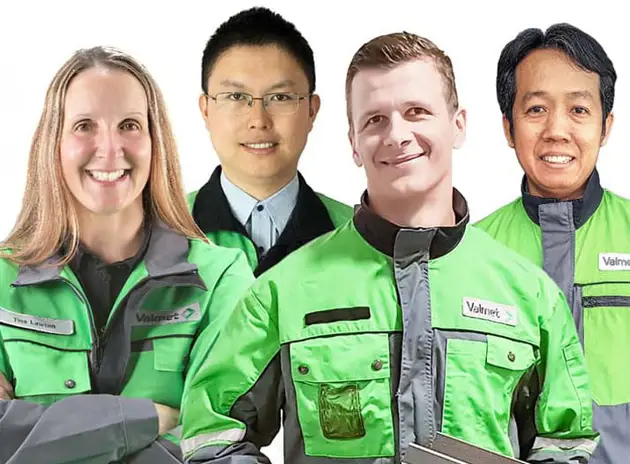
Do you have any questions?
If you wish to get further information like technical specifications, need a quotation, or wish to discuss different solutions, fill in the contact form and our experts will contact you shortly.
Contact usGalileo’s diamonds are the grinder’s best friends
The delivery and installation of the final two units at Sappi Ngodwana’s mill was disrupted by Covid-19, but the open-minded use of virtual technology and seamless collaboration between Valmet and Sappi meant the project was successfully completed on time and within budget.
Read more about Galileo grinding.
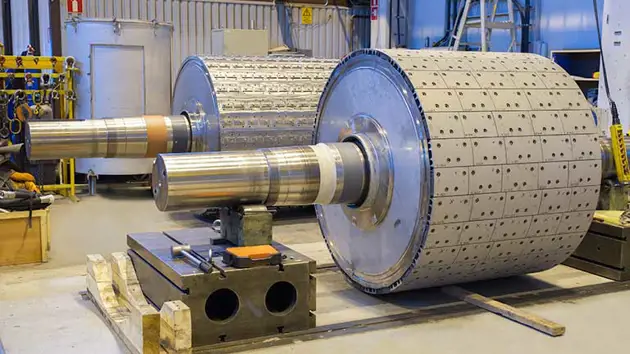

Grinding with diamonds - an award-winning innovation
With Galileo grinding technology, reductions in energy consumption can reach up to 300–500 kWh per tonne, equivalent to annual cost savings of more than EUR 500,000.
Read more about the energy saving that you can achieve:
Galileo is the latest innovation for energy saving in wood grinding
With the diamond coated surface, our customers can improve energy efficiency and the grinder’s production.
Download our brochure Valmet Grinding Surfaces Galileo
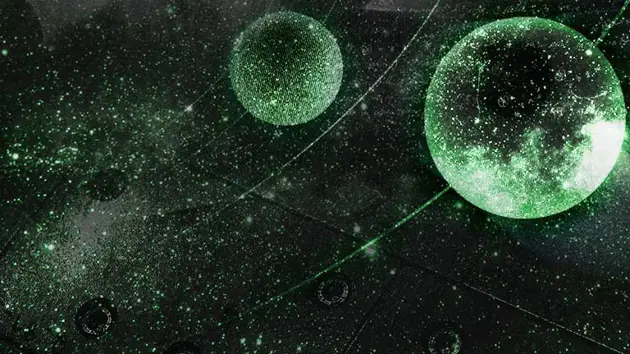
Related pages
